Welding Rod Making Machine
Introduction
Drawing, Straightening, and Cutting Machine
Mixing Machine
Slug Press Machine
Coating Machine
Baking Oven
Packing Machine
Introduction
In Welding Rod Making Machine, the wire is first drawn and cut, and then a combination of different materials is pressed onto the surface of the wire. The final step is Baking and packaging.
The Welding Rod Making Machine includes the following units: Drawing, Straightening, and Wire Cutting Unit; Mixer; Slug Press; Coating Machine; and Oven.
In this article, we will explain all the parts of this production line to provide you with a complete guide for your project. Also, to learn how to produce welding rods (welding electrodes), read this article, and to understand the key points of buying a welding rod-making machine, read this article.
The Main Parts of Welding Rod Making Machine
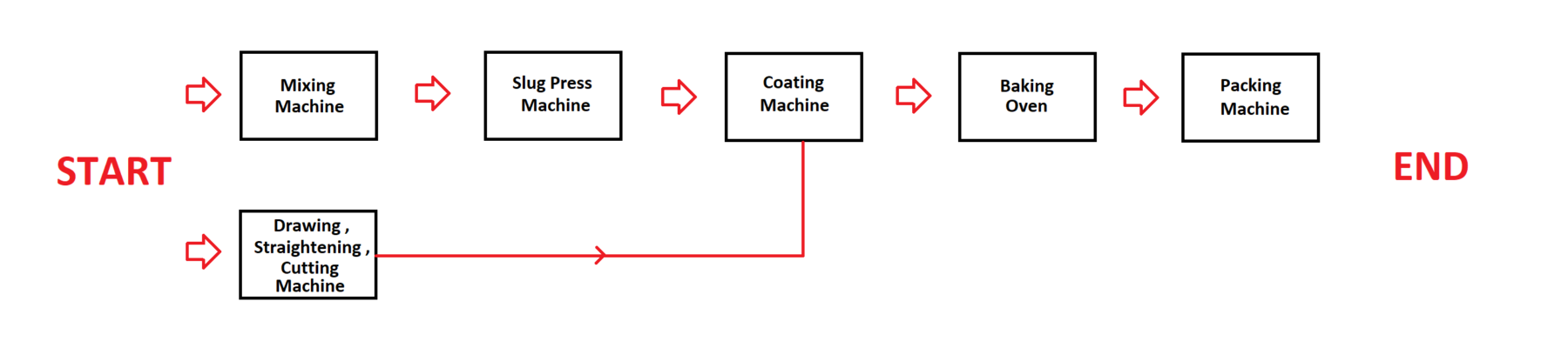
Drawing, Straightening, and Cutting Machine
The task of this part of the production line is to bring the primary wire with a diameter of 6.5 or 5.5 mm to a diameter of 2.5, 3.2, 4, 5, 6 mm. The final output of this line is drawn,straightened and cut wire.
The wire drawing process involves pulling the wire through a series of dies, each with a slightly smaller diameter than the previous one, which reduces the diameter of the wire in successive stages.As the wire passes through each die, it undergoes plastic deformation, reducing its diameter while increasing its length.
Initial Coil and final Output
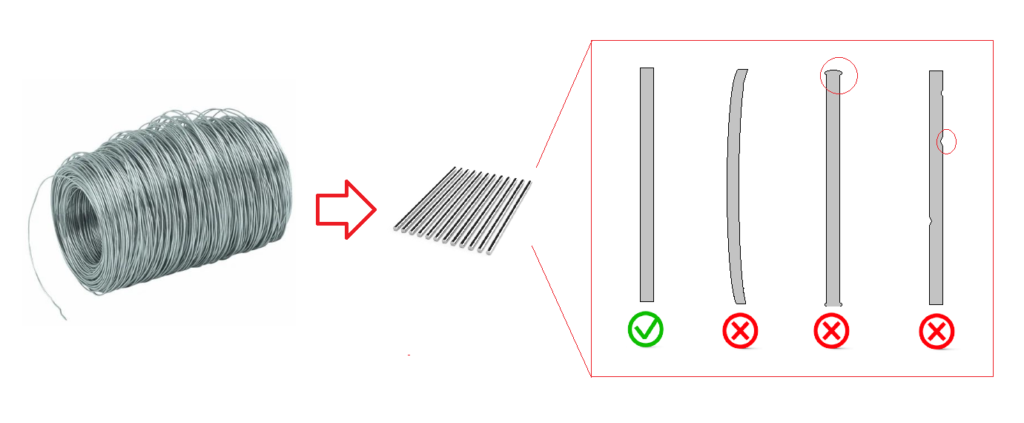
After drawing, the wire needs to be straightened and cut into uniform lengths to serve as the core wire for welding electrodes. The wire straightening machine uses a series of rollers to remove any curvature or coil set from the wire. The straightened wire is then fed into the cutting mechanism, which cuts it into predetermined lengths required for the electrode.
Therefore, we divide this production line into two parts:
Wire Drawing Machine
Straightening and Cutting Machine
The most important parts of this production line are as follows :
Pay-off Stand: Holds the raw wire coil and feeds it continuously into the drawing machine.
Descaling: The descaling unit in a wire drawing machine is a critical component used to remove the oxide layer (scale) and other impurities from the surface of the wire rod before it enters the drawing process. This step is particularly important because these metals tend to form a layer of oxide (scale) during hot rolling or storage.
