Lubricants for Wire Drawings
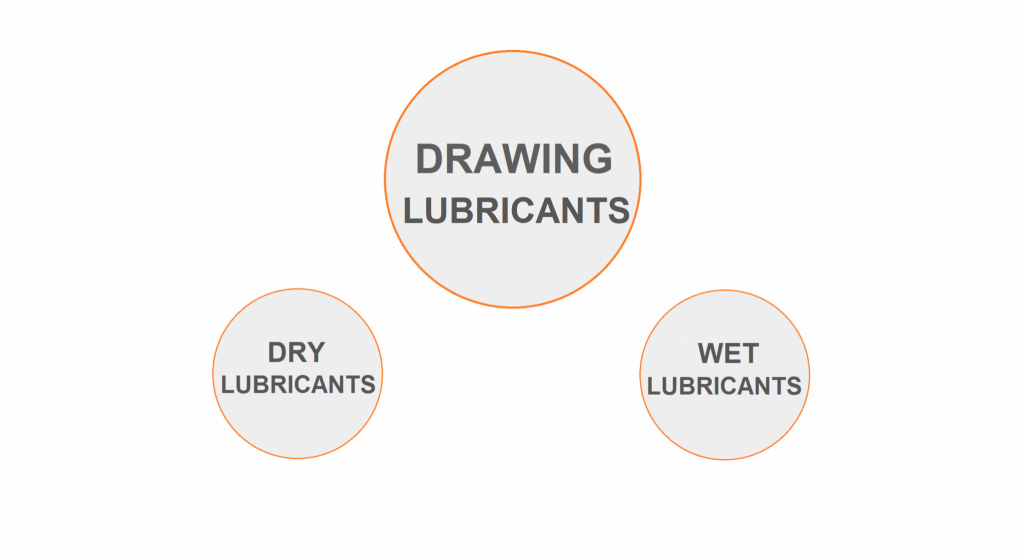
Lubrication in Wire Drawing
The role of lubricants in wiredrawing cannot be underestimated because it is key for the production of high quality wire products. Therefore, work on the fundamental aspects of lubrication must be continued in order to enhance performance. The future will see the development of new lubricants based on polymeric materials and enhanced modes of lubricant application such as pressurized application systems. In addition, fundamental modifications to the wiredrawing process will present a need for new, radical lubricants to keep up with these advancements.
The wire drawing process generates significant heat. This heat affects the lubricants ability to ensure quality wire production. The amount of generated heat is influenced by an interaction of factors that include the metal composition, surface preparation, and production equipment.
Factors Affecting Wire Drawing Dry Lubricant Selection
.Composition of the metal to be drawn
.Surface condition of rod and wire
.Drawing speed
.Drafting practices
.Die design
.Machine design and constraints
.Downstream use of wire
Importance of Lubrication in Wiredrawing:
The process of drawing ferrous wire through a reducing die results in the generation of high temperature, pressure and shear forces within the die, and, ultimately, massive, permanent deformation of the wire. Since the function of any lubrication is to reduce the friction and wear between two objects in relative motion to one another, the lubricant used in ferrous wiredrawing plays a critical role in reducing the friction between the die and wire, as well as the wear of the die. This has several important effects including:
- Reduced machine downtime to replace worn dies
- Reduced drawing forces because there is reduced friction
- Reduced surface temperatures for the wire and die
- More uniform physical properties of the wire due to more uniform metal deformation
- Reduction in off-specification wire
For these reasons, the role of lubricants in the wiredrawing process is critical and has become one of the most important variables in the move toward higher performance operations.
Types of Lubricants
Both solid and liquid lubricants are used for wire drawing. Drawing with solid lubricants is called dry drawing and that with liquid lubricants is called wet drawing.
Dry Drawing:
In dry drawing, the lubricant is in the form of solid powder which is generally a mixture of soap powder, graphite and lime or a mixture of solid fat and lime (CaO) and Ca(OH)2. The soaps generally used are calcium stearate and stearates of other metals like sodium, zinc and aluminium.
Sodium soap is particularly useful after the phosphate coating process which is described below. The typical compositions contain 10-15% aluminium stearate, 15-20% calcium stearate, hydrated lime 60-70% and graphite 2 to 5%.
Dry drawing is generally used for heavy reductions, though the surface produced is dull. The drawn wire also carries a thin film of lubricant which helps the subsequent processing such as upset forging of headed components like rivets, screws, bolts, etc.
In order that the wire surface may be able to carry the lubricant into die, it is coated with lime, for which, the wire is dipped in hot solution of lime at about 70°C, then taken out and dried. It may require several dippings before the desired film thickness is achieved. It is finally dried and baked at 200°C. The lime particles get firmly attached to the wire surface and can entrap the lubricant particles when the wire passes through the lubricant box which is placed just before the die.
