E6013 Welding Electrode Production
Introduction
Appropriate Machinery for E6013 Electrode Production
Suitable Raw Materials for E6013 Electrode Production
Core Wire
Powders
Binders
Proper Formulation for E6013 Electrode Production
Introduction
E6013 electrode is known as the most widely used manual electrode. This product consists of a steel core wire with a JIS G3503 (SWRY11) core and powders such as Calcium Carbonate, Silicon, Iron, Rutile, Mica, Cellulose, CMC, Kaolin, Potassium feldspar, Ferromanganese and Kieselguhr.
To press these powders on the surface of the wire, potassium silicate liquid binder is used.
The production of quality E6013 welding electrodes requires attention to several issues: Appropriate production machinery, suitable raw materials, and Proper formulation. If any of these issues are not considered, the final result will not be appropriate.
In this article, we will show you the way to reach the appropriate final result by mentioning an example of E6013 electrode production. also you can read E7018 Manufacturing Guide here.
If you are not the welding electrode producer and you are E6013 Consumer.This Article is for you.
Appropriate Machinery for E6013 Electrode Production
As mentioned in Welding Electrode Manufacturing and Machinery Purchasing Guide, there are generally two types of electrode production machines, the Hydraulic extruder machine and the Screw extruder machine.
The Screw extruder has less power compared to the hydraulic type to press the Flux on the surface of the wire. This machine can produce electrodes that require less force for pressing due to the presence of fluidizing materials (materials such as cellulose, mica, CMC, etc.).
E6013 Welding electrode has the ability to be produced by this machine due to the presence of these materials in its composition.
The positive point of this type of Machine compared with the Hydraulic type is the higher production efficiency and the simplicity of its maintenance.
On the other hand, the hydraulic press machine can produce all kinds of electrodes due to the high power of the hydraulic force. In the picture below, you can see a view of these two types of Machines.
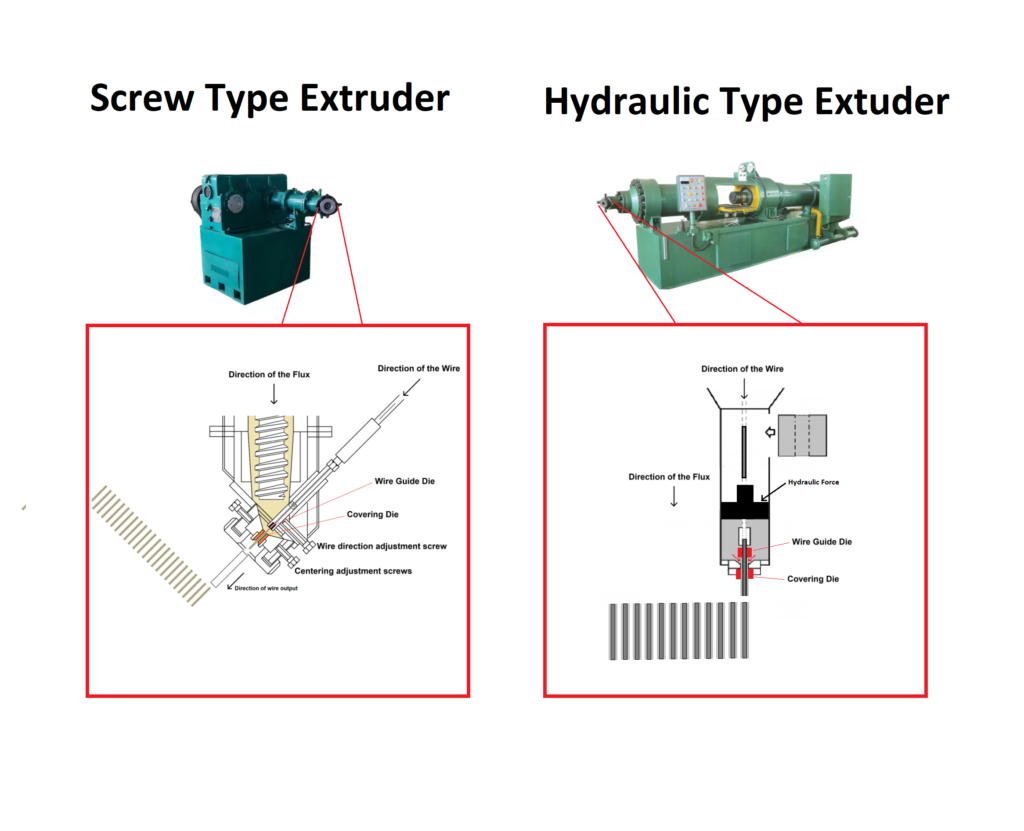
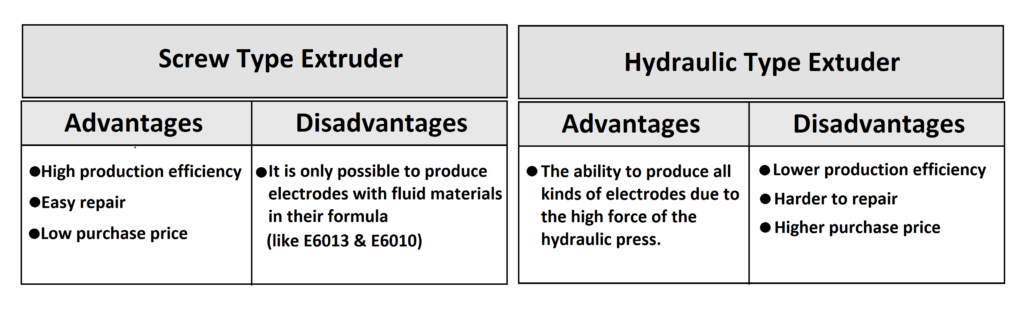
