Welding Electrode Production Line
The Welding Electrode Production Line has 9 important parts: Drawing-Straightening-Cutting Unit, Weigh and Batching System, Dry & Wet Mixer, Briquette or Slug maker, Wire Feeder, Extrusion Press, Conveyor and Accessories, Furnace, Packing Unit and other smaller Auxiliary parts. In this article, we have introduced each of these components. Also, the Welding Electrode Production Line Workshop is described in two different types.
For more information about Welding Electrode Manufacturing, you can Visit This Page. If you’d like to study E6013 Electrode Production in greater detail, Visit This Page , and for E7018 Electrode Production, Visit this page.
Welding Electrode Production Line Workshops
Welding Electrode Production Line Units
Wire Drawing, Straightening, and Cutting System
Weighing and Batching System
Mixer
Briquette or Slug Maker
Wire Feeder
Extrusion Press
Conveyor & Related Units
Baking Oven
Packing Machines
Welding Electrode Production Line Workshops
In the Welding Electrode Production Line, The process starts with a wire coil, 5.5 mm or 6.5 mm in diameter and weighing 1–2 tons. The coil is fed into a machine that draws, straightens, and cuts the wire into pieces with diameters of 2.5 mm, 3.25 mm, 4 mm, or 5 mm and lengths of 350 mm or 450 mm. These wire pieces are then used as inputs for the Coating Machine.
In another part of the production line, metal, mineral, and chemical powders are retrieved from the warehouse and weighed according to the formula. These powders are first dry-mixed in a mixer and then combined with sodium and potassium silicate binders to form a paste. (The wet and dry mixing can either be done in separate mixers or in a single mixer, depending on its capabilities.)