During the drawing operation the wire becomes hot and the soap tends to melt. The lime helps in keeping the lubricant thick and viscous and in maintaining lubricant film on the interface so that metal to metal contact between die and wire does not take place. However, for small diameter wires (d < 0.5 mm) lime is not used.
Wet Drawing:
Wet drawing is used for obtaining bright surface finish and for using hydrodynamic lubrication devices. Also it is used for small diameter wires and for wires which have to be coated after the drawing process because wet lubricant is easier to remove.
In wet drawing, liquid lubricants are mixtures of soap solutions with up to 3% oil. Soap emulsions with water and fatty oils may be used for copper, silver, gold and platinum wires. For aluminium wires petro-oils with fatty oils may be used.
Phosphate Coating:
It is beneficial to use phosphate coating for drawing wires of high strength steels. Phosphate coating is very adherent and spongy and can absorb the lubricant and hence acts as a very good lubricant carrier. The coating prevents metal to metal contact even under extreme pressures.
For phosphate coating, the wire surface is thoroughly cleaned of rust and grease. It is rinsed before dipping in a bath containing phosphoric acid and zinc phosphate.
The following reactions may take place:
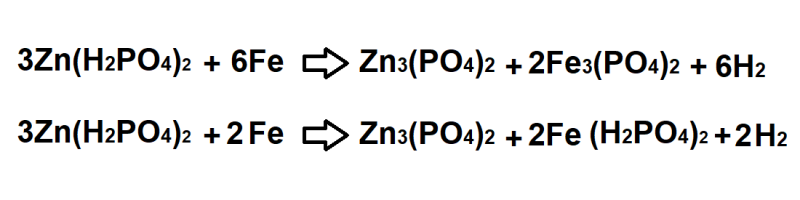
As the process proceeds the chemical reaction gradually slows down due to the following two reasons:
(i) Hydrogen which evolves during the reaction, makes a gaseous shield between metal and the solution. An oxidizing agent is added to the solution to convert hydrogen into water. Sodium nitrate or sodium chlorate may be used. The addition of these chemicals accelerates the process.
(ii) The second problem arises due to the dissolving of iron in the solution. This changes the composition of solution from Zn phosphate to iron-zinc phosphate resulting in slowing down the process. The addition of sodium chlorate helps in converting ferrous phosphate to ferric phosphate which precipitates out of the solution, thus it helps in maintaining the original composition of the solution.
After phosphate coating, the wire is dipped in a liquid lubricant generally containing soap and MoS2. The spongy and adherent phosphate coating absorbs the lubricant. If the coated wire is dipped in a solution of sodium stearate, a chemical reaction takes place as a result of which zinc-stearate is formed at the top layer of coating.
This makes a highly adherent lubricant film because zinc stearate is chemically bonded to zinc phosphate which in turn is chemically bonded to wire metal. Experience with this coating shows that wire may be drawn through 10 to 12 dies without an additional lubricant box.
Hydrodynamic Lubrication in Wire Drawing:
Now-a-days, wires are drawn at pretty high speeds, and therefore, hydrodynamic effect may be utilized to enhance the lubrication at the die-wire interface. Hydrodynamic lubrication decreases the die wear as well as the drawing force. In conventional wire drawing the motion of lubricant is illustrated in FIG Y12.
FIGY12
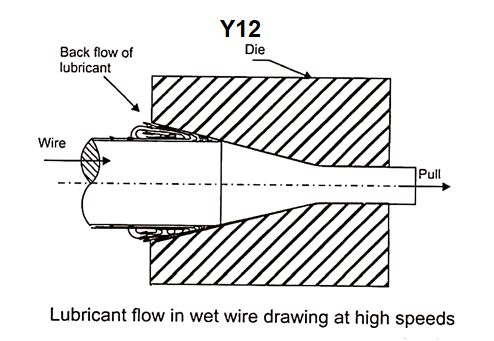
As the wire passes through the liquid lubricant box, its surface picks up a layer of lubricant, which moves along with the wire. Because of high interface pressure between the wire and the die, only a small fraction of the lubricant layer can go through the die, the remaining lubricant coming at high speed with the wire comes to a stop and possibly flows back (FigY12).
The change of momentum of high speed fluid (Newton’s second law of motion) gives rise to very high pressures near entrance to the die. This is equivalent to a pressurized lubrication. The hydrodynamic lubrication may be enhanced by fixing a short tube length at the entrance to the die (FigZ12). The clearance between the tube and the wire is very small, just sufficient for the fluid film to get into the tube along with the wire.