Drawing Capstans (Blocks):Motor-driven wheels that pull the wire through the dies. These capstans maintain constant tension, ensuring smooth wire flow through the dies.
Drawing Dies: Made of hard materials like tungsten carbide or diamond. Positioned in series, each die incrementally reduces the wire’s diameter.
Lubrication System: Lubricates the wire and dies to reduce friction and prevent overheating. Ensures longer die life and a better surface finish on the wire.
Cleaning Unit: The purposes of a cleaning is to remove residual lubricants, impurities, and metallic particles from the surface of the wire .There are different methods for cleaning wire, the two ways of using a liquid washing tank, with hot water and physical cleaning are the most common and cheapest ways.
Wire Straightening and Cutting Machine: After drawing, the wire needs to be straightened and cut into uniform lengths to serve as the core wire for welding electrodes. The wire straightening machine uses a series of rollers to remove any curvature or coil set from the wire. The straightened wire is then fed into the cutting mechanism, which cuts it into predetermined lengths required for the welding rod.
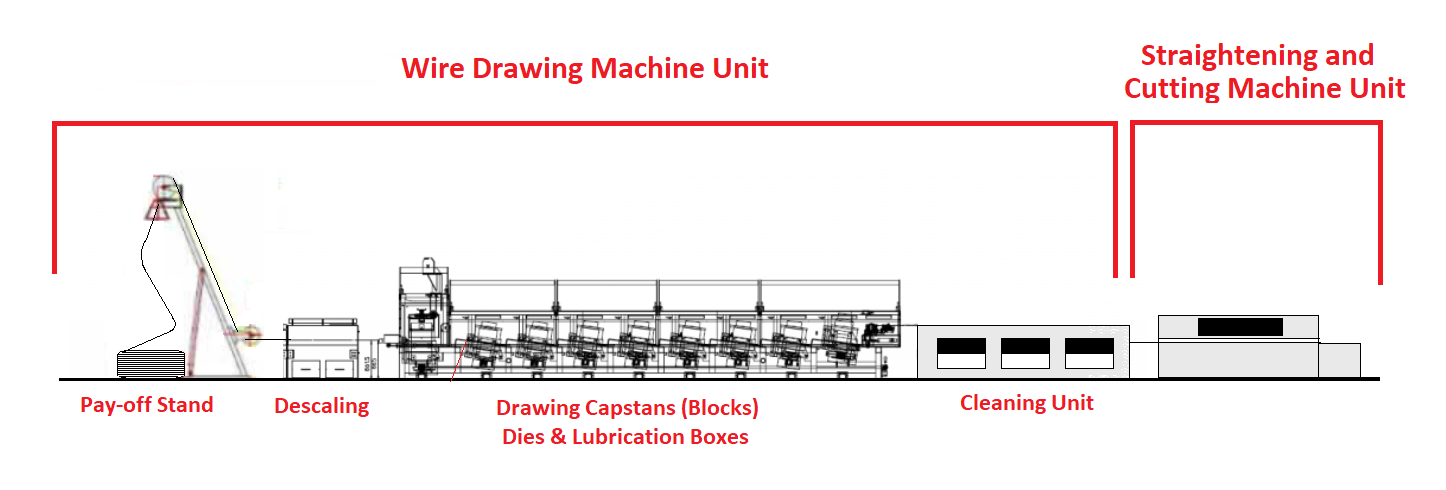
It’s important to note that while there are various types of welding rod production machinery, we can confidently state that the components mentioned are consistently found in all production lines, regardless of the country of manufacture.
Also, in some production methods, the Drawing Line is separated from the straightener and Cutter. But usually these two lines must be connected.
