Introduction
Necessary Items to Check the Designed Line
Dry Method With One Rough Module , Two Fine Module and Four Re-spooler
Rough Drawing Module Overview
Fine Drawing Module Overview
ReSpooler Module Overview
Dry Method With Linear Line Includes Both Rough and Fine Modules and Four Re Spooler
Introduction
In general, wire drawing processes can be divided into two types: dry and wet. Each of these methods has its own advantages and disadvantages. Of course, the comparison of these two methods is comparable in drawing below 2 mm, because in the drawing above 2 mm, the wet method is usually used less.
In this article, we are going to describe the production line with modules that have using the dry method. This production line includes one Rough Drawing Module, two Fine Drawing Modules and Four Rewinder. Also, we have described the linear line that includes both Rough and Fine Drawing.
Necessary Items to Check the Designed Line
To check each product line, it is necessary to request 7 items from the seller, these items are as follows:
- Production type
- Working speed
- Size of the production
- Working capacity(24H, 300 days)
- Price
- Power supply
- Installation and debugging
Production Type :
The idea that a production line has the ability to produce all types of ferrous and non-ferrous alloy wires is completely wrong. For example, the stages of drawing stainless steel wires with low carbon steels have completely different stages like the annealing that is necessary for the production of some wires. In the production line that we have described, low carbon steel wire with ER70S-6 code (Related Standard:AWS/ASME SFA-5.18) is considered.
Working Speed:
In the welding wire production process, the efficiency is a function of the Drawing speed.In the production of ER70S-6 welding wire, the speed between 25 and 30 meters per second is desirable,
Size of the Production:
This type of product is usually required in sizes of 0.6, 1, 1.2 and 1.6 mm.
Working Capacity (24Houre,300 Days):
It is necessary to ask the seller for the exact number of the output and they should include this number in the contract.
Price:
The price of the production line can be divided into 3 classes. The price difference in each of these classes is due to their difference in the output