An important point in all types of welding electrode production devices is the issue of Flux Coating Die and wire guiding Die. The Flux Coating Die has the task of pressing the Flux on the surface of the wire by applied pressure. The inner diameter of this part is adjusted according to the desired diameter of the electrode cover. Also The wire guiding Die is responsible for adjusting the wire path to be in the center of the coating. Both of these Dies are made of tungsten carbide. Below is pictures of type of these Dies and their suggested dimensions.
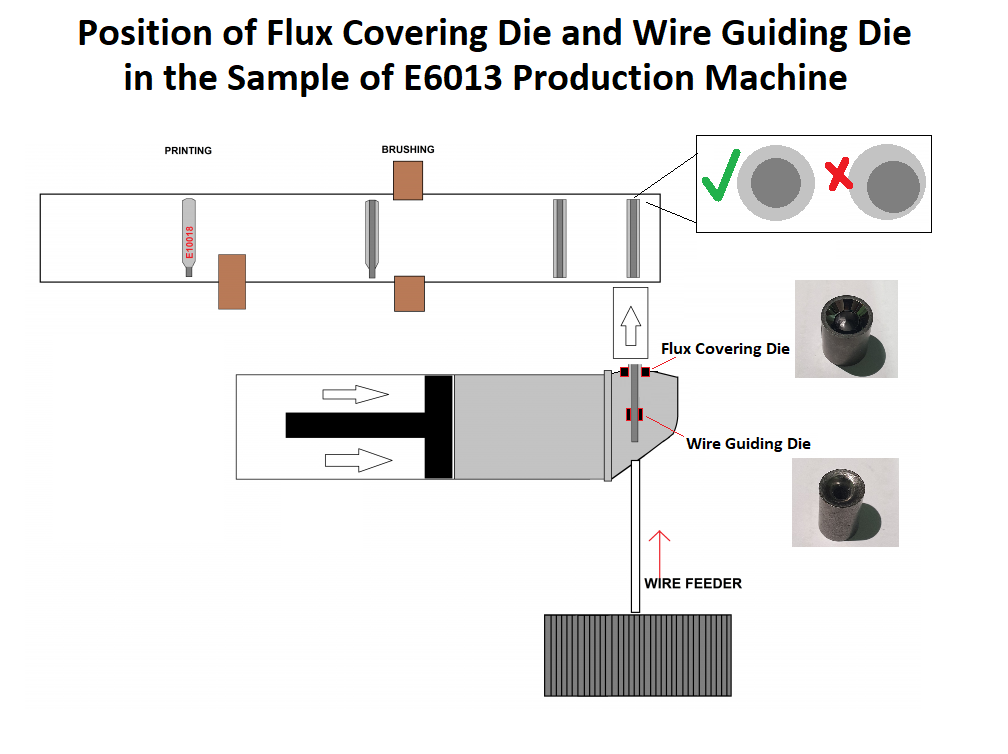
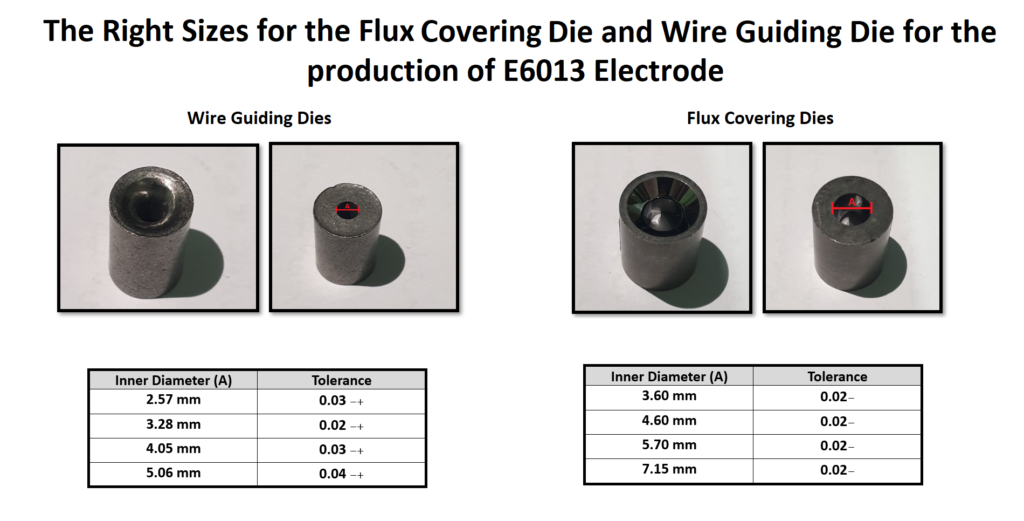
Suitable Raw Materials for E6013 Electrode Production
The raw materials for the production of E6013 electrodes are divided into three categories: powders, Binders, and wire.
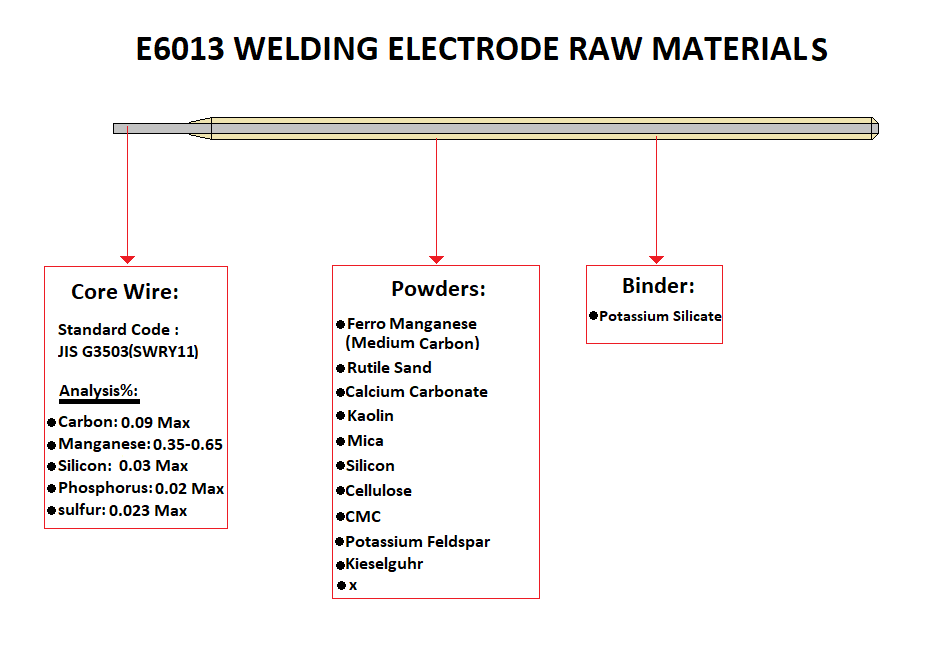
Core Wire for E6013 Production
The drawn and cut wire has specific quality characteristics. These specifications are obtained if the necessary technical points are paid attention during production. The specifications of the final core wire are as follows:
-Clean and without any dirt and grease on the surface of the wire.