A second device shown in (FigX12) employs two dies fixed at either end of a high pressure chamber. A low reduction is given in the first die while a high reduction is given in the second die. The low reduction allows more fluid lubricant to get into the chamber while the high reduction in the second die allows less quantity of fluid to get out of the chamber. Thus, a high pressure is built up inside the chamber. The second die gets high pressure lubrication.
FIG Z12&X12
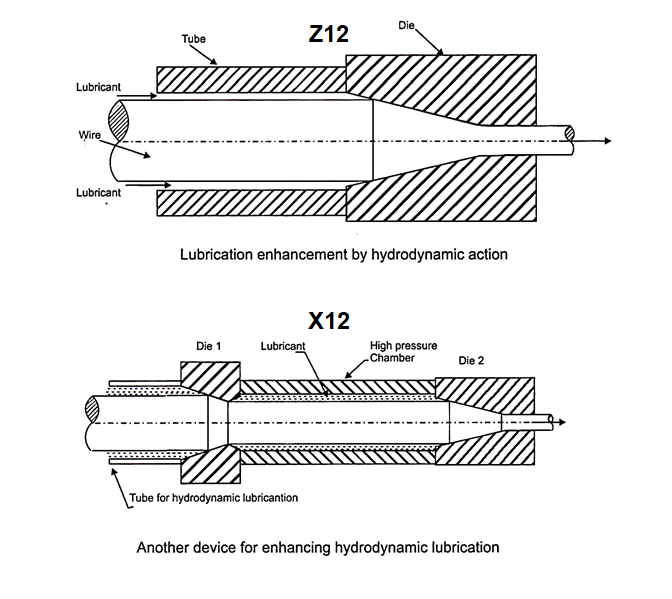
Lubricant Selection on Wiredrawing Operations
The primary functions of a lubricant are to reduce friction and to minimize wear. However, there are other criteria that need to be considered when selecting a lubricant. Since lubricity must be maintained throughout the drawing operation, residual lubricant is a left on drawn wire see (Figure A12). This residual lubricant often is beneficial for subsequent deformation processes, such as cold heading coiling operations, and it can improve surface appearance and corrosion resistance during storage. On the other hand, residual lubricant on the wire may impair cleaning and annealing of drawn wire. Finally, environmental concerns such as hazardous materials, harmful emissions, and ease of disposal, must be considered in lubricant selection.
FIG A12
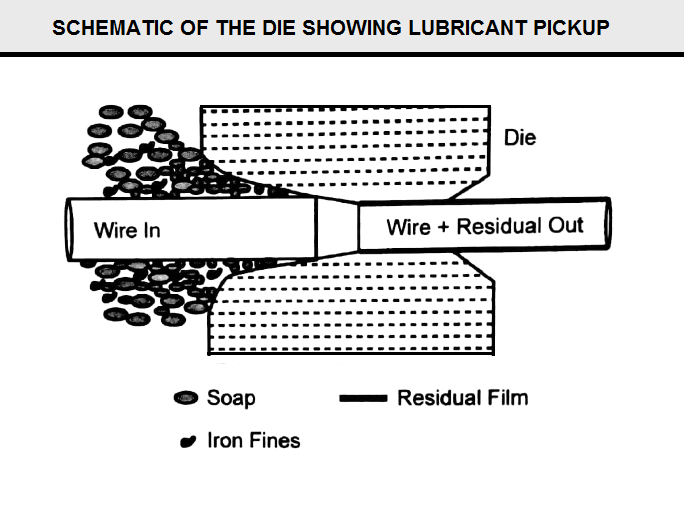
Mechanisms of Lubrication in Wiredrawing
Hydrodynamic and Boundary Layer Lubrication
Lubricant film thickness determines the mechanism of lubrication. For thick lubricant films, hydrodynamic lubrication occurs, and boundary layer lubrication results for thin lubricant films. For mixed lubricant thickness, the lubrication mechanism is a combination of hydrodynamic and boundary layer termed quasi-hydrodynamic (see Fig B12).
In hydrodynamic lubrication, a lubricant film physically separates the two load bearing surfaces that would otherwise contact one another (the wire and die surfaces). If this layer is thick enough, the relative motion of wire through the die is opposed by shear strength and viscosity of the lubricating film. Clearly then, the coefficient of friction for hydrodynamic lubrication is a function of the shear strength and viscosity of the lubricant. Friction in hydrodynamic lubrication is low and wear is minimal.
Due to high loads, the lubricating film layer becomes increasingly thin, and a microscopic layer of lubricant separates the two working surfaces. In this case, physical properties of the bulk lubricant, such as shear strength and viscosity, are not important. Rather it is the chemistry of the lubricant and nature of the base metal that are important. Typically, the lubricant is either adsorbed or it reacts chemically with the metal surface to form the boundary lubrication. Asperities on the opposing surfaces pierce through the lubricant film so that the coefficient of friction is a function of the wear properties of the metal.