efficiency, the life of consumable parts, frequency of line stops, and the robotic nature of the parts. Also, the history of that company and the number of machines it has sold have a significant effect on the price.
Power Supply:
Imagine that you have chosen the production line and during the contract, the seller inform you about the require electricity, water, gas and other equipment needed. This is wrong. You must obtain this information during negotiations and before signing a contract.
In fact, first, based on the needs of the production lines, all the necessary requirements for the construction of the factory are designed and then the production line is purchased.
The best consultant for you is the line seller itself, who can advise you on the construction and equipment of the factory based on its experience. In this case, the percentage of error will be reduced.
Installation and Debugging:
It is necessary for the seller of the product line to have a clear explanation in the contract regarding how to install and operate and train the buyer’s personnel. It is also necessary for the seller to respond to solving problems if they occur.
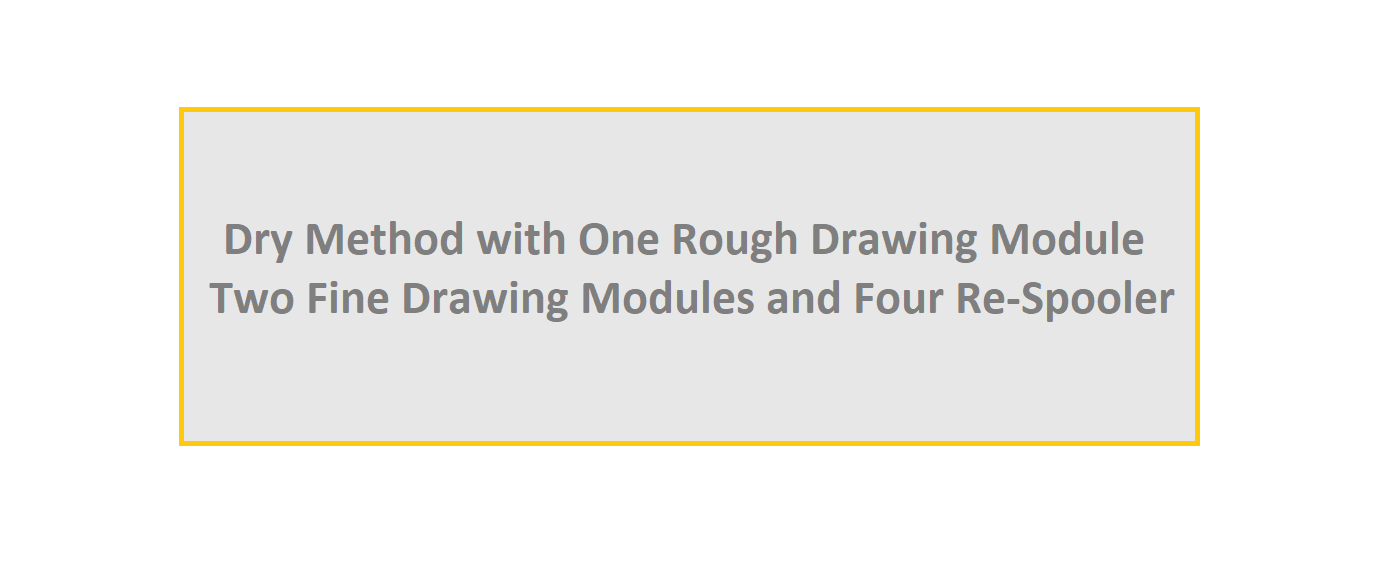
As mentioned, this production line has one Rough module, two Fine modules and 4 Rewinder. We consider the output of the stages in the form of a funnel. According to this funnel, there are 9 tons of semi-finished products in the Rough stage, in which the diameter of the wire has reached 6.5 to 2 mm. In the Fine stage, the output from diameter 2 to 1.2 or 1 or 0.8 mm is equal to 13 tons.