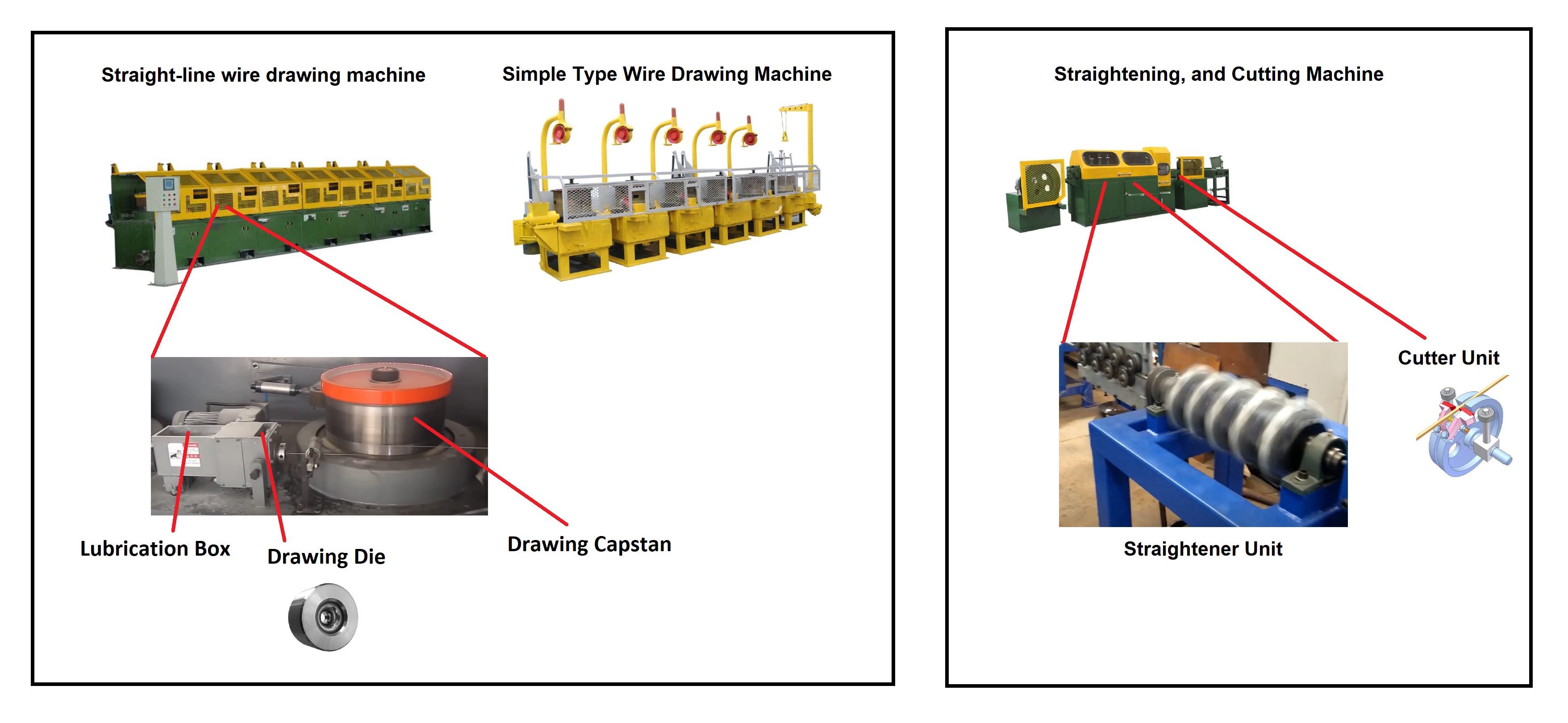
Mixing Machine
In welding rod making machine, the mixer has two tasks, one is the dry mixing of mineral, chemical and metal materials. After that, adding and combining this dry mix with sodium and potassium silicate binders and water to make the Flux paste.
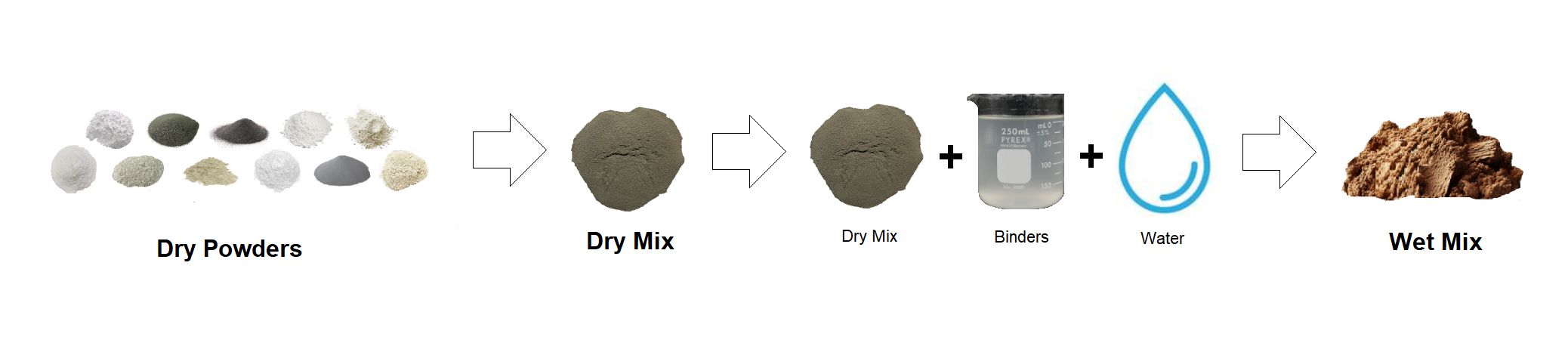
Dry Mixer
The dry mixer has the task of uniformly combining the powder raw materials, since the raw materials for electrode production is in different shapes, it is very important to achieve this uniform composition. According to your budget, the capacity of this mixer will be vary and two different models can be mentioned for this type of mixer.