Film thickness and coefficient of friction for boundary layer, quasi-hydrodynamic, and hydrodynamic modes of lubrication as a function of lubricant viscosity (Z), speed of the surfaces relative to another (N), and die pressure (P) is given by Stribeck curves. See (Figure C12) At high speeds and low pressures (ZN/P increases) hydrodynamic lubrication dominates. However, as the ZN/P ratio decreases, and there is incomplete separation of an surfaces and wear. Then, the coefficient of friction increases, until the point at which the boundary layer lubrication becomes dominant. At this point, the friction is high, and there is no relationship between the physical properties of the bulk lubricant and the friction.
FIG B12
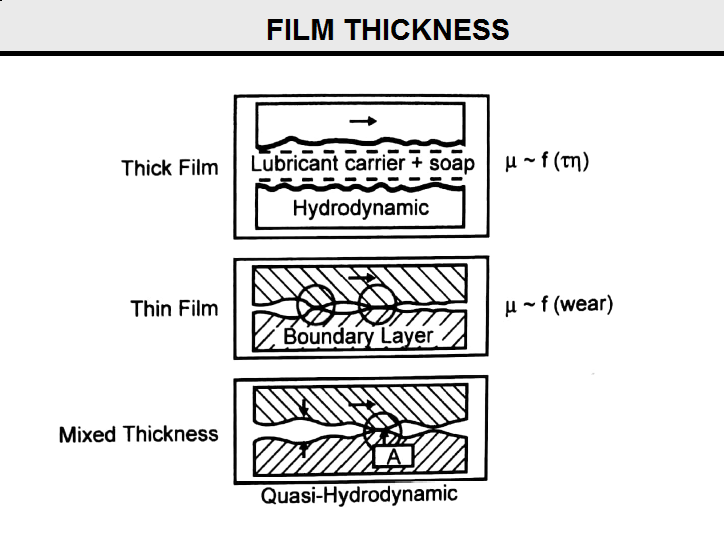
FIG C12
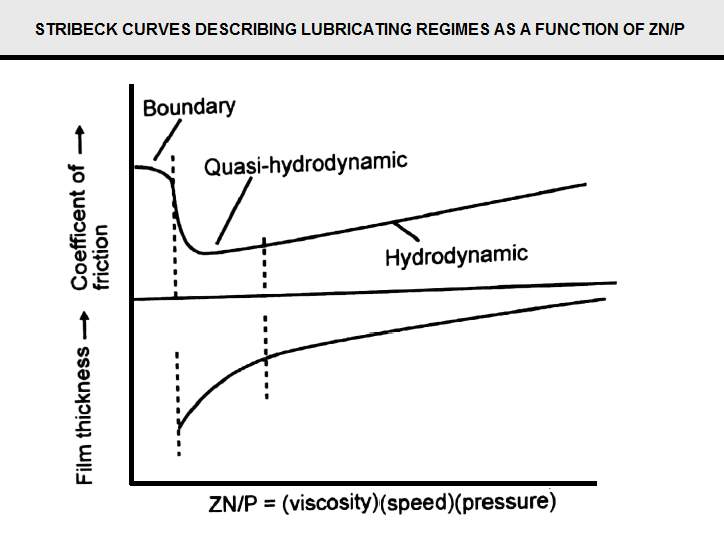
Lubrication Modes in Wiredrawing with Soap Powders
Hydrodynamic lubrication is preferred in wiredrawing, and the die design to supply lubricant in a wedge-like configuration strongly promotes the hydrodynamic mode, as illustrated in Fig. 1. Hydrodynamic lubrication provides the lowest friction in the drawing process. However, in the wiredrawing process, there is a wide range of pressure, temperature, and speed from rod breakdown to final fine wiredrawing that affects lubrication according to the Stribeck curves. Therefore, wiredrawing lubrication is best describe as a combination of both hydrodynamic and boundary layer modes (quasi-hydrodynamic) in practice. For example, for rod breakdown at high pressures and low speeds, there will be a reversion to boundary layer lubrication. Conversely, in situations where there is high drawing speed, high viscosity, or decreased die pressure, hydrodynamic lubrication can occur.
It should be noted that this is a general description of the lubrication modes, and there remains more fundamental work to be done to understand the mechanisms better. Nonetheless, the bottom line is that in the development and selection of lubricants for wiredrawing, both chemistry and bulk characteristics, must be considered to best match a drawing soap to a given application.