Depending on the type of coating machine, the paste is either shaped into bricks using a slug press machine before entering the coating machine (Figure 1) or sent directly into the coating machine (Figure 2).
Welding Electrode Production Line Working FlowChart
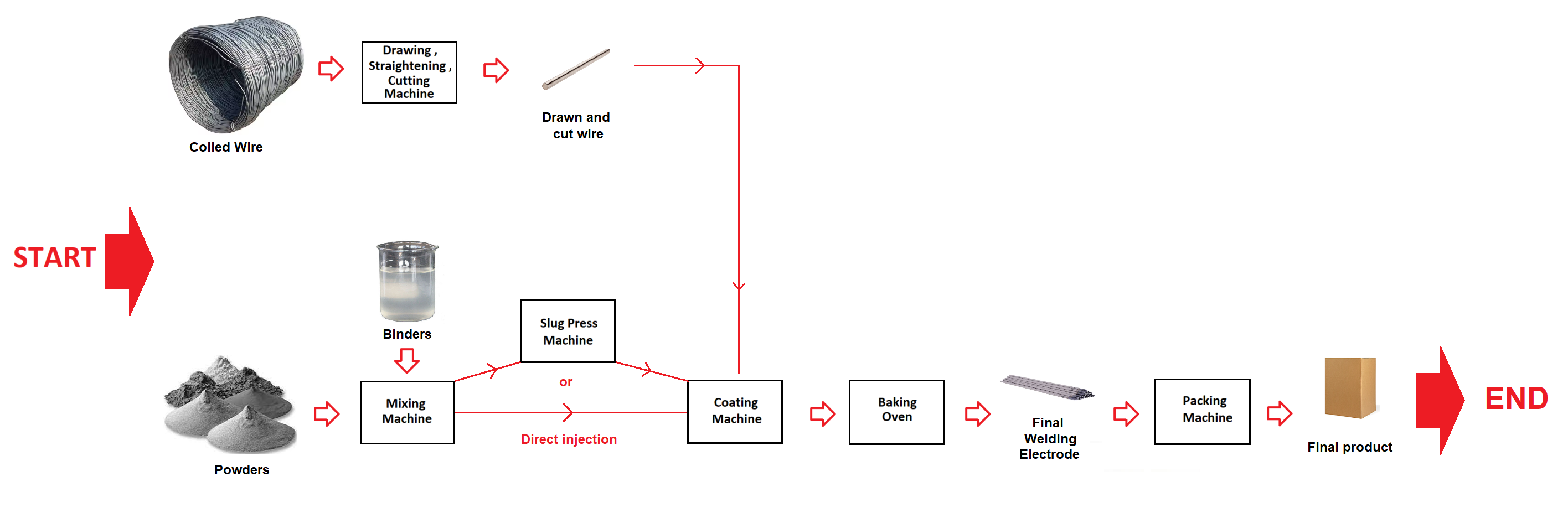
figure 1:Welding Electrode Production Line with Hydraulic Extruder
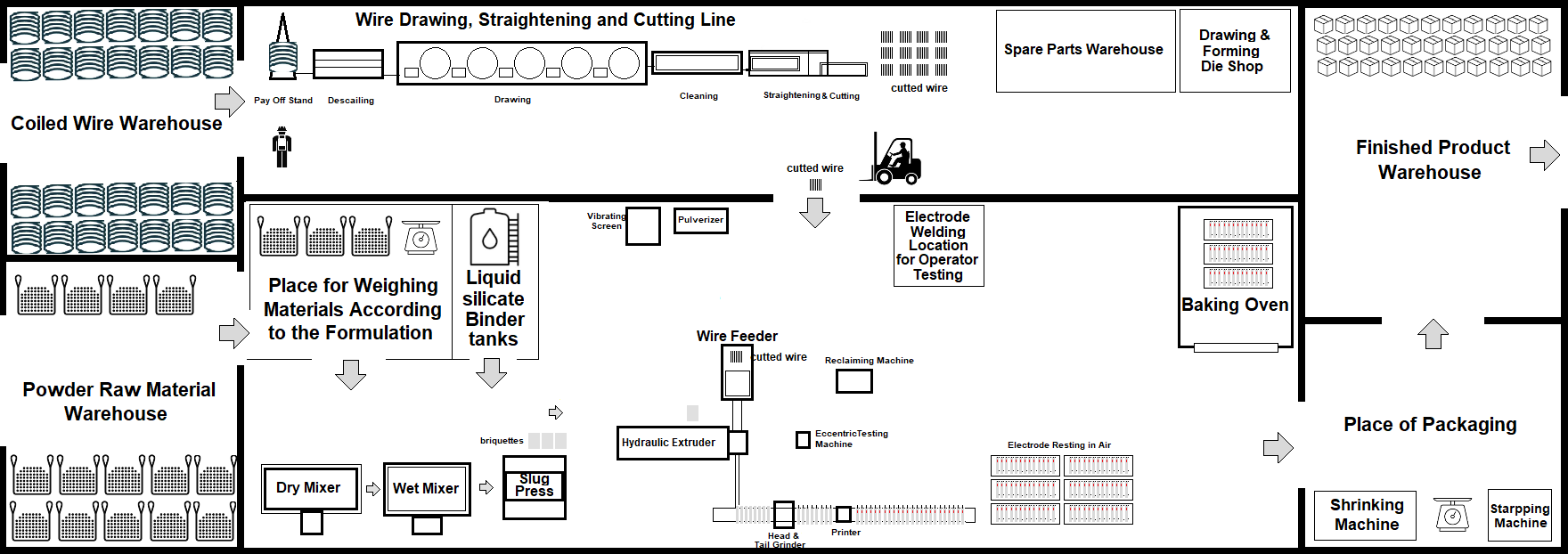
figure 2 :Welding Electrode Production Line Workshop with Screw Extruder
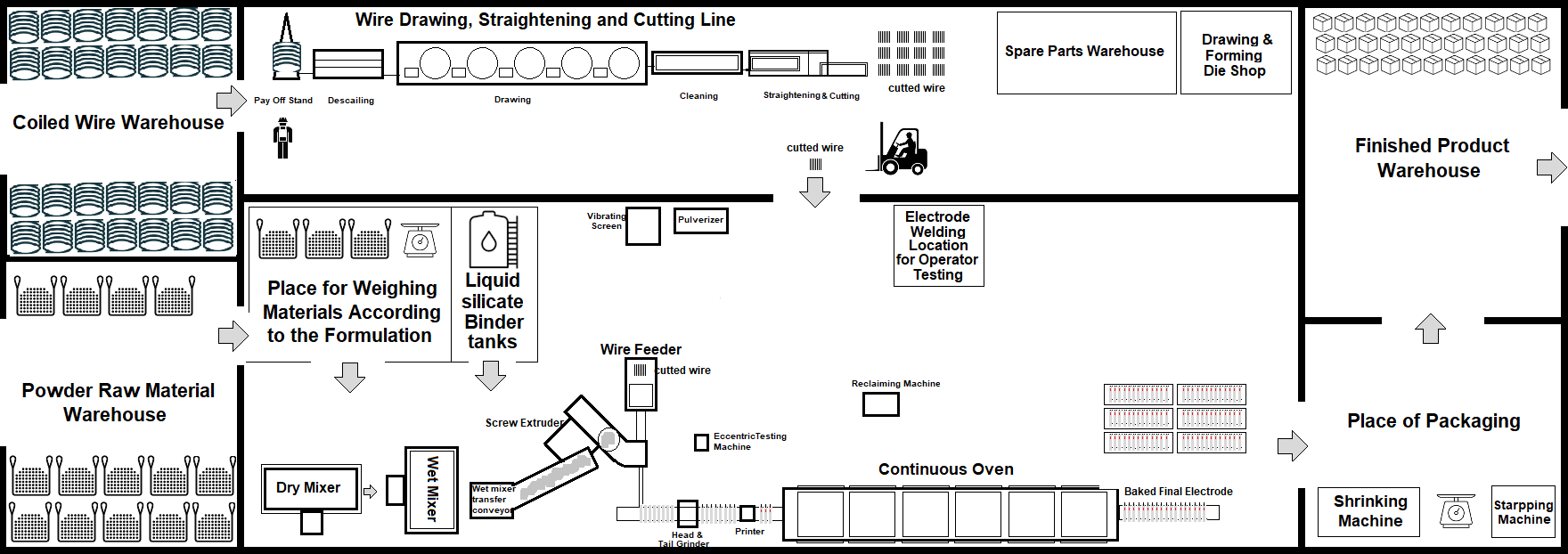
Welding Electrode Production Line Units
In the following, the main parts of the Welding Electrode Production Line are described.
Wire Drawing, Straightening, and Cutting Units
Wire Drawing Machine Working Mechanism
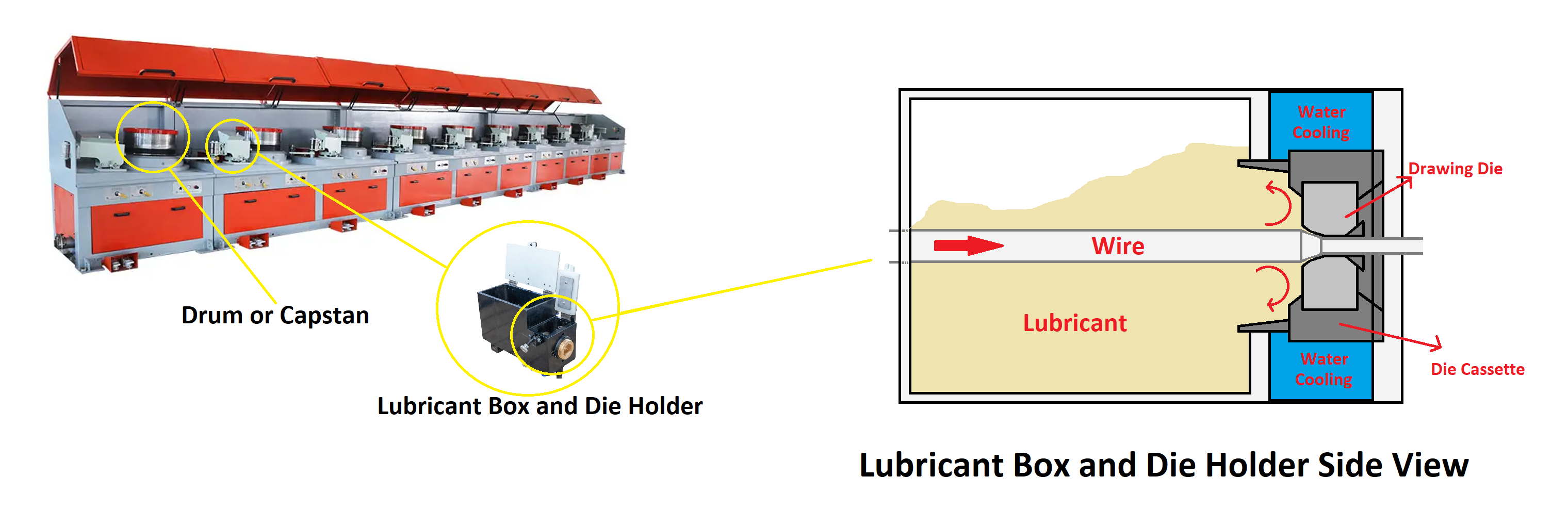
Straightening and Cutting Machine Working Mechanism
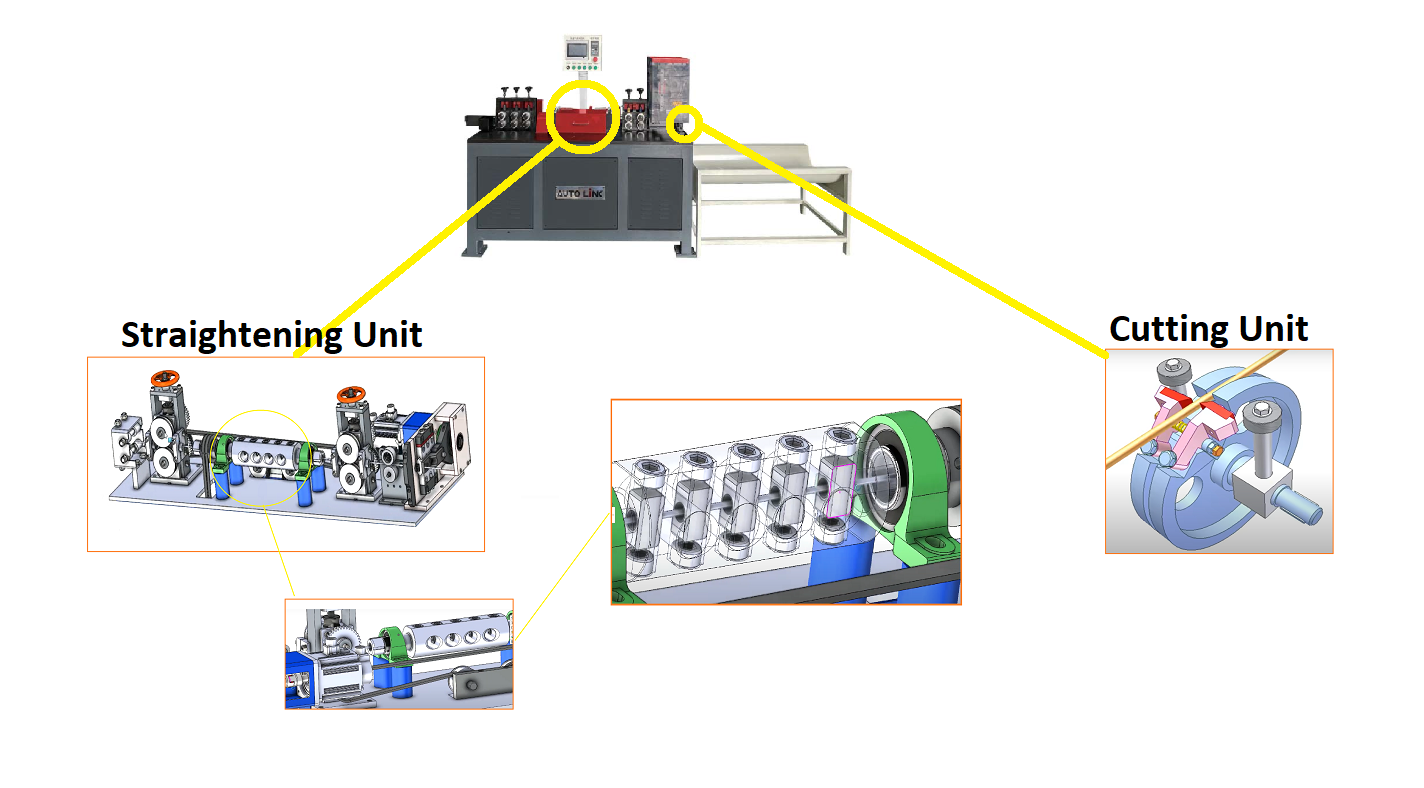