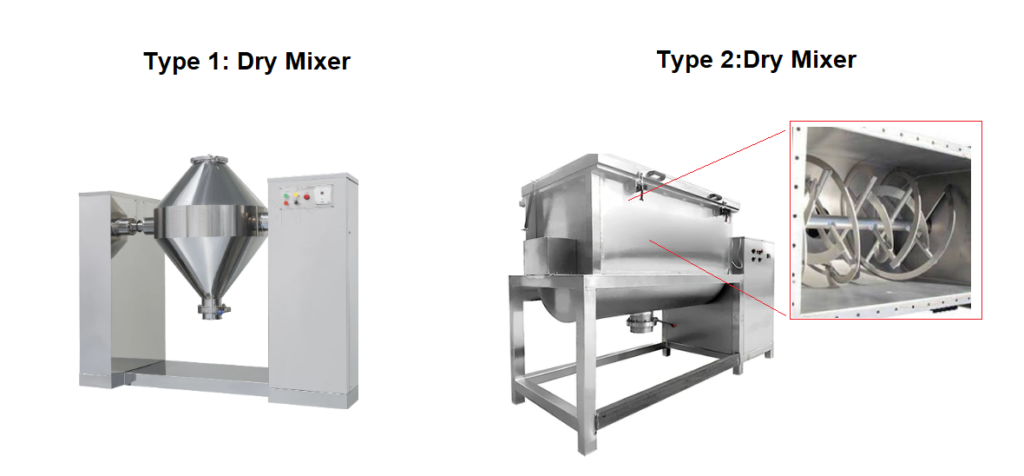
Wet Mixer
The mixer has the function of combining water and sodium and potassium silicate binders with the dry mix to obtain a uniform paste. The most important functions of the Wet Mixer are as follows:
Homogenization: The main objective of the wet mixer is to thoroughly homogenize the mixture. This ensures that all powder particles are evenly distributed in the liquid binder, creating a uniform consistency throughout the batch.
Control of Viscosity: Viscosity is a critical factor in the coating process. The mixture needs to be viscous enough to adhere properly to the core wire, but not so thick that it becomes difficult to apply or too fluid that it runs off.
Shearing and Kneading Action: Wet mixers typically have blades or paddles that rotate at high speeds, exerting both shearing and kneading action on the mixture. This action helps break down any lumps in the powder and ensures thorough wetting of all particles. The shearing force is especially important for blending denser materials like iron powder or certain types of oxides.
Temperature Control: Some wet mixers have temperature control features to prevent the mixture from becoming too hot due to the friction of mixing. Excessive heat can lead to premature drying or changes in the binder properties, affecting the performance of the coating. Controlled temperatures ensure that the binder retains the correct viscosity.
As you can see in the figure below, some mixers have the possibility of dry and wet mixing. The decision to buy a dry mixer depends on various factors, including the desired final product and product formulation.

Slug Press Machine
The briquette press, often referred to as a slug press in the welding rod making machine, is specifically used to compress raw powder materials into compacted briquettes or slugs. These briquettes are then inserted into the coating machine to coat the wire for welding rod production. This step is crucial in ensuring that the coating material is efficiently processed and applied during the electrode production.
It is important to mention that the use of this part of the welding rod making machine is only used for the hydraulic extruder. In the helix or screw extruder machine, the wet flux is directly inserted into the extruder without the need to be compressed.
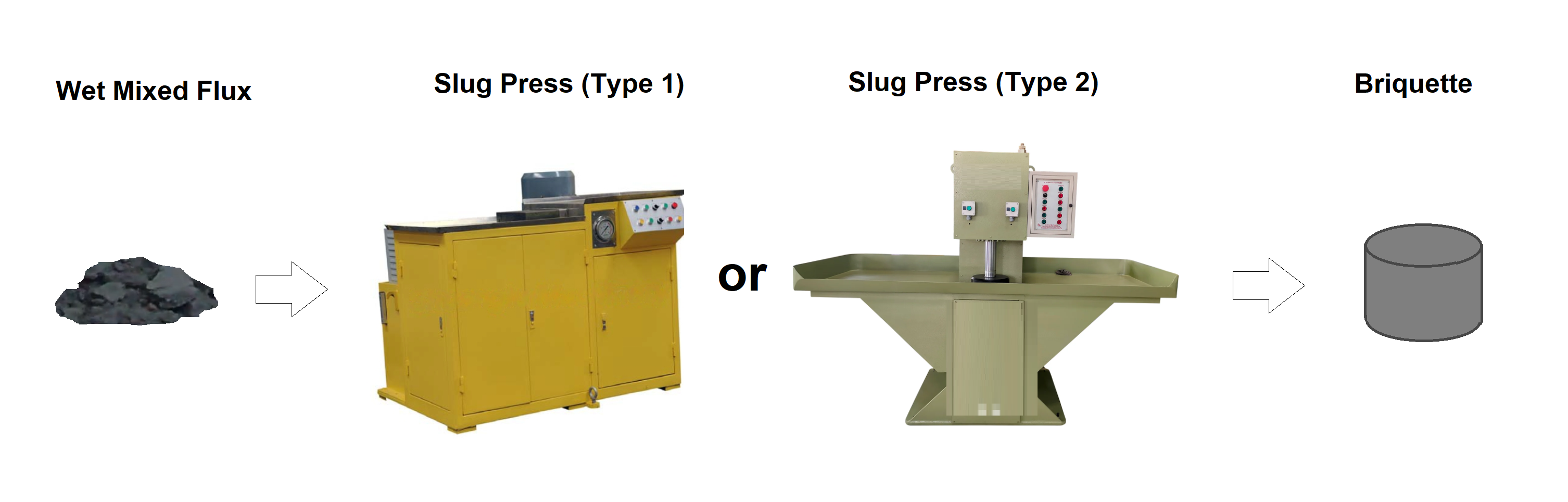
Coating Machine
In welding rod making machine, the coating of core wire can be done by two different type of machine: screw type coating and hydraulic coating.You can also get information about the working mechanism of these machines in E6013 Welding Electrode Production and E7018 Welding Electrode Production.
