Cellulosic Electrodes
Rutile Electrodes
Lime Type Electrodes
Acid Electrodes
Electrode Coatings High Amounts of Iron Powder
Classification by Manufacturing Process
Classification Based on Chemical Composition
Classification Based on Type of Slags
Classification Based on Chemical Properties
Introduction
Welding Flux plays an important role in the quality of the final product. In this section, we have explained the details of them. These materials have various functions such as protecting against the entry of impurities and alloying. They are mineral or synthetic in nature.
These materials are usually in powder form and their approved specifications will be present in Know-How, including chemical analysis and granulation, and other specifications.
Flux Classification of Covered Electrodes
In general, the covered electrodes can be divided into the following categories according to the type of cover.The major components of the coating determine the four major types of covered electrodes: cellulosic, rutile, lime or lime– titania, and iron powder.
Cellulosic Electrodes:
as their name implies, incorporate considerable wood flour or other forms of refined cellulose (figure B10) . The combustion of the cellulose provides the shielding gas that surrounds the arc. Slag-forming materials are incorporated in the coating to control the molten metal as it flows into the joint.
FIG B10
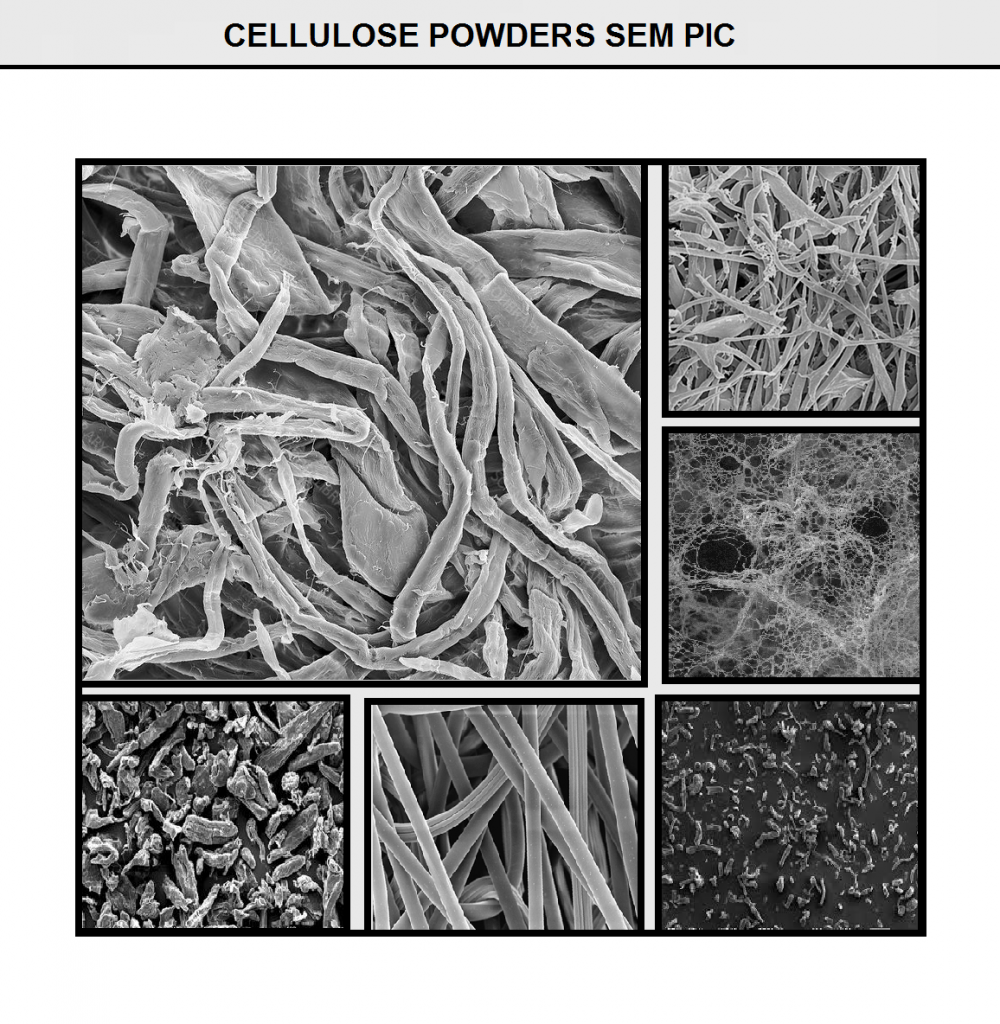
For welding in other than the flat position, for example in pipeline welds where the operator must weld completely around the pipe, a fast-freezing slag is needed to hold the molten weld metal in the joint while the weld is solidifying. This is one of the principal uses of cellulosic electrodes. An operator may start the joint in the six o’clock position (overhead) and progress upward to the three o’clock position (vertical), thence to the twelve o’clock position (flat).