-Not having edge in the place of cutting at the head and bottom of the wire.
-Not having a bend in the length of the wire.
-No Ovality.
-The diameter and length of the wire should be in the appropriate range.
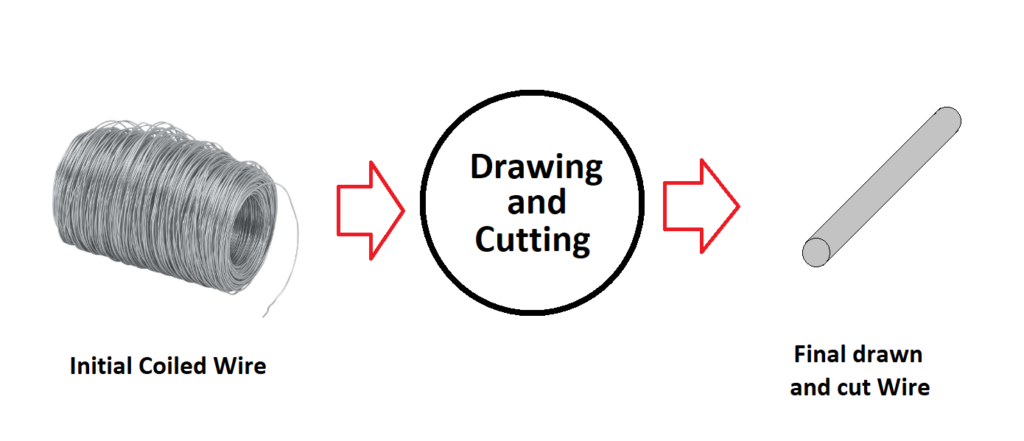
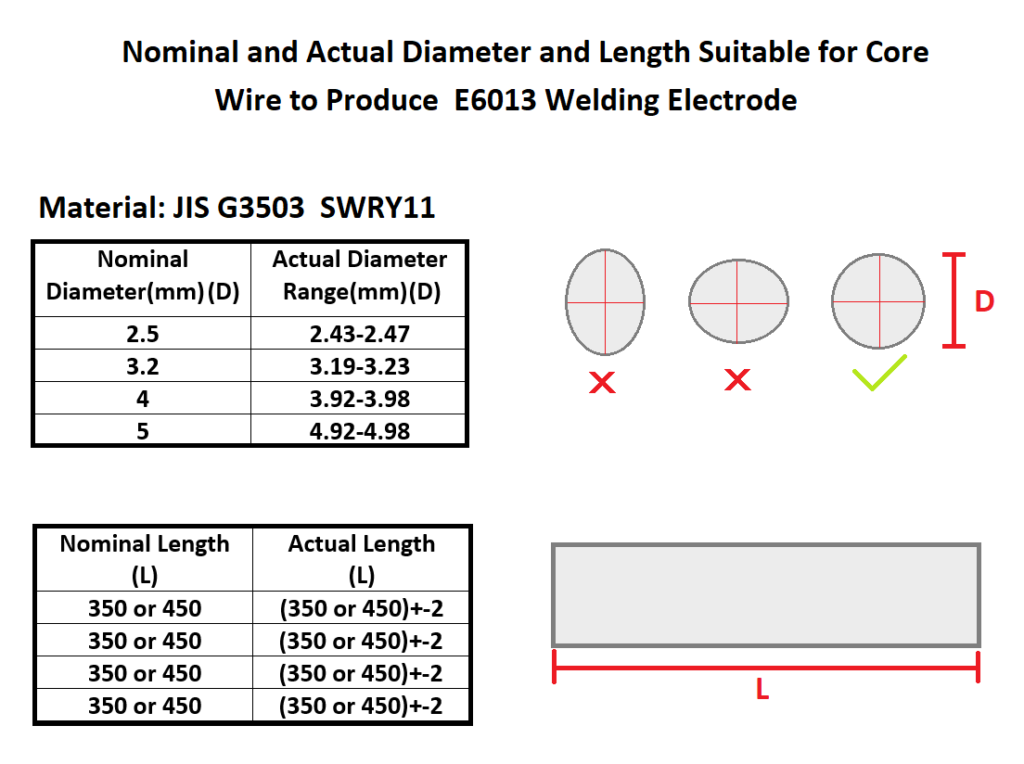