Weigh and Batching System in Welding Electrode Production Line
The Weighing and Batching System for raw materials in Welding Electrode Production Line is a critical process to ensure accurate formulation and consistent quality of the electrode coating. This system involves the precise measurement of various powder and binder components, such as rutile, feldspar, manganese, and other additives, according to the specific Formula for the electrode type being manufactured. The batching process starts with operators or automated systems retrieving materials from storage, weighing them using digital or mechanical scales, and combining them into a batch for mixing. Advanced systems are equipped with load cells and programmable controllers to automate the weighing and batching process, ensuring minimal deviation from the required formula.
To improve efficiency and accuracy, the system often Integrates Software that monitors and records the weight of each material and verifies compliance with the formulation specifications. This reduces the Risk of Human Error and allows for traceability in case of quality issues. The weighed materials are then transferred to the mixing unit for homogenization. Proper weighing and batching are essential to achieve the desired mechanical and chemical properties of the electrodes,making this system a foundational step in the production process.
Weighing and Batching Systems in Welding Electrode Production Line
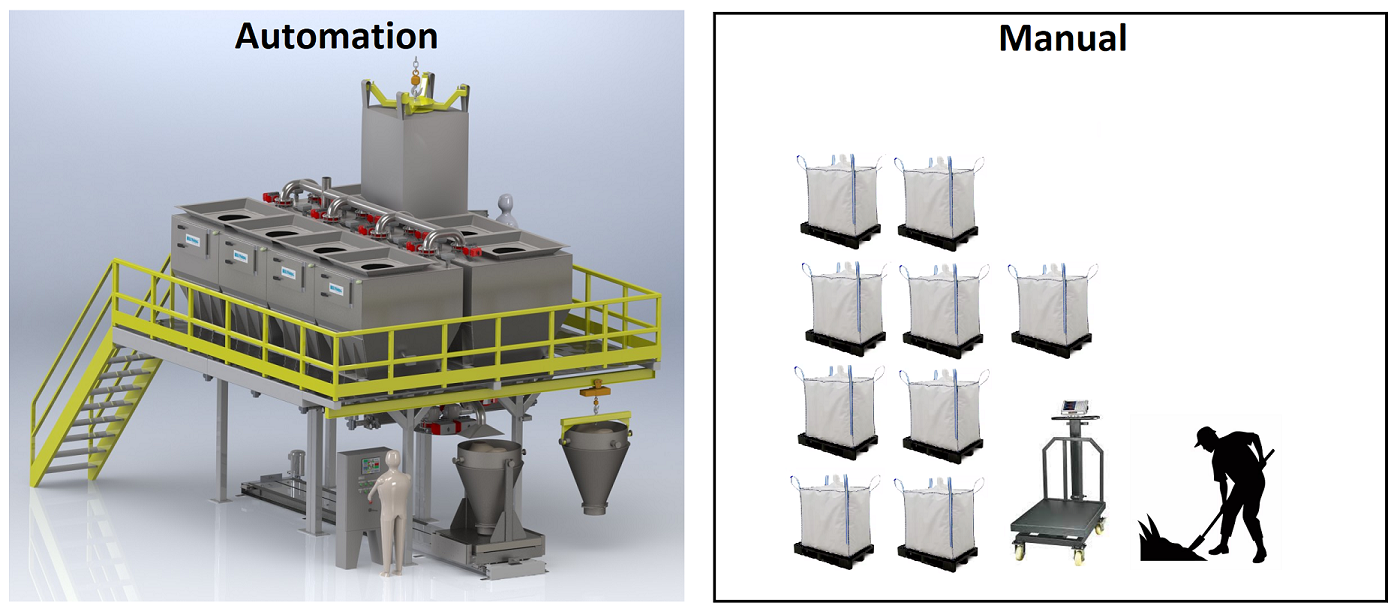
Mixer in Welding Electrode Production Line
Mixing Machine in Welding Electrode Production Line
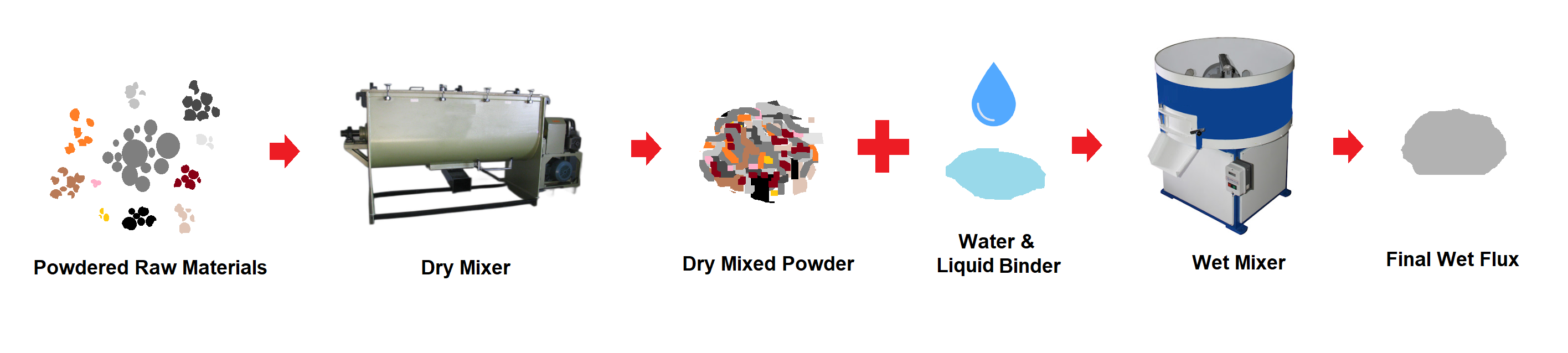
Slug Press in Welding Electrode Production Line
A Slug Press, also known as a Briquette Press, is an essential component of the welding electrode production line. Its function is to compact the prepared coating material into cylindrical or rectangular briquettes, which will later be applied as the coating for welding electrodes. The process begins with mixing the coating material in Mixer, a carefully formulated blend of powders and binders, to achieve a uniform consistency. This mixture is fed into the slug press, where high-pressure dies compress the material into consistent shapes. These briquettes are then used in the Extrusion Press to ensure uniform application onto the electrode core wire.
The slug press plays a critical role in maintaining quality and efficiency in electrode production. By standardizing the size and density of the briquettes, it ensures the even distribution of coating material during the extrusion process, which is vital for the electrode’s performance in welding.
