Submerged Arc Welding Flux Production Formula
Introduction
Unlock exclusive technical insights into sub arc welding flux formula. With this guide, manufacturers can achieve consistent, quality flux production while minimizing waste and errors. This technical package delivers practical steps, formulas, and testing protocols for producing superior submerged arc welding fluxes, giving your business a competitive edge. Also you can Read This Article for understanding the way of producing high quality agglomerated Submerged arc welding fluxes.
What Does ``Sub Arc Welding Flux Formula`` Package Include?
1-Precision Weight Formulation
2-Chemical and Physical Specifications of Raw Materials
3-Step-by-Step Production Instructions
4-Quality Control at Every Stage
Schematic View of Agglomerated Submerged Arc Welding Flux Manufacturing Line
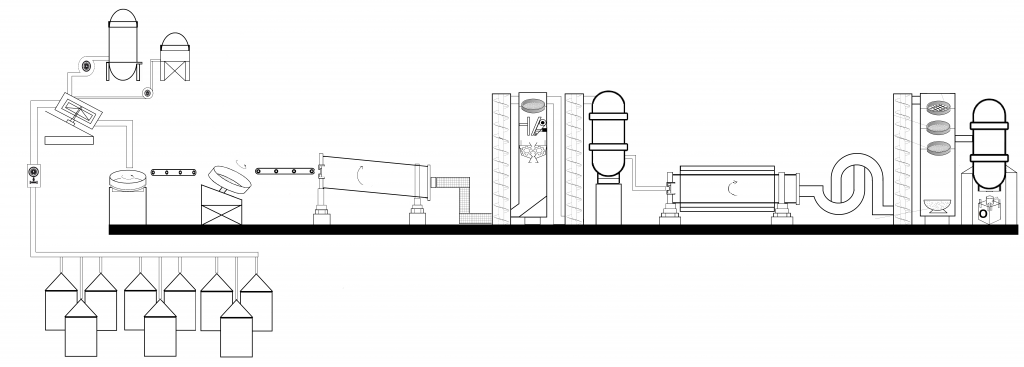
1-Precision Weight Formulation
Our Sub Arc Welding Flux Formula Package offers exact weight formulations for every Final Flux, helping you replicate consistent results batch after batch. Each Formula ensures the flux delivers the necessary properties for smooth welding and strong joints.
2-Chemical and Physical Specifications of Raw Materials
Detailed specifications of the chemical properties of each powder and binder give you the critical insights needed to select only the best-quality raw materials. This includes granulation details to achieve uniformity in particle size, which is essential for smooth production flow, minimal dust, and consistent results.
3-Step-by-Step Production Instructions
1. Raw Material Selection and Preparation
Learn how to properly select, measure, and prepare each raw material, including tips on avoiding contaminants and maintaining material consistency for optimal performance.
2. Mixing and Homogenization Techniques
Our guide includes step-by-step instructions on mixing procedures that yield an even blend of all components. Discover the best practices for mixing speed, duration, and environmental conditions to maintain material stability and reduce downtime.
3. Granulation and Drying Process
The granulation process is key to creating a flux that flows smoothly and delivers reliable results. Our detailed instructions on granulation cover essential parameters like granule size and moisture control. Recommendations on drying techniques help prevent material caking and ensure shelf stability.
4-Quality Control at Every Stage
Quality Control at Every Stage
Maintaining quality is essential to producing flux that meets rigorous industry standards. This section includes:
- Pre-Production Quality Control: Guidelines for testing raw materials to ensure compliance with chemical and physical specifications.
- In-Production Monitoring: Ongoing quality checks during mixing, granulation, and drying to catch inconsistencies early.
- Post-Production Inspections: Final tests for uniform granule size, moisture content, and chemical balance, ensuring every batch meets high standards.