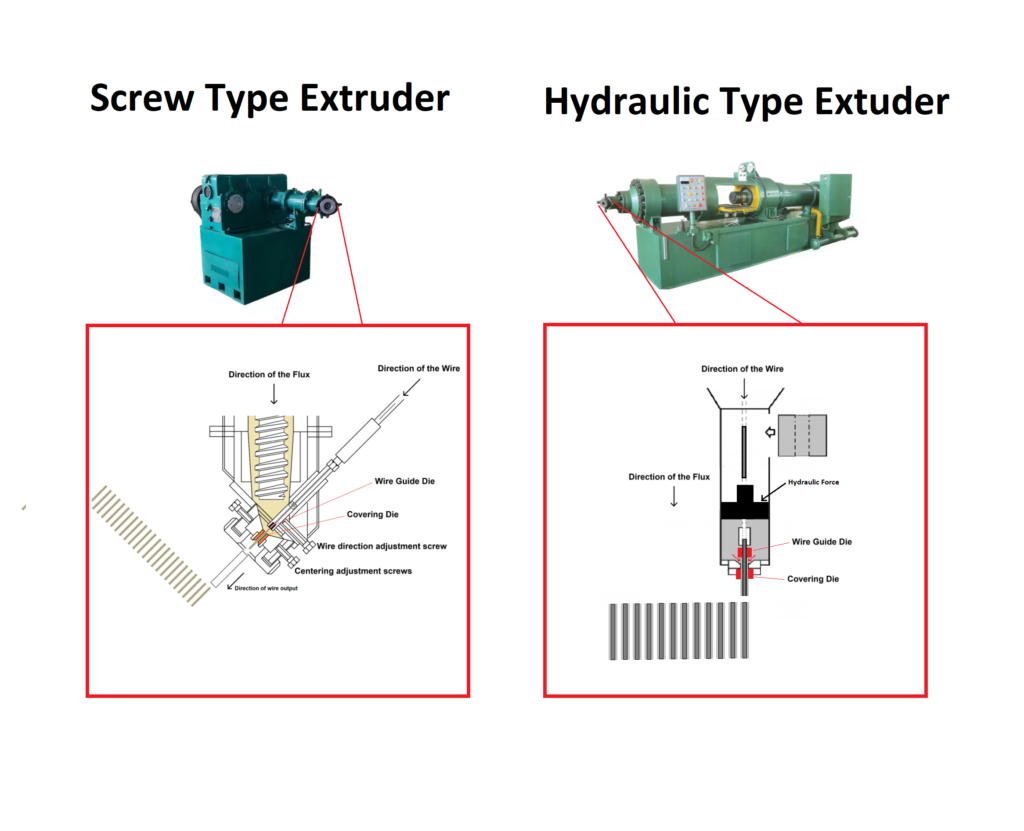
Screw Type Coating Method
In the screw type coating method, The prepared wet flux is fed into a hopper that leads into a screw extruder. The screw inside the extruder rotates and pushes the flux forward under pressure. As the core wire passes through the screw mechanism, the flux is applied to it. The density of the coating can be controlled by the rotation speed of the screw and wire feed speed.After the coating is applied, the electrode passes through a die, which shapes the coating to a desired diameter and ensures uniformity.
Hydraulic Type Coating Method
The hydraulic coating method involves the use of hydraulic pressure to apply the Flux onto the core Wire. In this method, the core wire is inserted into the coating machine, which typically has a cylinder filled with the flux coating paste.Under hydraulic pressure, the flux is forced uniformly around the core wire as it is passed through a covering die. The high pressure ensures that the coating adheres tightly to the surface of the core wire.
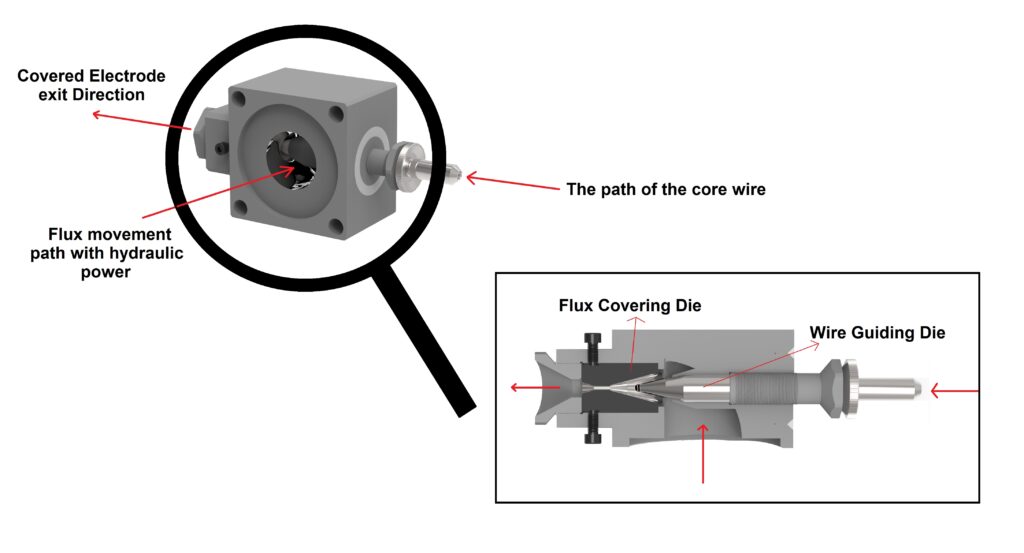
Comparison of Screw and Hydraulic Coating Types in Welding Rod Making Machine
Feature | Screw Type Coating | Hydraulic Coating |
Coating Uniformity | Lower quality than the hydraulic type | High (consistent and precise coating) |
Production Rate | High (continuous extrusion process) | Moderate (slower due to hydraulic press operation) |
Equipment Cost | Lower | Higher |
Surface Finish | May have minor surface defects | Smoother and more uniform |
Precision | Less precise than hydraulic method | High precision with uniform thickness |