Briquette or Slug Press Machine in Welding Electrode Production Line
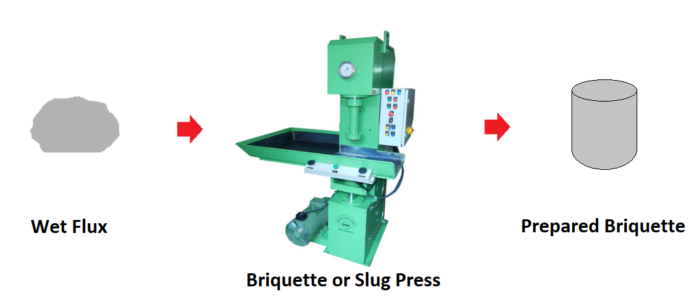
Wire Feeder in Welding Electrode Production Line
In the welding electrode production line, the Drawing, Straightening, and Cutting processes are performed by the dedicated machine.The straightened and cut wire is then transferred to the Wire Feeder Machine,which plays a pivotal role in the subsequent stages. The wire feeder carefully feeds the prepared wire into the Extrusion Press, where it undergoes the coating process to form the final welding electrode.Modern Wire Feeders are equipped with adjustable speed controls and sensors to accommodate different electrode specifications and enhance production efficiency.
Wire Feeder in Welding Electrode Production Line
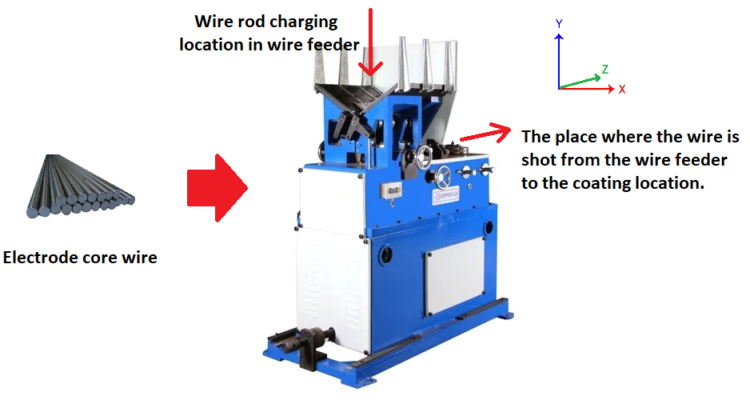
Extrusion Press in Welding Electrode Production Line
The Extrusion Press is a central piece of equipment in the welding electrode production line, responsible for applying the coating material uniformly onto the core wire.The Extrusion Mechanism in the extrusion press is a sophisticated system designed to precisely apply the coating material onto the core wire. The process begins with the coated briquettes or Wet Paste being fed into the machine’s hopper. These briquettes or Paste are then compressed by a Hydraulic or Mechanical Plunger, generating the pressure needed to push the material through a Specially Designed Die. The core wire, simultaneously fed into the die from the wire feeder, passes through the center of the extrusion assembly. As the briquettes are extruded, the coating material envelops the core wire evenly, forming the characteristic cylindrical shape of welding electrodes.
The Extrusion Mechanism is highly adjustable, allowing for fine-tuning of parameters such as Pressure, Die Size, and Feed Rate to suit different electrode diameters and coating compositions. A Consistent and Uniform Extrusion Process is Crucial, as uneven coatings can lead to poor welding performance, such as unstable arcs or spattering. Modern extrusion presses may also feature additional mechanisms for monitoring coating thickness and detecting defects in real-time, ensuring a high-quality end product. The controlled movement of the core wire and the precision of the extrusion die work in tandem to maintain the integrity of the electrode during production, resulting in a durable, high-performance product ready for subsequent processing stages like baking and packaging.