The List of Sub Arc Welding Flux Formula for Production of High Quality Products
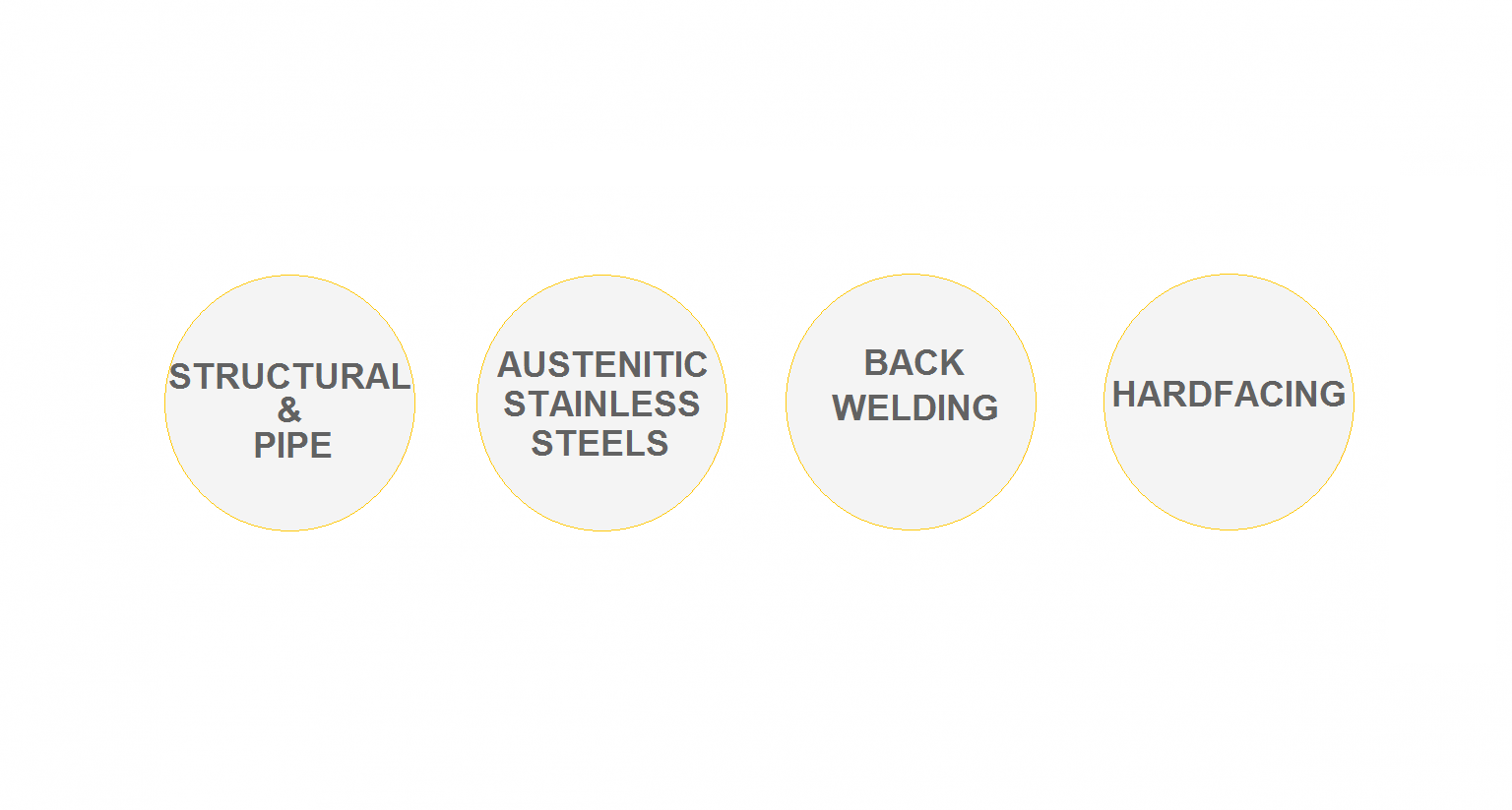
Fluxes for Submerged Arc Welding of General Structural Steels
DIN 32 522 | EN 760 | AWS |
---|---|---|
B AB 1 67 AC 10 M | SA AB 1 67 AC | F7A0-EL12-F7A0-EM12-F7A0-EM12K-F7P0-EM12K |
B AB 1 67 AC 12 MHP5 | SA AB 1 67 AC H5 | F7A4-EM12-F7A4-EM12K-F7P5-EM12K-F7A5-EM13K-F7P5-EM13K-F8A5-EH12K-F7P6-EH12K-F8A4-EA2-F8P4-EA2 |
B AB 1 66 AC 12 | SA AB 1 66 AC | F7A4-EM13K-F7A4-EM12K-F7P5-EM12K-F7P4-EM13K-F8P5-EA2-F8A4-EA2 |
B CS 1 88 AC 10M | SA CS 1 88 AC | F7A2-EM12-F7A2-EM12K-F7P2-EM12K |
B FB 1 55 AC 12 | SA FB 1 55 AC | F6A2-EM12-F6A2-EM12K-F7A2-EM13K-F7A2-EA2-F7P2-EA2 |
B AB 1 67 AC 12 MHP5 | SA AB 1 67 AC H5 | F7P6-EH12K-F7P5-EM13K-F7P5-EM12K-F7A4-EM12-F8A4-EA2-F8A5-EH12K-F7A5-EM13K-F7A4-EM12K |
B AB 1 67 AC 12MHP5 | SA AB 1 67 AC H5 | F7A2-EA2-F7A2-EM12-F7P2-EA2-F7A2-EM12K-F8A4-EH12K |
B AB 1 67 AC 12MHP5 | SA AB 1 67 AC H5 | F7A5-EM13K-F7P6-EH12K-F7A4-EM12K-F7A4-EM12-F7P5-EM13K-F8A5-EH12K-F7P5-EM12K-F8A4-EA2-F8P5-EA2 |
B CS 1 98 AC 12 M | SA CS 1 98 AC | F6A0-EL12-F7A2-EM12-F7P2-EM12 |
B FB 1 66 AC 10MHP5 | SA FB 1 66 AC H5 | F8A2-EB2-F9A8-EF1-F8A8-EH12K-F7A5-EM12-F8P2-EB2-F8P8-EF1-F8P8-EH12K-F7A5-EM12K-F7A5-EM13K-F8A8-EA4-F8A8-EH14-F7P5-EM12K-F7P5-EM13K-F8P8-EA4-F8P8-EH14-F8A4-EA2-F8P5-EA2 |