Maintenance | Easier to maintain and operate | Requires more specialized skills and higher maintenance |
Application | Ideal for mass production of standard electrodes | Suitable for high-quality or precision electrodes |
Baking Oven
Different Types of Baking Oven in Welding Rod Making Machine Line
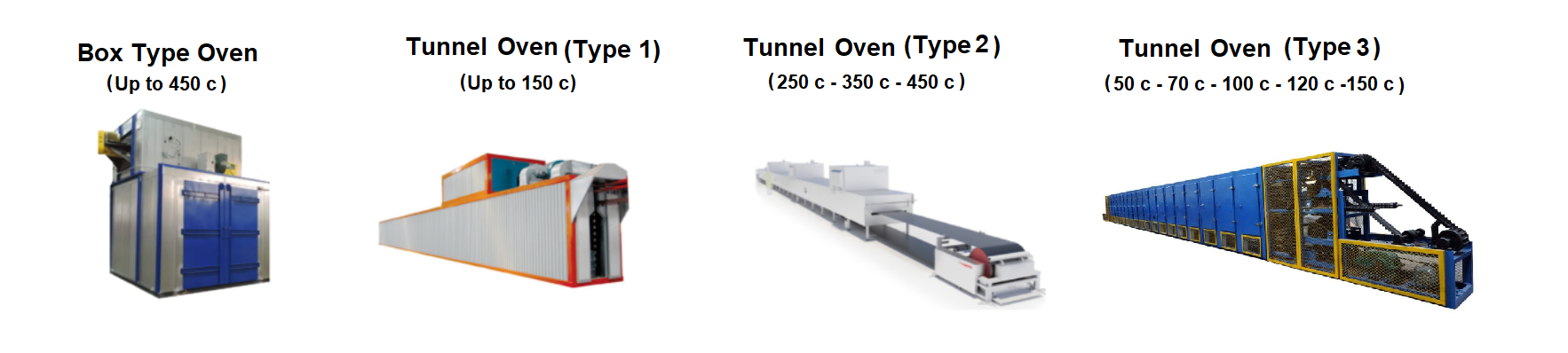
The Box Type Baking Oven in Welding Rod Making Machine
A box-type electric oven is a chamber designed to heat welding rods in a contained space. In this type of oven, the welding electrodes are placed on a trolley and moved into the chamber. Once the door is closed, the heat generated by the elements is applied to the electrodes through airflow. This type of oven can adjust the temperature using a time-temperature graph. The technology of these furnaces lies in the heat flow and heat generation system of the elements. There is also a gas version of these ovens, where the heat is produced by flames from burning gas.
Box Type Baking Oven Working Mechanism
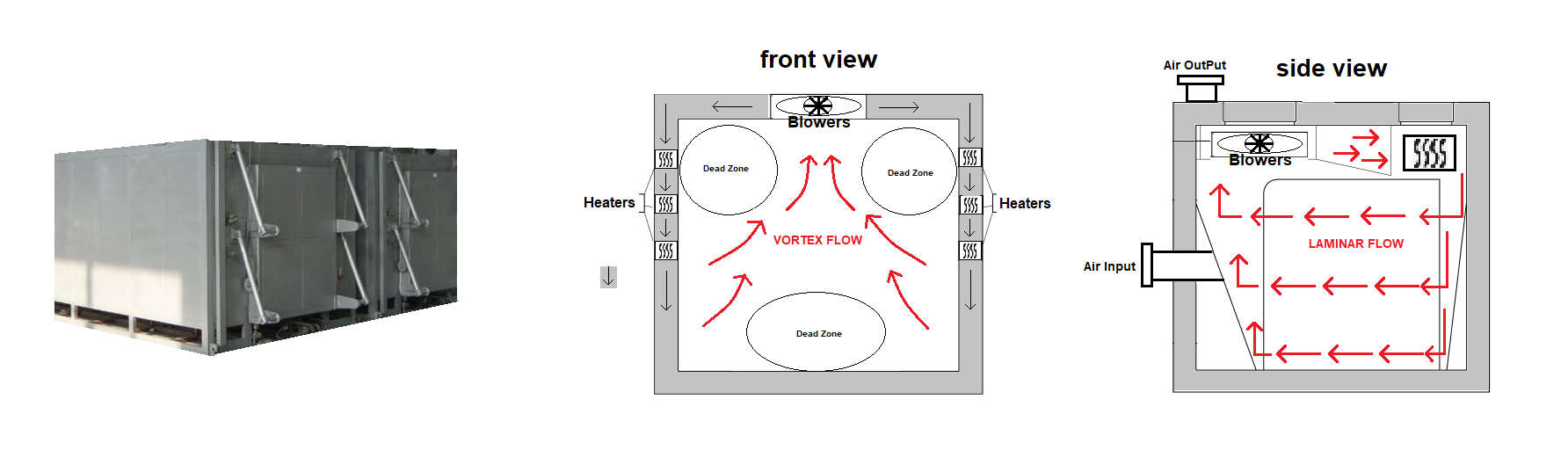
The Tunnel Type Baking Oven in Welding Rod Making Machine
A tunnel oven used in the manufacturing of welding rods (welding electrodes) is a continuous, high-capacity baking system designed to efficiently heat-treat large volumes of electrodes. This type of oven consists of a long, enclosed tunnel where the welding rods move through on a conveyor system, typically mounted on trays or trolleys. The heating process is highly controlled, with adjustable temperature zones that allow for precise regulation of the baking cycle to ensure optimal curing and moisture removal from the electrode coating.