Finally, the output of 4 Rewinder will be 15.3 tons in 12 hour shift.
It should be noted that it is possible to increase the number of modules based on the budget increase and consequently increase the output.
Designed Production Line
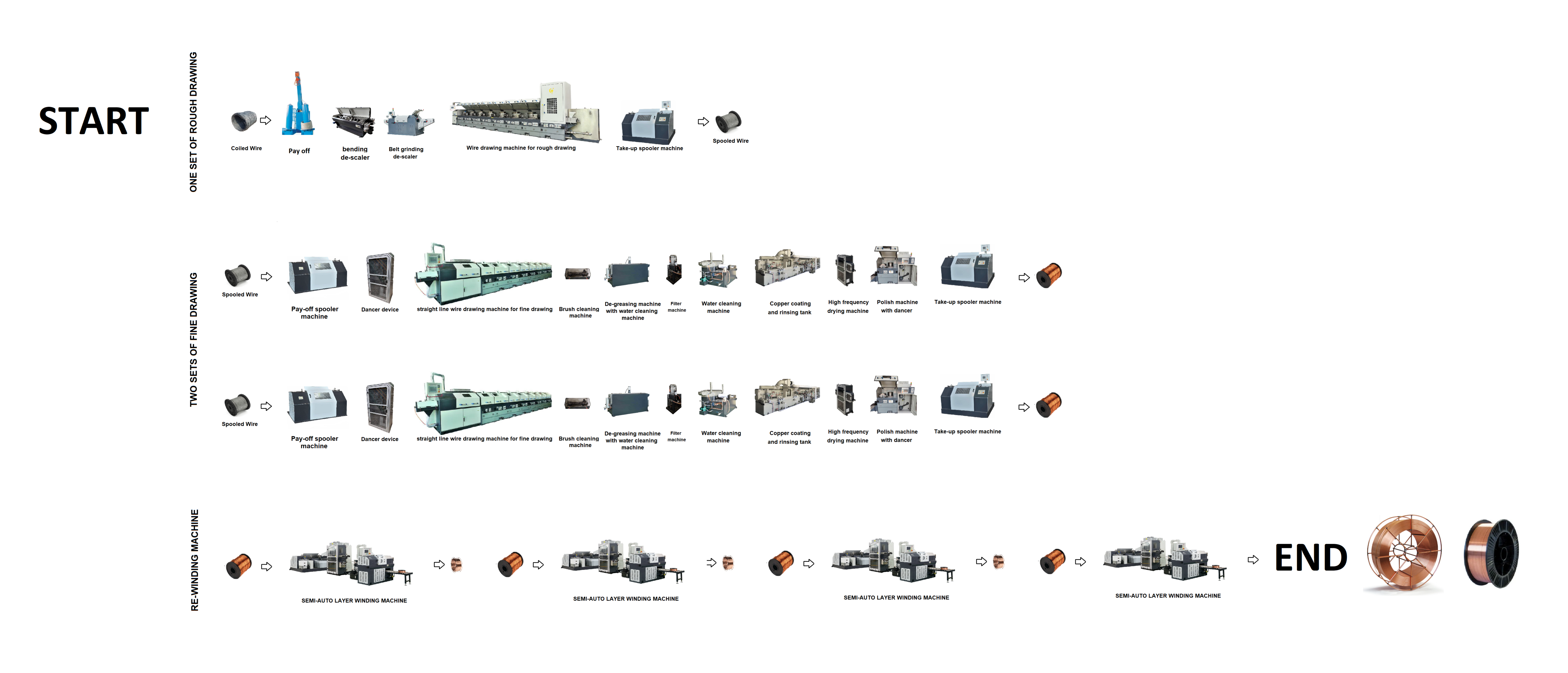
Production Funnel
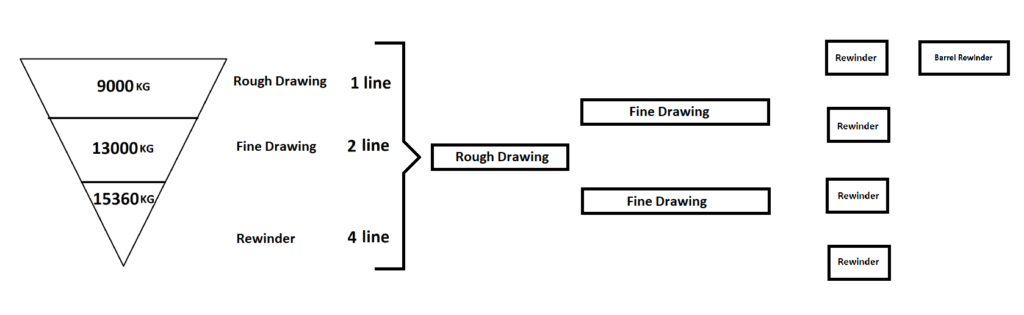
Rough Drawing Module Overview
When talking about Rough Drawing, Commonly it means reducing the diameter of the wire from 5.5 or 6.5 mm to 2 mm. At this stage, Initial cleaning of the wire will also happen. The output of this line is spooled drawn wire on big reel.This module contains units as follows:
Rough Drawing Module as part of a full set of Wire Drawing Manufacturing Line