Types and Chemistry of Wiredrawing Lubricants
Dry Lubricants (Soap Powders)
Dry lubricants comprise the majority of ferrous wiredrawing compounds used to achieve the requisite reduction of area in the drawing process. All wiredrawing soaps are the reacted product of fatty acids and an alkali to form a salt, with additives and other materials incorporated into the soap to enhance performance. Wiredrawing soaps typically are categorized according to their solubility in water as follows:
- Insoluble soaps-usually calcium-based, such as calcium stearate formed by the reaction of lime and a stearic acid.
- Partially soluble soaps-usually mixtures of sodium stearates and calcium stearate formed by reacting a caustic soda (or sodium carbonate) and lime with a stearic acid.
- Soluble soaps-sodium or potassium stearates formed by the reaction of caustic soda (or sodium carbonate) and caustic potash with a stearic acid.
The type of fatty acid used to manufacture a drawing soap affects its properties. These fatty acids are typically classified by “titer,” which is a measurement related to the melting point. Typically, the softening point of soap increases with increased titer of the fatty acid, as shown in (Figure D12). It should be noted that the identification of the softening point often is difficult; hence the rule is a general one.
Typically, soluble sodium soaps, or insoluble calcium soaps, contain additives incorporated during the reaction of alkali and fatty acid. These additives may be high melting point materials used to increase the softening point and melt viscosity of the lubricant, extreme pressure (EP) additives, adhesion enhancers, corrosion inhibitors, etc. Types and effects of additives are discussed below.
Lime-(calcium hydroxide) is by far the most common additive due to its effectiveness and cost. While lime is used primarily in calcium-based soaps, it is also effective in sodium soaps. Typically, the ratio of lime to calcium soap is described as “richness of soap.” The leaner the soap, the less fat (or soap) it contains and the higher its softening temperature become. Lime acts primarily as a thickening agent, which increases the melt viscosity of the soap, as illustrated in (Figure E12). The relationship between richness of soap and lubrication properties will be addressed in the Lubricant Selection Section.
Borax-is another popular additive for wiredrawing soaps, which, like lime, has been used as a rod coating for many years. It is used principally in sodium soaps to increase the softening point, melt viscosity, and compressive strength. Also, it is used as an additive in soaps designed to leave a residue after drawing that will not interfere with subsequent welding operations. Borax has the disadvantage of being hydroscopic; hence, it tends to pick up moisture in humid environments resulting in clumping. Environmental restrictions on boron levels in waste effluent need to be considered.
Sodium Carbonate-or soda ash, is fused into sodium soaps to enhance melt viscosity. The presence of sodium carbonate also enhances the water solubility of the lubricant residue, and it is popular in applications requiring cleanability in water.
Sodium sulfate provides a similar enhancement of melt viscosity as doe’s soda ash, but it does not contribute to the alkalinity of the lubricant. This material also promotes lubricant pickup and results in thick lubricant films, probably in a manner similar to that provided by the use of now largely obsolete iron or ferrous sulfate.
Before the advent of carbide dies, one of the important coatings to assist wiredrawing was a “sull” coating. This is actually light brown rust obtained by spraying water on acid-pickled rod. Iron (ferrous) sulfate, which is an acidic salt, leaves a residue that is reddish brown, somewhat similar to a sull coat. Lubricants containing ferrous sulfate were preferred by many nail manufacturers since they left a thick residual film, which enabled good nail cutting.
Colored Pigments-include materials such as zinc oxide, titanium dioxide, and calcium carbonate. These materials tend to be dual-purpose additives. They modify the surface appearance of wire and function in a manner analogous to pigmented liquids used for deep forming operations on sheet metal. The pigment particles tend to “fill in” areas of surface roughness so that a smoothing effect is obtained. This is particularly applicable to mechanical descaling where there is no rod coating to fill in surface roughness. Due to its hardness, titanium dioxide can have a positive effect on maintaining a smooth die surface by its ability to polish the die. Further, it tends to have an affinity for the surface of the steel wire, which can provide separation between the wire and die surfaces.
Friction Modifiers-graphite, mica, talc, molybdenum disulfide tungsten disulfide, graphite-fluoride, and Teflon powders belong to a class of additives best referred to as friction modifiers. These are plate-like materials so that particles readily slip over each other. With varying degrees of effectiveness and expense, these materials can significantly reduce friction at the die/wire interface. Molybdenum disulfide is particularly popular because of its low coefficient of friction; however, it is expensive.
Sulfur and Extreme Pressure (EP) Additives-such as elemental sulfur, alkali sulfides, and polysulfides, are reactive in nature. They function by reacting with the wire surface to form a compound (iron sulfide) having reduced shear strength relative to the metal and the die material. These additives should be used with discretion where fluxing in a post-drawing welding operation, or subsequent corrosion might be a problem. One important feature of such materials is that they tend to increase the melt viscosity with increased temperature, thereby allowing heavy deformation during drawing.