Powders for E6013 Production
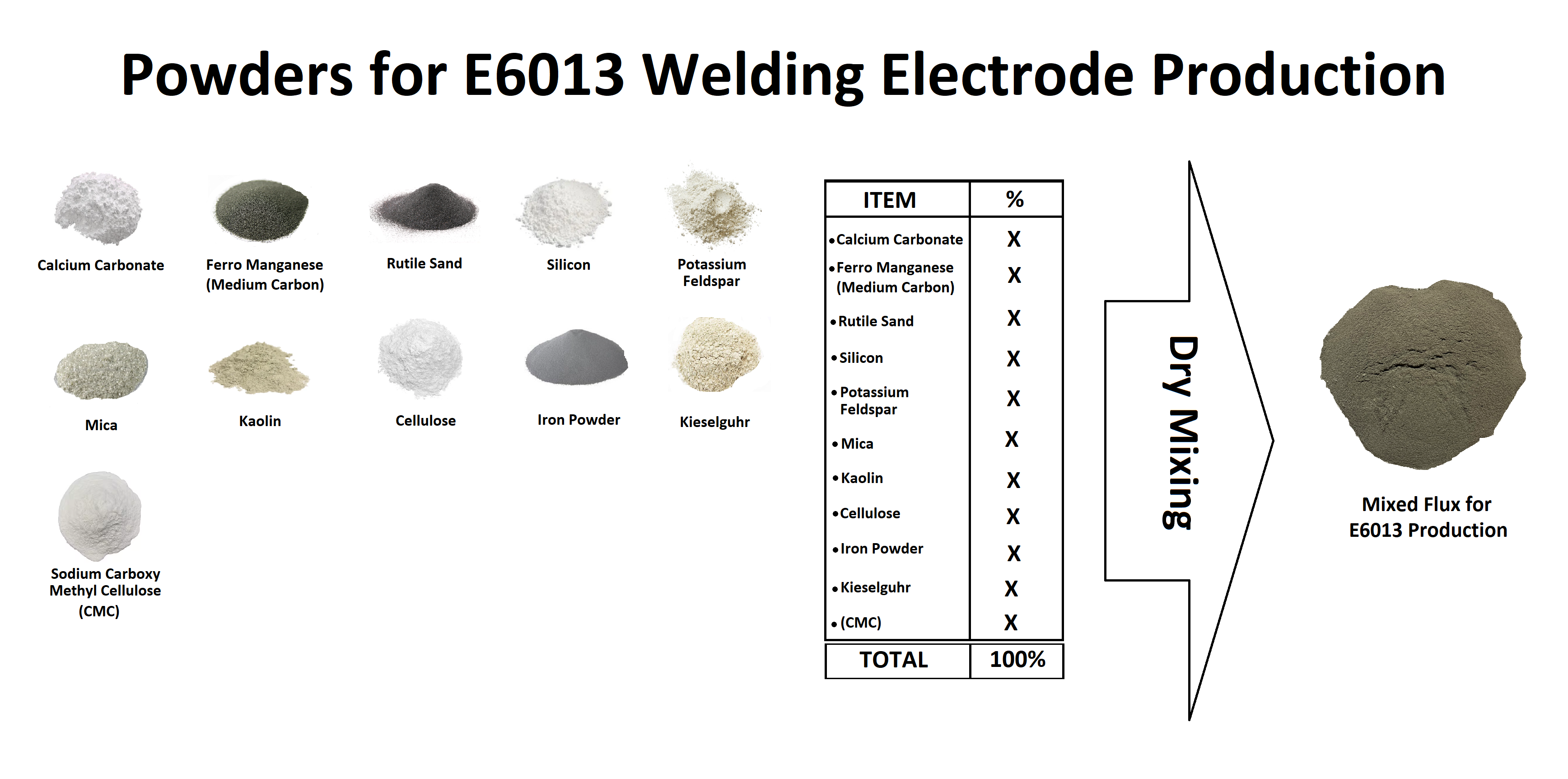
Each of the described materials has its own unique characteristics, and for a better understanding of this issue, one of the materials with a high weight percentage is mentioned as an example.