Cellulosic electrodes for use with alternating current contain potassium silicate, rather than sodium silicate, as a binder; the potassium ionizes the arc more readily, giving it stability as the current alternates between positive and negative polarity.
according to different nature of the cellulose, combination of It with heavy metal powders requires special engineering and techniques to combine these powders in order to provide a homogeneous mix of materials for manufacturing electrode coating (figure C10).
FIG C10
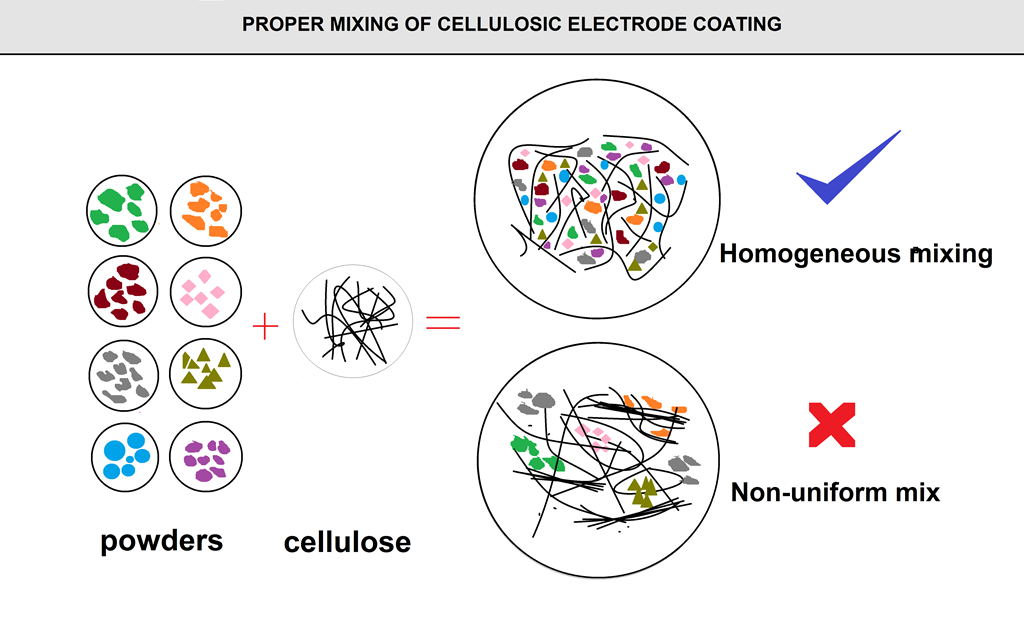
Different structures cellulose lead into different effects in production process as well as performance of final products. Cellulose powder can be classified in 5 shapes that each shape has its own specification.
Available in various sizes and structures:
- Long fibers
- Cubic particles
- Granules
- Spheres
- Cellulose gels
Another important issue to consider in cellulosic electrodes is that regard to the production of protective gases, including hydrogen, Positive and negative properties will be created in the weld pool.
This has two consequences: good protection of the weld pool and high level of diffusible hydrogen in the weld metal and heat-affected zone (HAZ). The high percentage of hydrogen is the cause of the high deposition rate and deeper penetration by the creation of the strong arc for which this kind of electrode is well known.
Another result of the hydrogen content of the gas shield is the required for higher voltage.
However, the high hydrogen content in the shielding gas could be leaded some defects. It causes a high level of diffusible hydrogen in the weld, which is one of the parameters influence on hydrogen cracking (also called cold cracking).
Therefore, in the design formulation of cellulosic electrodes, despite the production of hydrogen gas for performing the specified tasks, it is necessary to prevent the entry of this harmful gas into the weld pool or to purify it by adding other materials (figure F15).