Corrosion Inhibitors-usually based on alkali metal nitrites are routinely compounded into wiredrawing lubricants, particularly those that are water soluble and hygroscopic. It is important to remember that they have limited temperature stability and, as such, offer no protection following any annealing or heat treatment cycles.
Pastes and Greases-pastes are soap/water mixtures with various additives, and greases are soap-thickened oils, also with additives. The additives are the same ones used in drawing powders. Pastes and greases are used principally for drawing plating quality wire where clean, bright surface is required. However, to maintain reasonable die life, some residual film must be left on the drawn wire. There is a thin line between scratching out and a lubricant residue that is too heavy.
FIG D12
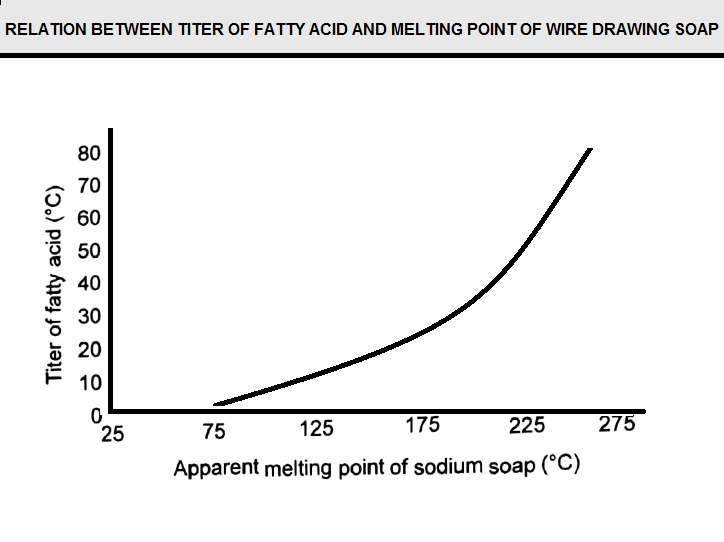
FIG E12
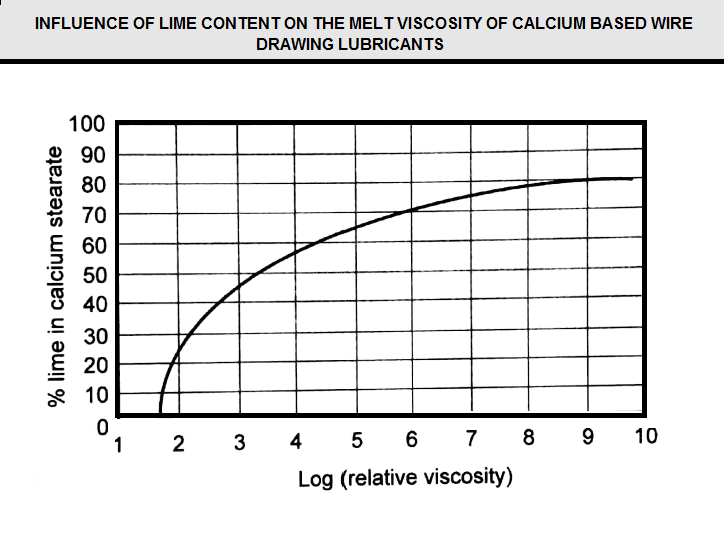
Wet Lubricants
In drawing fine wire to its final dimensions, wet drawing is often used, particularly in applications requiring special finishes, and for ferrous wire with coatings such as copper, zinc, and alloys. In many cases wet drawing follows a dry drawing stage in which a certain residual soap remains on the wire to reduce metal-to-metal contact in the wet drawing stage.
Emulsions or solutions are used mainly for copper wire, but they are also common for drawing copper and brass coated and liquor finished wire where forces between die and wire are not as great as typical ferrous operations. These lubricants may be soap-fat mixtures in water where the soap acts as an emulsifier, wetting agent, detergent, and lubricant. The fat, emulsified by the soap, provides the principal lubrication. A system such as this requires chelators to prevent the soap from reacting with metal ions present in hard water. They also require pH control to stabilize the emulsion in order to maintain the detergency and lubricity of the soap.