Comparison of Box and Tunnel Type Baking Oven in Welding Rod Making Machine
Feature | Box Type Oven | Tunnel Type Oven |
Production Capacity | Limited, batch production | High, continuous production ideal for large-scale |
Heating Process | Batch mode, uniform heating | Continuous, multi-zone heating for precise control |
Efficiency and Time | Downtime between batches, slower for high-volume | Continuous operation, minimal downtime, higher efficiency |
Air Circulation | Variable, possible temperature variation(Vortex & Laminar Heat Flow) | Controlled, consistent airflow with forced convection |
Energy Consumption | Higher due to batch operation | More energy-efficient for large-scale production |
Space and Setup | Requires less space, simpler setup | Requires more space, complex setup |
Cost and Labor Requirement | Lower initial cost, less efficient for large-scale.
More manual handling, labor-intensive |
Higher upfront cost, more cost-effective for mass production. The furnace used to produce E6013 is cheaper than the box type
Lower, due to automation and continuous operation |
Packing Machine
Depending on the type of welding rod (welding electrode), the packaging of this product will be different. Normal electrodes such as E6013 are packed in carton packaging. Nylon shearing is also applied to the carton as a protection. This work is done by a shrinking machine. This method can also be used in the packaging of other types of electrodes such as E7018.
Another type of packaging is using a metal can. This method is usually used to pack cellulosic electrodes. The purpose of this type of packaging is to prevent the moisture present in the coating of the cellulose electrode from escaping because a certain amount of moisture plays a useful role in the welding quality of this electrode.
Seal vacuum packing protects welding rods from moisture, oxidation, and contaminants. It ensures quality, especially for moisture-sensitive electrodes Like Alkaline Electrodes, and eliminates the need for Re-drying after open the packing. Vacuum-packed electrodes are convenient for long-term storage and transport in critical applications.
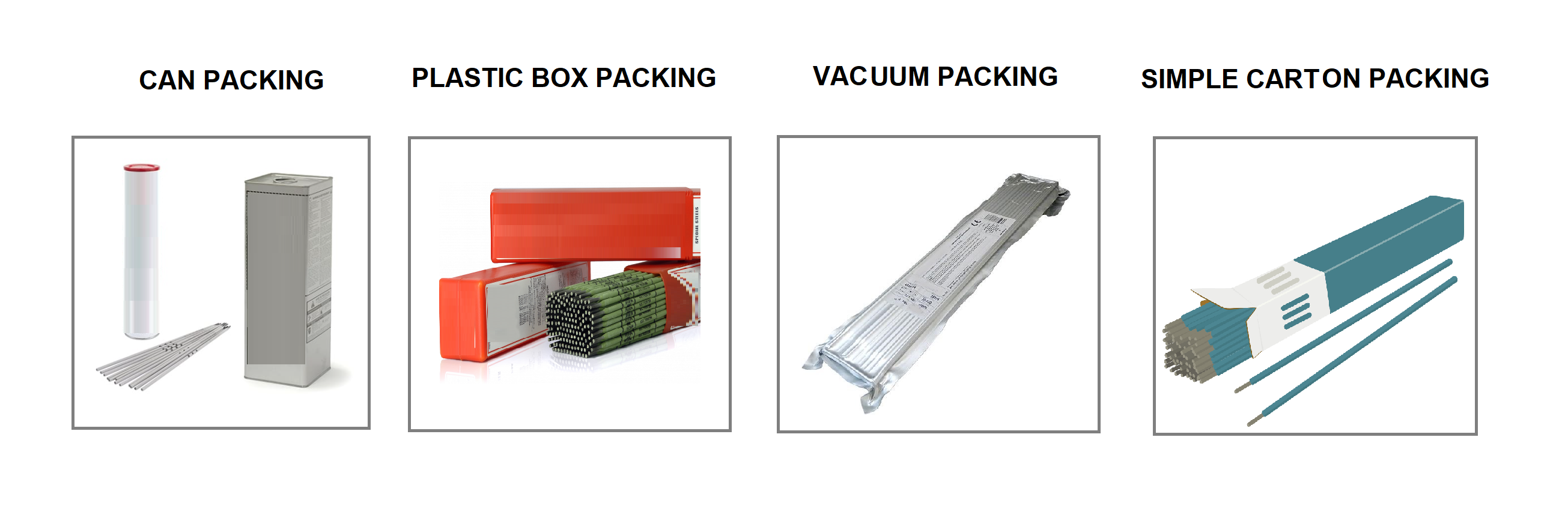
Other Units and Their Application in Welding Rod Making Machine
Other parts of the Welding Rod Production Line that are necessary are as follows :
Reclaiming Machine: Welding Rods(Welding Electrodes) that are not of suitable quality and the flux must be removed from the surface of the wire are entered into this machine.The wire is reused and the flux is recycled through Pulverizer and Shaking Sieve.