FIG F15
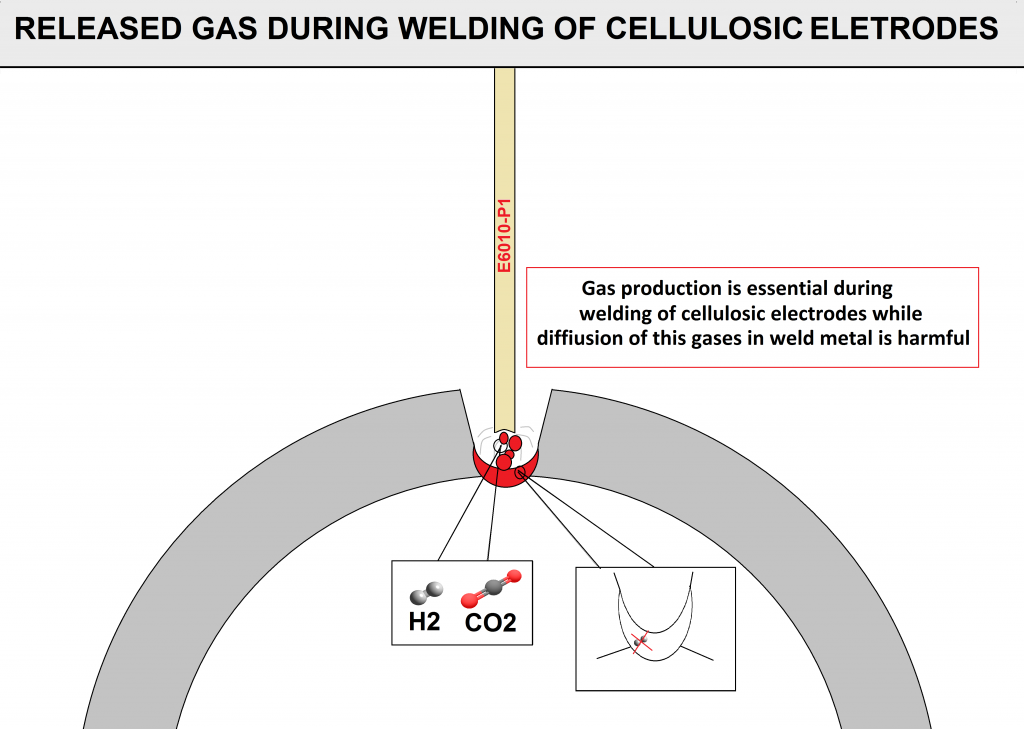
Rutile Electrodes:
contain more than 50% rutile, providing a very stable arc. For gas shielding the electrode also contains some cellulose, along with deoxidizers, and arc stabilizers. As with the cellulosic electrodes, rutile types can be used in all positions, but the arc does not penetrate as deeply as the cellulosic type.This allows the weld to fill gaps more easily. A dense slag that was created over the weld surface will be removed. These electrodes are preferred by less-skilled operators and consequently are used for a wide variety of maintenance operations. The rutile type which is made for using with alternating current has a very stable arc, and, with its low penetrating character, is especially suitable for sheet metal joining. Another type of rutile electrodes include a comparative amount of iron powder, which oxidies and adds to the weld metal.
Lime Type Electrodes:
are generally called basic type electrodes because they produce a basic slag formed largely from limestone and fluorspar.
Decomposition of calcium carbonate forms carbon dioxide and carbon monoxide that shield the arc from atmospheric contamination. During manufacture with alkaline liquid silicates as binders, lime type electrodes are baked at much higher temperatures than those containing cellulose and thus produce welds characterized by low hydrogen contents. Such electrodes frequently are referred to as low-hydrogen electrodes, allowing them to be used on low-alloy steels where hydrogen cracking can be a problem. They are suitable for use on direct current with the electrode connected to the positive terminal.
Unskilled operators may find it more difficult to maintain a steady arc with these electrodes; thus variations with up to 8% titania (lime–titania electrodes) have been developed to improve arc stability. With the addition of potassium silicate as the binder, this type of electrode can be used with alternating current.
Basic electrodes are usable in all positions, although their slags are somewhat more difficult to remove; the addition of titania and sometimes zirconia makes the slags more friable when cold and thus more readily removed.
As with the cellulosic types, iron powder additions have improved the ease of operation and provide additional weld metal, and are now the most popular of the low-hydrogen types. They are used not only for carbon steels, but also for stainless steels, low-alloy steels, and even some nonferrous alloy electrodes.
Acid Electrodes:
have large amounts of iron oxides in the coating which would result in high oxygen content in the weld metal and poor mechanical properties. It is therefore necessary to incorporate large amounts of de-oxidants such as Ferro-manganese and Ferro-silicon in the flux. Although they produce smooth flat weld beads of good appearance and can be used on rusty and scaled steel items the mechanical properties tend to be inferior to the rutile and basic coated electrodes. They are also more sensitive to solidification cracking and are therefore little used.
Electrode Coatings with Very High Amounts of Iron Powder:
in which the thick coatings comprise as much as 50% of the electrode weight, are also available. The iron powder adds considerably to the amount of weld metal produced by the metallic core; thus these electrodes sometimes are referred to as high-efficiency electrodes. The relatively thick covering and the conductivity provided by the iron powder allow the electrode to rest on the weld seam to produce a flat groove weld. This sometimes is referred to as gravity welding.