When drawing copper coated wire, a build-up of copper salts in the drawing solution will eventually deplete chelating materials and react with the soluble soaps rendering the fatty acid molecule ineffective. Most modern formulations are synthetic based. Other ingredients include mineral oils to lubricate and, to some extent, to reduce foaming; other defoamers, chelators, inhibitors to prevent metal corrosion, lubricant oxidation and bacterial attack, and coupling agents to solubilize incompatible ingredients. Advantages of the more synthetic-based materials include:
- No reactivity with hard water salts or copper
- Effective lubricity and detergency over a wider pH range Easier to handle since they are liquids instead of paste concentrates
- Essentially 100% active and therefore you aren’t paying to transport water
- Low ash for clean annealing
- Solution life is usually extended because they are less sensitive to pH or salt concentration (hard water or copper)
Lubricant Selection
Matching Lubricant Type to Application
The following three requirements must be met to draw wire effectively(see FIG F12):
- The lubricant must become plastic to flow through the die.
- Lubricant pickup on the wire must be adequate.
- Die geometry must be appropriate for the drawing practice.
It should be noted that drawing die geometry causes problems for both wire manufacturers and lubricant suppliers, since it is not possible to make up for poor die geometry and drafting practice with the lubricant.
In order to understand the lubricating properties of rich and lean soaps, consider drawing a high carbon spring wire and a low carbon wire having the same initial and final diameters. High carbon wire has a higher tensile strength, and it requires greater die force resulting in higher die pressure and temperature than needed for low carbon wire. A lean soap, with its higher softening temperature and higher melt viscosity, would provide a good lubricant with a light residue after drawing; whereas, a rich soap softens excessively and would be literally squeezed out of the die-wire interface. When this occurs, the lubricant balls in the die box and scratching or breaking results. For low carbon wire, a lower die temperature allows a rich lubricant to perform well with a reasonable residual film. However, a lean lubricant, although lubricating well, results in a very heavy residue that is wasteful, expensive, probably dusty, and very likely unsuitable for any end use application.
Ratios of lime to calcium soap usually vary from 25:75 to 75:25. Below 25% lime, the lubricant tends to soften at too low a temperature for even the least demanding draw, as shown in Fig Above 75% lime, lubricity suffers because residual films are incomplete or lack cohesiveness.
Lubricant choice is influenced by many operating variables. Some of these factors include:
- Drafting practice-greater reduction causes more die force.
- Drawing speed-higher speeds cause greater die force and increased temperatures.
- Machine and die design-affect lubricant pickup, and interpass cooling can affect die temperature.
- Rod surface-heavy surface coatings require lubricants with less pickup, whereas more smooth surfaces require a heavier residual coating.
- Wire finish-cleaner surface finishes require less residual lubricants.
Sodium and potassium soaps have higher softening ranges than calcium soaps, but nonetheless, they tend to result in thinner lubricant films after drawing. For this reason, inorganic sodium compounds are often fused into these soaps to enhance lubrication at higher speeds and temperatures. Since these inorganic compounds include borax and soda ash, one problem encountered with sodium soaps is moisture susceptibility. These soaps, in humid environments, tend to pick up moisture more readily than calcium soaps. Storage in polyethylene-lined drums reduces this problem. Increased softening points go hand in hand with increased melt viscosity at the requisite operating temperatures and also enhanced compressive strength. This has resulted in the trend toward sodium and sodium/potassium mixed soaps in many demanding high-speed applications. Lime has similar effects when fused into sodium soaps, and so it is useful for more demanding applications. A general guide for lubricant selection is given in Figure.
Mixed soaps, such as mixtures of insoluble with soluble soaps (calcium stearate + sodium stearate) and soluble with soluble soaps (sodium stearate + potassium stearate) are very useful. The advantage of mixed soaps is that they allow the range of lubricant performance to be extended since there is generally a wider softening range. This can be important, particularly in multi-hole machines or in systems with somewhat greater process variability.
Particle Size-and the distribution of particle sizes within a powdered lubricant are critical parameters in selection of the proper lubricant for wiredrawing. Particle size and distribution affect lubricant pickup and are also important for plant hygiene. It is necessary that lubricant particles be sufficiently fine to be picked up by the rod (or wire) as it passes through the die box . Smaller particles adhere to the surface more easily and become plastic to allow for flow through the die. As a general rule, however, very fine particles.
do not flow well. Instead, they tend to pack and then to channel about the wire passing through, a phenomenon known as “tunneling.” This effect is especially pronounced when the wire is under back tension and has no lateral motion in the die box. Therefore it is desirable to maintain a distribution of particle sizes consisting of both larger and smaller particles so that the powder moves about the wire and finer particles are picked up. Coarser particles, during this operation, abrade to replenish the supply of fine particles.
As a rule of thumb, pickled rod with a lubricant carrier should be run with a grind size ranging from 1/4 in. through 5/32 to 1/8 in.; intermediate size wire should use a 1/8 or 1/16 in. grind size; fine wire sizes usually require a 1/32 in. grind size. However, it is generally not necessary to use multiple sizes of lubricant throughout the entire machine during drawing as long as the lubricant is able to break down to provide the requisite sizes.