Pulverizer: The flux separated from the surface of the wire is crushed in this machine.
Shaking Sieve: The crushed flux in this machine is separated by passing through the vibrating sieve to be used again in the coating.
Wire Straightener: Recycled core wire that are bent are straightened in this machine for reuse.
Electrode Printing Machine: This device is used for printing the name of the electrode on the surface of the welding rod.
Eccentric Measuring Instrument: The core wire must be exactly in the center of the cover and this is controlled by this device.
Binder Tank: This Tank is responsible for keeping the Binder before use.
Wire Feeder & Coating Press(Lab Model): When changing the supplier of one of the materials or changing the formulation before production in the main line, this device is used for testing and research.
Wire Guide: Part of Wire Drawing Unit.
Belt Packing Machine: Part of Packing Unit.
Rod Shooter: This part has the task of dropping the electrode onto the conveyor after it comes out of the hydraulic nozzle.
This photo showcases the full range of machinery used in the production of Welding Rods (coated welding electrodes) From wire preparation to coating and drying, each machine plays a vital role in ensuring high-quality production.
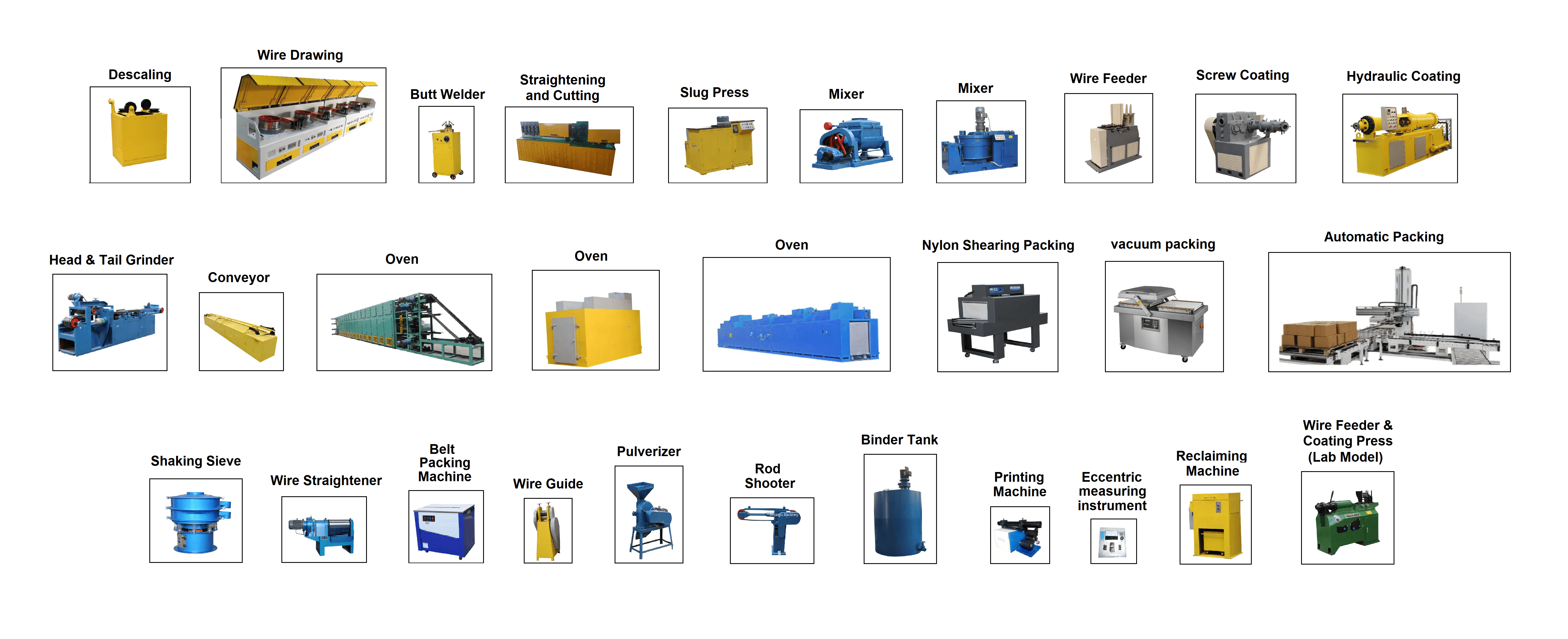
Dear Sir/Madam
We would like to invest covered electrod producing in Turkmenistan. We are quite big company in here. We have Sere Construction Sere Concreate Esli textile DegrePlast and MetalON Screw Co.
We are familiar of wire and wire drawing and wire production. We want to invest Electrod production here also.
Please inform us how we can be partner and achieve that project together.
I am waiting you replay.
Best Regads
Huseyin Gumustekin