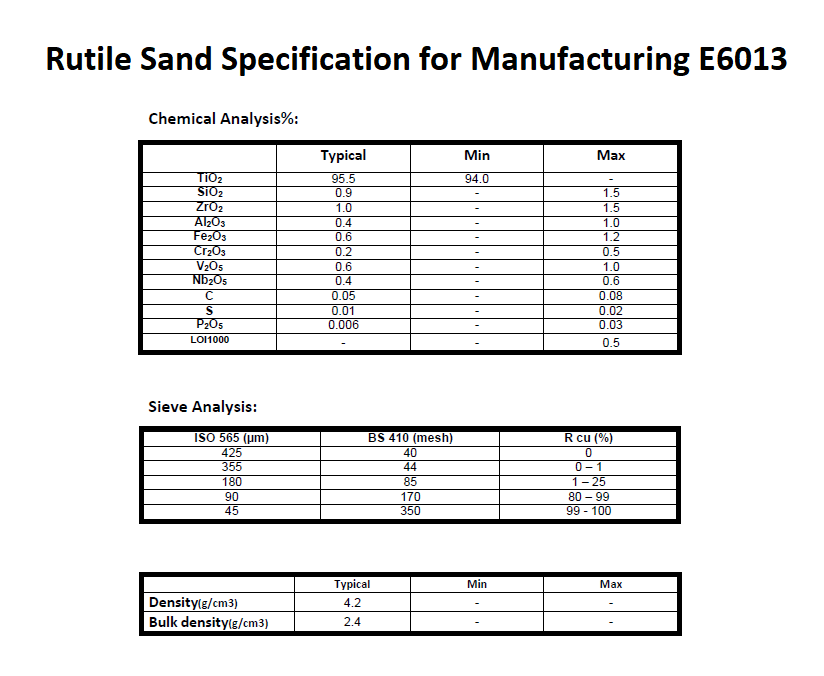
Binder for E6013 Production
Potassium silicate binder is a crucial component used in the manufacturing of E6013 welding electrodes. This binder acts as a glue to hold the coating materials together and ensure proper adhesion to the core wire. The potassium silicate not only provides the necessary mechanical strength but also contributes to the welding characteristics of the electrode, such as arc stability and ease of slag removal.
Properties and Benefits:
- Arc Stability: Potassium silicate contributes to a stable and smooth arc, which is essential for achieving high-quality welds.
- Slag Formation: It helps in the formation of a protective slag layer that covers the weld pool, protecting it from atmospheric contamination.
- Ease of Ignition: Electrodes with potassium silicate binders are known for their easy arc starting and re-striking capabilities.
- Moisture Resistance: Potassium silicate helps in maintaining the integrity of the electrode coating by resisting moisture absorption, which is critical for preventing hydrogen-induced cracking in welds.
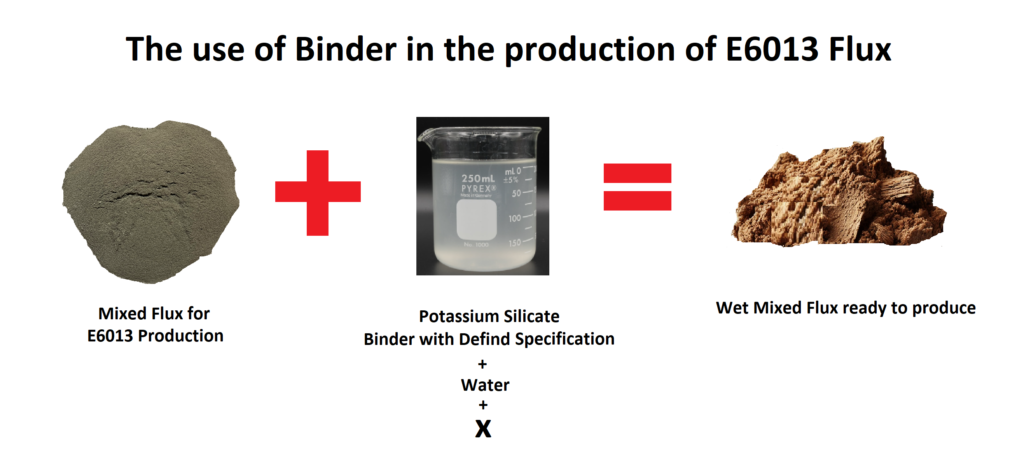
Proper Formulation for E6013 Electrode Production
As mentioned, the formulation of E6013 was shown in the above image. However, in order to achieve a quality product, not only the formulation of the coating is important, but the necessary instructions for the production of this product are also needed.