FIG F12
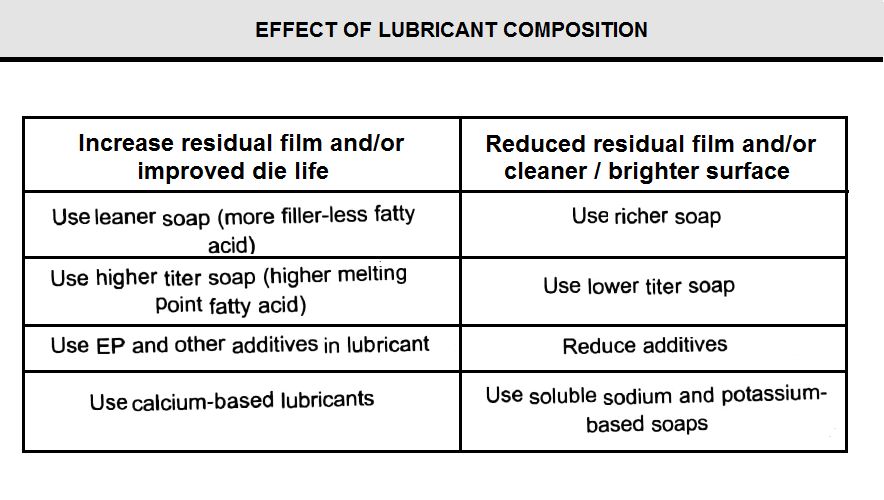
Hygiene and Dusting
Two lubricant morphologies have been developed to enhance hygiene: palletized products and beaded products. They are sometimes used instead of ground material to eliminate fine dust from flying about during handling of wiredrawing lubricants. Also, it is thought that these morphologies promote a more uniform “rolling” action of the lubricant powder during wire passage through the die. Unfortunately, the greatest source of dust during wiredrawing results from fine fused flakes of lubricant, which have carried through the die and are then blown up into the air by the action of the capstan. This problem is not improved by the use of either a palletized or beaded product. Concern about dust levels has resulted in development work suggesting that lubricant rheology, i.e., the deformation or flow of a material in response to applied stresses, must be closely matched to a specific machine and application.
Lubricant Testing
Currently, there are no techniques available that can be used reliably to predict performance of wiredrawing lubricants. The only true test is to run the product on the specific machine. Nevertheless, there is great interest in the development of techniques to predict lubricant performance.
Characterization Methods. In material characterization, it is desirable to develop specific structure-property relationships that can be used to predict performance. In the case of wiredrawing lubricants, some of the important properties are:
- Soap microstructures
- Thermal properties of the soap
- Rheological properties of the soap
Soap microstructure depends on chemistry and thermal/mechanical processing, and so it is very difficult to quantify, especially since the majority of formulations and manufacturing techniques remain proprietary. For that reason, a discussion of soap microstructure is beyond the scope of this chapter.
Thermal properties of soap are typically characterized by using calorimetric techniques such as Differential Scanning Calorimetry (DSC) or Thermal Gravimetric Analysis (TGA). DSC characterizes thermodynamic changes as a function of temperature revealing melting points, glass transition temperatures, and chemical reactions. The TGA technique provides an indication of mechanical changes resulting from thermodynamic events as a function of temperature. It has been suggested that these techniques can be used to determine which type of lubricant should be used based on the temperatures at which the thermal events take place.
However, there are serious difficulties in using these data for predictive purposes. The significant effects of high pressures on soap in the die on thermal properties, such as melting point, have not been determined due to limited availability of high pressure DSC equipment. Also, characterization of thermal properties without an understanding of rheological effects is incomplete, particularly since the impact of fillers and EP additives is to modify melt properties to enhance performance.
For these reasons, others have relied on rheological measurements to determine melt viscosity of soaps during the wiredrawing process. Smith studied soap viscosity as a function of temperature to investigate conditions in a drawing die and to examine the effects obtained in a multi-hole drawing operation. While this work demonstrated that viscosity measurements could identify soaps from one another, they were limited in that they were based on measurements at low pressure. Further, the actual results could not be used to predict lubricant performance during wiredrawing.
Montmitonnet and his colleagues made more fundamental studies of the effects of pressure on thermal and viscometric properties simple soaps. This work clearly showed that pressure significantly impacts thermal transitions and viscosity. Further, structure and property relationships based on these results characterize the behavior of soaps during wiredrawing. Much work remains to develop a better predictive test for wiredrawing soaps.