B FB 1 55 AC 10MHP5 | SA FB 1 55 AC H5 | F8A8-EA4-F8A8-EF1-F8A8-EH12K-F7A5-EM12-F8P8-EA4-F8A2-EB2-F8A8-EH14-F8A4-EA2-F7A6-EM13K-F9A8-EF1-F7P5-EA2-F7P6-EM13K |
B FB 1 65 AC 12 MHP 5 | SA FB 1 65 AC HP 5 | F7P2-EA2-F7A5-EH12K-F6A2-EM12-F7P5-EH12K-F6A2-EM12K-F7A2-EA2-F7A2-EM13K |
B CS 1 77 AC 10 M | SA CS 1 77 AC | F7P2-EM12-F6A0-EL12-F7A2-EM12 |
B AB 1 67 AC 12 MHP5 | SA AB 1 67 AC H5 | F7A4-EM12-F7A4-EM12K-F7P5-EM12K-F7A5-EM13K-F7P5-EM13K-F8A5-EH12K-F7P6-EH12K-F8A4-EA2-F8P5-EA2 |
B MS 1 89 AC 8 SKM | SA MS 1 89 AC | F7A0-EL12-F7A0-EM12 |
B MS 1 88 AC 10 SKM | SA MS 1 88 AC H5 | F7A2-EM12-F7A2-EM12K-F7P0-EM12K |
B AR 1 88 AC 10 SKM | SA AR 1 88 AC | F7A7-EL12-F7P7-EM12-F7A7-EM12-F7A7-EM12K |
B AR 1 88 AC 10 SKM | SA AR 1 88 AC | F7A7-EL12-F7P7-EM12-F7A7-EM12-F7A7-EM12K |
B AR 1 97 AC 10 SKM | SA AR 1 97 AC | F6A2-EL12-F7A7-EM12-F7P7-EM12-F7A7-EM12K |
Fluxes for Submerged Arc Welding of Austenitic Stainless Steels
DIN 32 522 | EN 760 |
---|---|
B FB 6 55455 AC 8 MHP 5 | SA FB 2 55 AC |
B FB 5 63745 DC 8 K | SA FB 2 63 DC |
Flux for Back Welding by Submerged Arc Welding Method
DIN EN 760 |
---|
ACS1 |
Flux for Hard Facing Applications by Submerged Arc Welding Method
DIN 32 522 | EN 760 |
---|---|
B CS 3 97 CCrMo AC 8 | SA CS 3 97 AC |
B CS 3 97 CCrMo AC 8 | SA CS 3 97 AC |