You can consider a simple type of E6013 electrode coating formulation, which includes Calcium Carbonate, Mica, Cellulose, Kaolin, Ferromanganese(MC),Silica, Potassium Feldspar, Rutile Sand. Also, The required Binder is Liquid potassium silicate, which is added in the dry powder mixture. (if you want to produce professional high quality E6013 Welding Electrode , please CONTACT US)
The following information is also available in the formula sheet: Specifications such as the Diameter of the electrode coating, the Pressure of the Flux coating on the surface of the wire and the amount of Binder and water to produce the wet Flux, Baking time and temperature, etc.
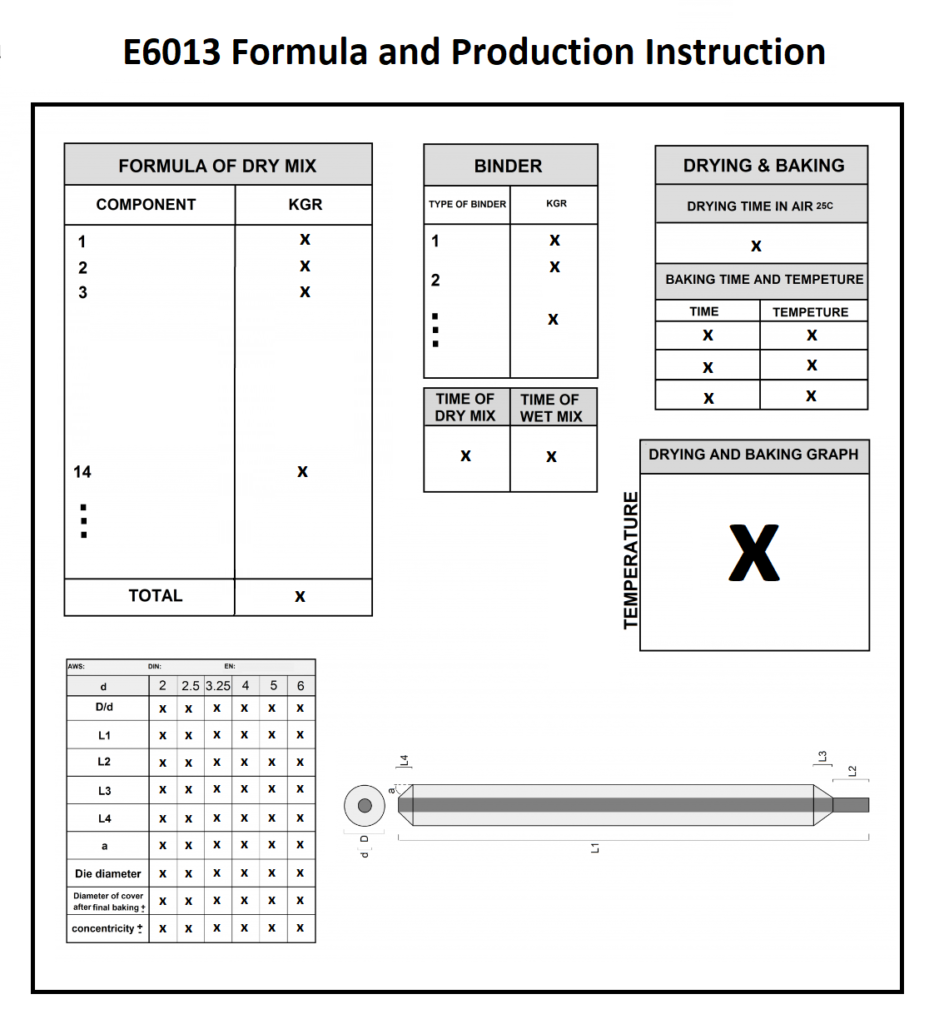