Extrusion Press in Welding Electrode Production Line
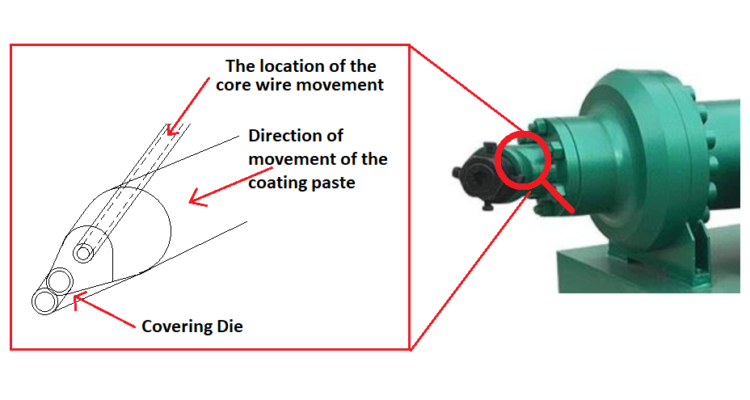
Conveyor and Related Units in Welding Electrode Production Line
The conveyor system, consisting of a head grinder, tail grinder, and words printer, plays a vital role in the finishing stages of the welding electrode production line. After the extrusion process, the electrodes are transferred onto the conveyor for further processing. The head grinder trims the electrode’s front end, ensuring a smooth and precise surface for consistent arc initiation during welding. Similarly, the tail grinder smoothens the rear end of the electrode, creating a clean finish that enhances handling and usability. This grinding process is critical for meeting quality standards and ensuring the electrodes are uniform and defect-free before final packaging.
Integrated into the conveyor system is a words printer, which adds essential markings to each electrode. These markings typically include the electrode’s type, classification, and manufacturer’s details, providing vital information to end-users about the product’s specifications and intended applications. The printing process is automated and synchronized with the conveyor’s movement, ensuring accuracy and efficiency even at high production speeds. Together, the head grinder, tail grinder, and words printer ensure that the electrodes are not only functionally optimized but also professionally labeled, ready for quality assurance checks and distribution to customers.
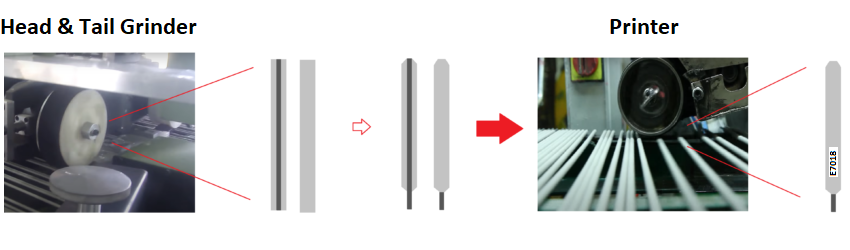
Baking Oven in Welding Electrode Production Line

Packing Machine in Welding Electrode Production Line
Packing types for welding electrodes vary depending on Customer Requirements and Market Standards. Common options include Small Cardboard Boxes, typically holding 2.5 to 5 kilograms of electrodes, and larger master cartons designed to hold multiple smaller boxes, generally weighing 20 to 25 kilograms. For added protection, especially in humid or corrosive environments, electrodes may be Vacuum-Packed or Sealed in plastic bags within the Boxes. This ensures that the electrodes remain dry and free from contaminants, maintaining their quality and performance. Some manufacturers also use Shrink-Wrapping or Laminated Packaging to enhance moisture resistance and provide a professional finish.
The packing machine for Welding Electrode Production Line automates the process of weighing, counting, and packaging electrodes into designated containers. These machines are typically equipped with precision sensors to ensure accurate weight or quantity per pack, reducing errors and waste. Advanced models may feature conveyors, sealing mechanisms, and labeling systems to streamline the packaging process. For vacuum or moisture-proof packaging, specialized vacuum sealers or heat-sealing machines are integrated into the production line. These machines not only improve efficiency but also maintain uniformity and quality in the final packaging, meeting both customer expectations and regulatory standards.(Visit this company website for more information about Welding Electrode Automatic packaging system)