Submerged Arc Welding Fluxes Classification
There are two flux types: fused and unfused types (bonded and agglomerated).
Fused Flux
various mineral materials are mixed together in proportion as formula indicates, then heated and melted in electric furnace at 1300℃. Fused materials are queened in water, granulized and sieved to get fused flux finally. Raw materials include manganese ore fines, silica, magnesite, fluorite, quick lime, ilmenite in addition with cryolite and borax. All raw materials should go through a drying process at 150-200℃ to remove excessive moisture content. Due to fusing process at high temperature, carbonate, deoxidant and alloying agent addition is impossible. It is difficult to make highly basic fluxes. Moreover, it is impossible to keep raw material proportion after fusing process. Final products are compounds.
Fused fluxes are classified into glass-like type, crystal type, pumiceous type by granule structure. The apparent density of glass-like type and crystal type is 1.1-1.8g/cm3, while the apparent density of pumiceous flux is 0.7-1.0g/cm3.
Unfused Flux
Unfused type is made by these process: various materials in form of powder are mixed together with binder. next step They are made into particles with certain granular size. Final process is drying or sintering.(see saw flux manufacturing in wespec.net) Raw materials to produce unfused flux are similar with materials to produce electrode coating. The difference is unfused materials have strict requirement for composition and granular size. Powders are mixed in proportion with addition of binder to get wet materials. Wet materials are made into granules, usually 0.5-2mm. Wet granules are sent into rotary dryer for solidification and drying purpose at 150-200℃. Finally, they are fed into rotary kiln for sintering process. According to sintering temperature, unfused fluxes are classified into two categories:
1) Bonded type(or ceramic ). Usually, water glass is used as binder. Sintering temperature is 350-500℃. Due to low sintering temperature, bonded flux is more hygroscopic and low in particle strength. This product supply now in China is small.
2) Agglomerated type. The sintering temperature is 700-1000℃. Particles after sintering are ground into granules of certain size. Sintering process improves granule strength and lowers hygroscopicity greatly.
Compared with fused type, agglomerated flux has higher melting point and lower apparent density. So, agglomerated flux is suitable for high energy input cladding. Agglomerated flux can adjust basicity in large scope and still keep good welding performance. Alloy transfer to weld metal is available. Due to the wide application range and simple manufacturing process, agglomerated flux is developing rapidly in recent years.
Below is a comparison of different submerged arc welding flux types (figure P10).
FIG P10
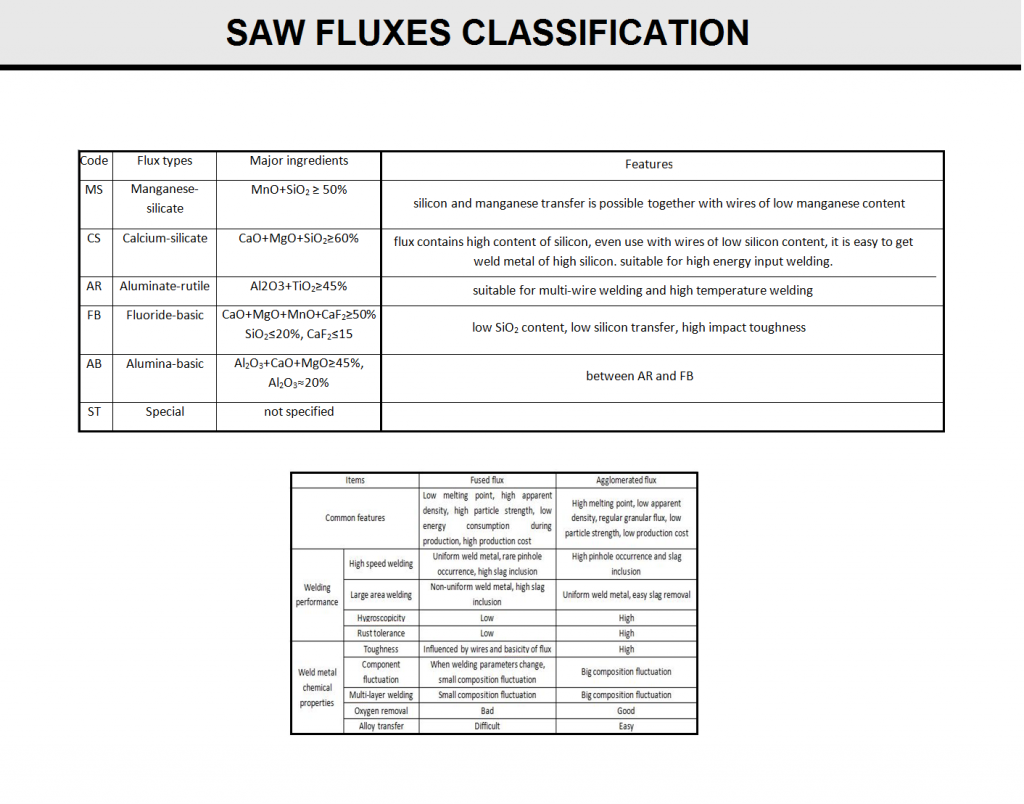
Classification of Saw Flux Based on Chemical Composition
1) by SiO2 Content:
High silicon flux (SiO2>30%), middle silicon flux (SiO2=10%-30%),low silicon flux (SiO2<10%), no silicon flux.
2) by MnO Content:
High manganese flux (MnO>30%), middle manganese flux (MnO=15%-30%), low manganese flux (MnO=2%-15%), no manganese flux.
3) by CaF2 Content:
High fluoride flux (CaF2>30%), middle fluoride flux (CaF2=10-30%), low fluoride flux (CaF2<10%).
4) by MnO, SiO2, CaF2 Content:
One of these types, is high manganese, high silicon, low fluoride flux, the other one is middle manganese, middle silicon, middle fluoride flux, there is also low manganese, middle silicon, middle fluoride flux.
High manganese, high silicon, low fluoride flux is in the category of acidic flux, which is excellent in welding performance, adapted for DC/AC power, and applicable for low carbon steel and low alloy steel.
Middle manganese, middle silicon, middle fluoride flux is in the category of neutral flux, which is both acceptable in welding performance and mechanical properties. Neutral flux is applicable for low alloy steel structure.
No manganese, low silicon, high fluoride flux is in the category of basic flux, which is not so good in welding performance on AC mode. Basic flux has low oxidizing, high toughness and is applicable for high alloy steel like stainless steel.
5) by major ingredients and features: This classification is intuitive and easy to tell the major ingredient and features of welding fluxes. In China, we use this way.
Classification of Saw Flux Based on Type of Slags
1) Silicate type:
Manganese oxide-silicon dioxide type (MnO+SiO2>50%), zirconium oxide-silicon dioxide type (ZrO2+SiO2>35%).
2) Aluminate type:
Alumina-titanium dioxide type (Al2O3+TiO2>45%), basic alumina type (Al2O3+MgO>45%, Al2O3>20).
3) Basic fluoride type:
calcium fluoride type (CaO+MgO+CaF2>50%, SiO2<20%, CaF2>15%).
Classification of Saw Flux Based on Chemical Properties:
Welding flux can be categorized into three groups:
1) Oxidizing Flux:
This flux is oxidable to weld metal. There are two types: one type contains high content of SiO2, MnO, one type contains high content of FeO.
2) Weak Oxidizing Flux:
This flux type has low content of active oxidant like SiO2, MnO, FeO. It is slightly oxidazing to weld metal.
3) Neutral Flux:
This type contains merely oxidant like SiO2, MnO, FeO. Almost no oxidizing to weld metal. Main components are Al2O3, CaO, MgO, FeO, etc.
Classification of Saw Flux Based on Basicity Index:
Basicity is one of the most important metallurgical features of slags. It impacts greatly on metallurgy reactions at slag-metal phase boundary, welding performance and mechanical properties. There are many formulas to calculate basicity. The most popular is the one recommended by IIW (calculation below).
In this formula, various ingredients are calculated by mass fraction. Flux types are categorized into three groups:
1) Acidic Flux (Basicity<1.0)
This flux has excellent welding performance and Uniform weld metal. Alloy transfer to weld metal is possible. However, oxygen content in weld metal is high, impact toughness is low at low temperature.
2) Neutral Flux (Basicity=1.0-1.5)
Chemical composition of deposited metal shares similar content with wires. Oxygen content in weld metal is relatively low.
3) Basic Flux (Basicity>1.5)
This flux shows advantages of low oxygen content in weld metal, high impact toughness, good cracking resistant. However, welding performance is not as good as acidic flux. Basicity of flux higher than 2.0 is called high basicity flux, which could remove sulphur and reduce silicon content.
This flux shows advantages of very low oxygen content in weld metal, high toughness at low temperature. As basicity rises, weld pass becomes narrow and high, and defects like undercuts and slag inclusion are easy to occur.