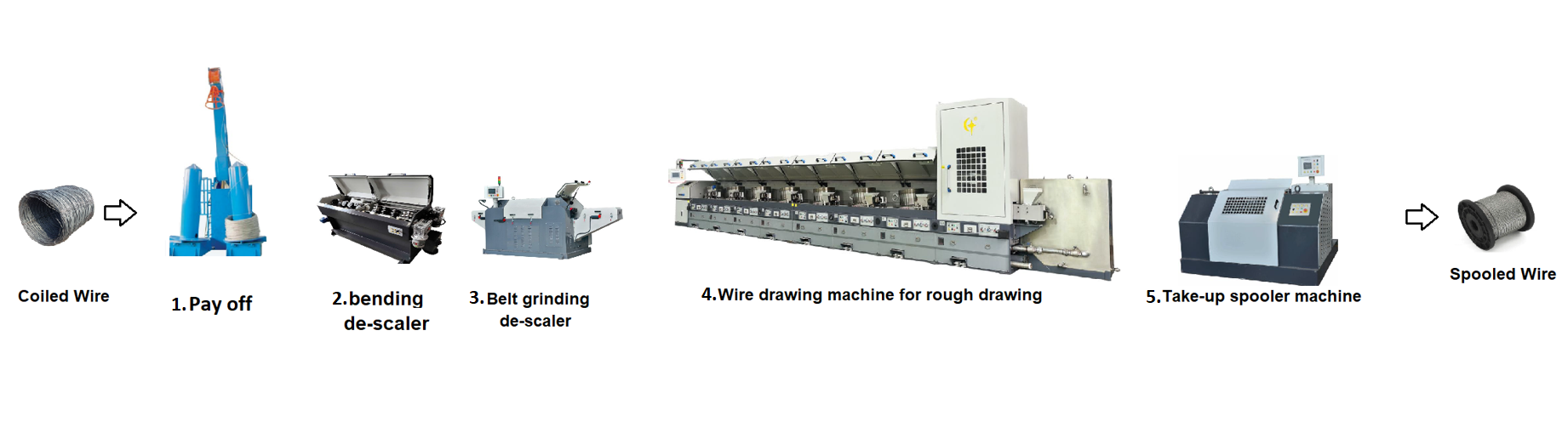
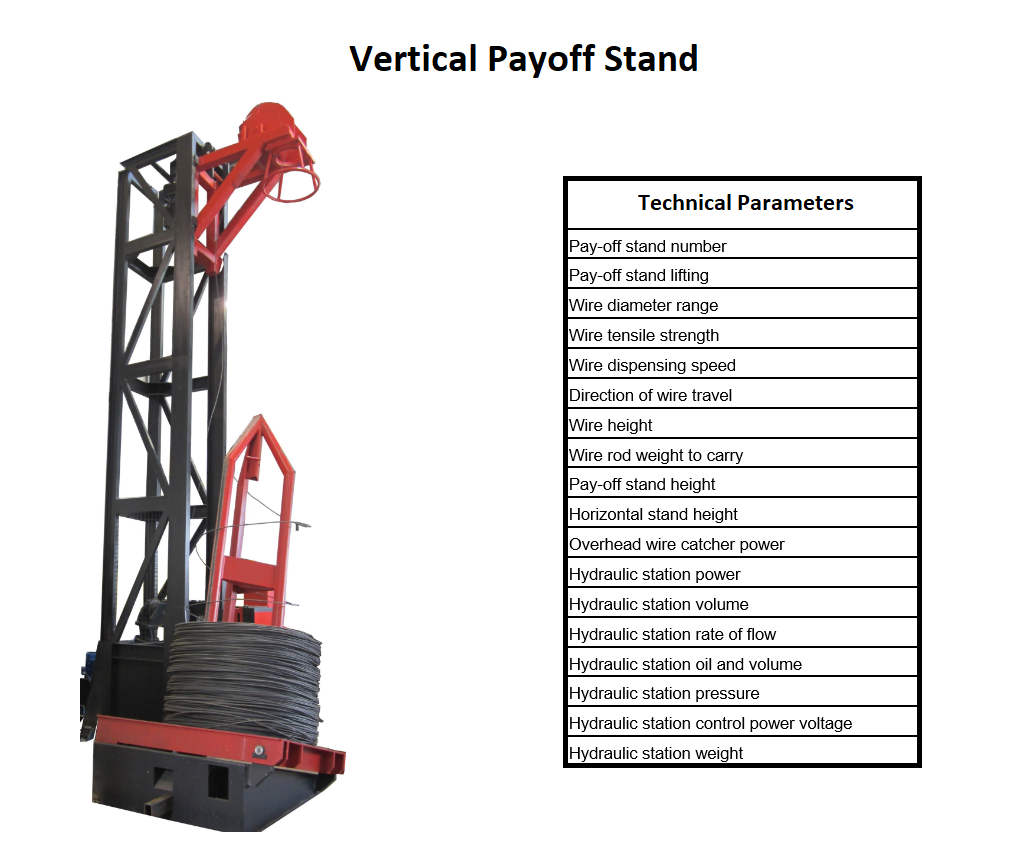
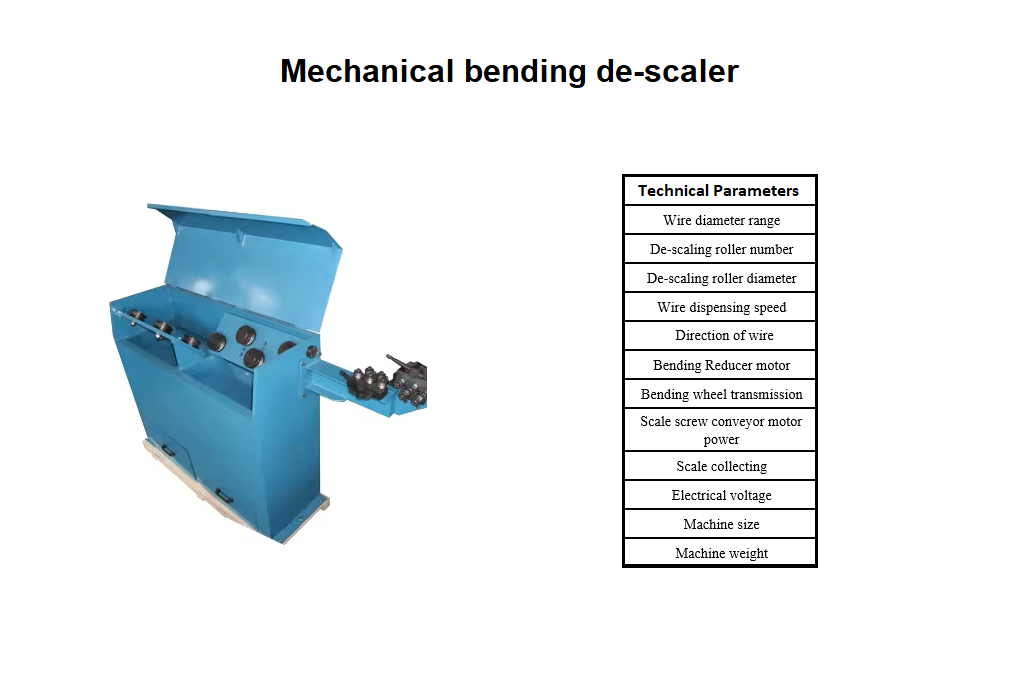
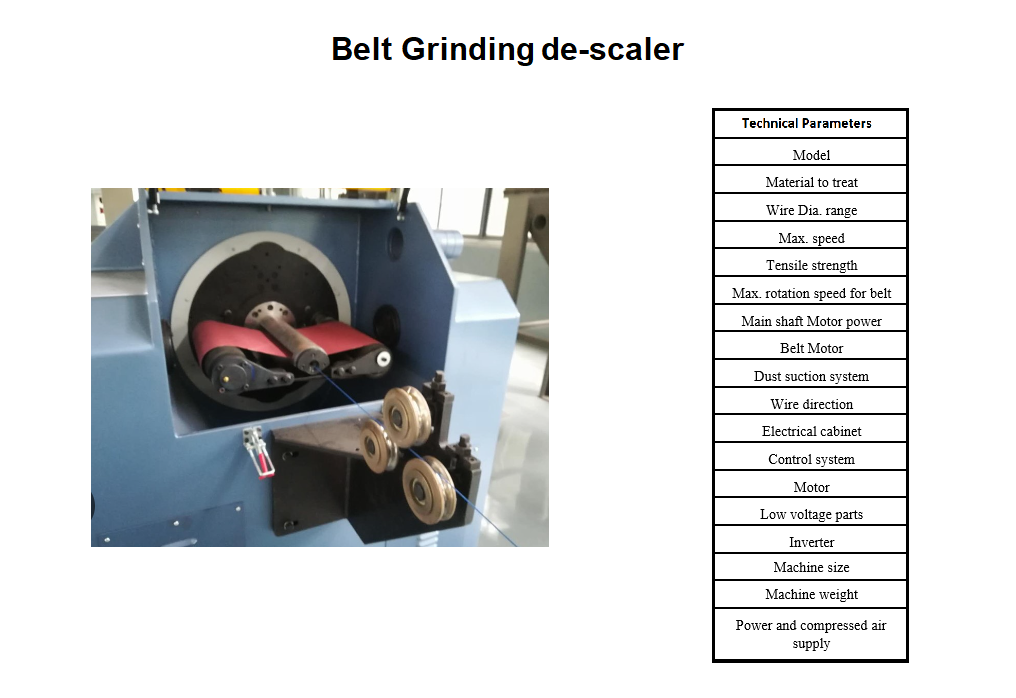
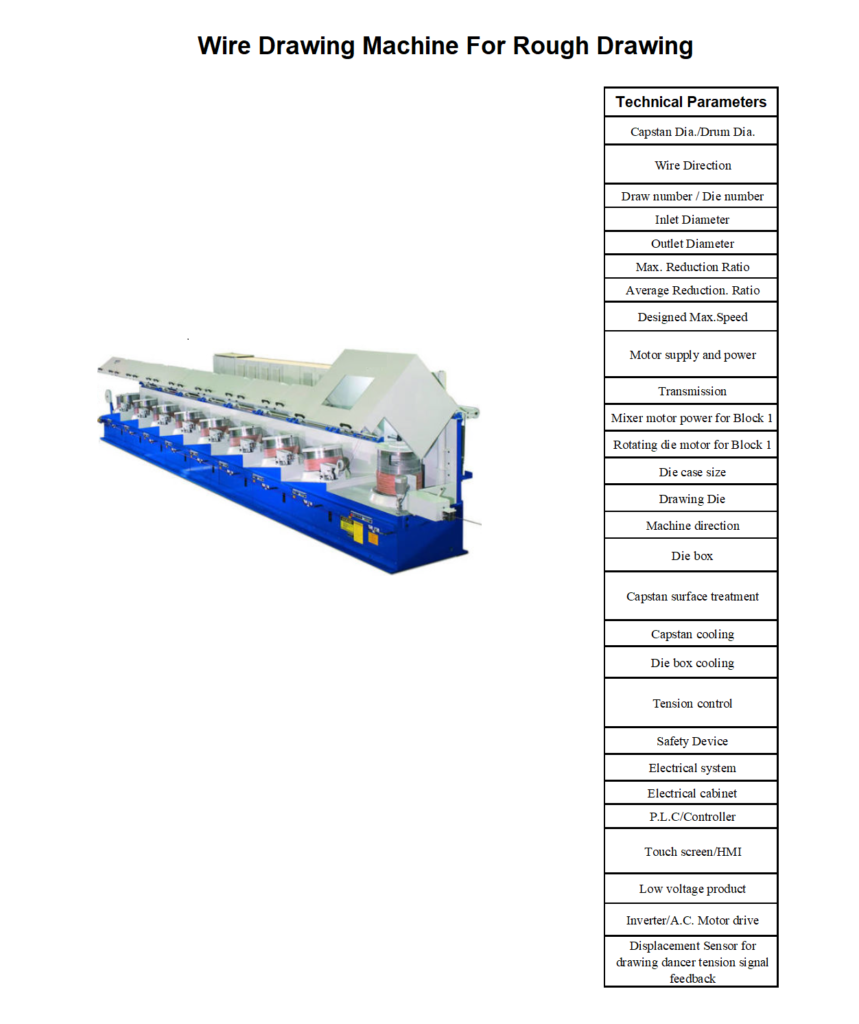
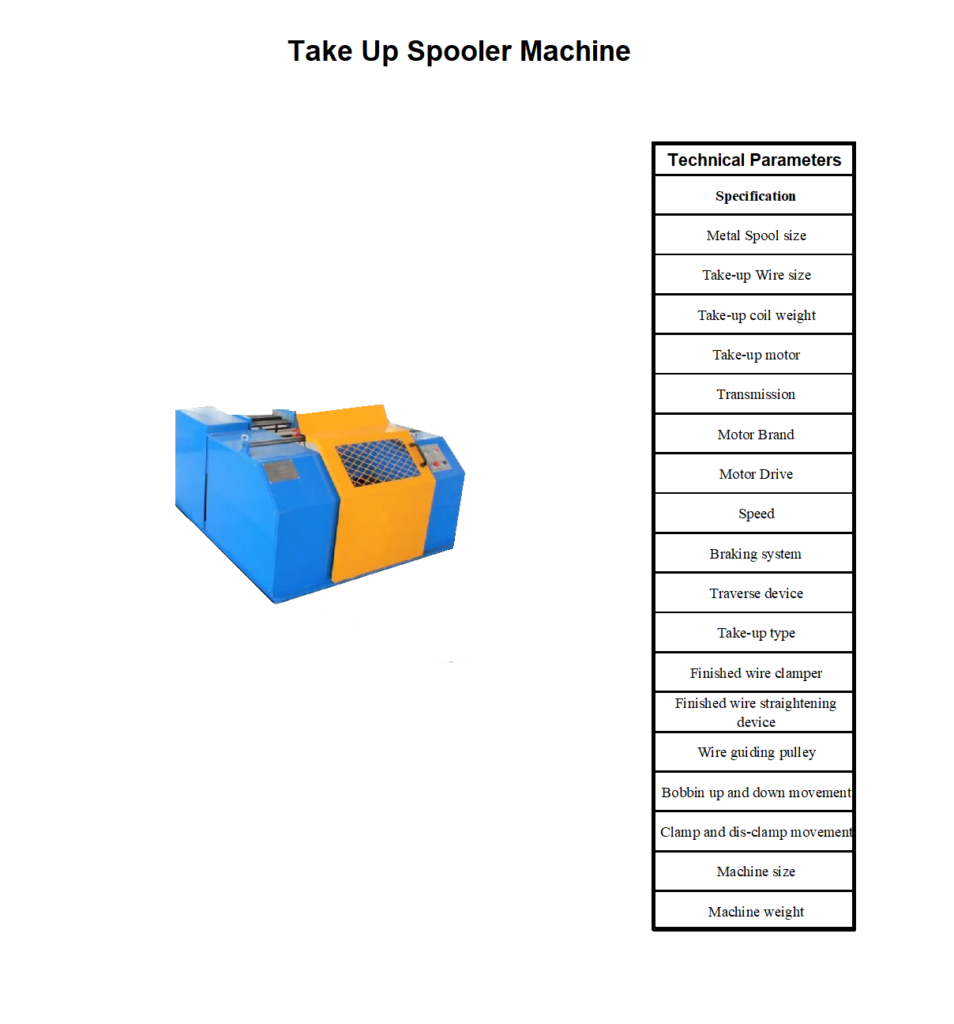
Fine Drawing Module Overview
In the stage of fine drawing, the diameter of the wire reaches from 2mm to 1.6 or 1.2 or 1 or 0.8 mm. In this process, copper plating will also be done on the surface of the wire. The output of the rough drawing stage in reels above 800 kg will be the input of the fine drawing. This module includes the following equipment:
Introduction of Quality Parameters of Fine Drawing Line Units:
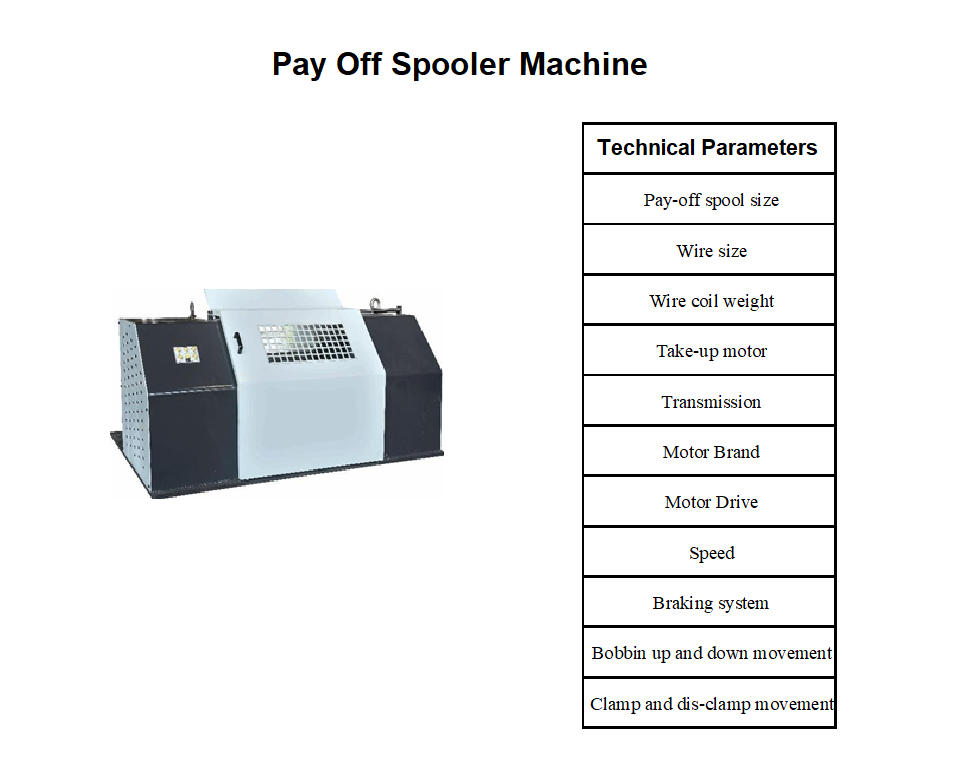
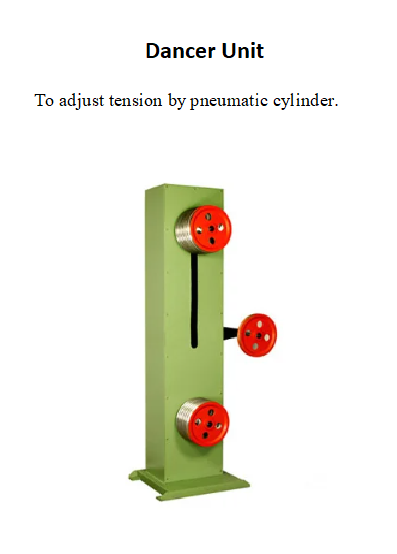
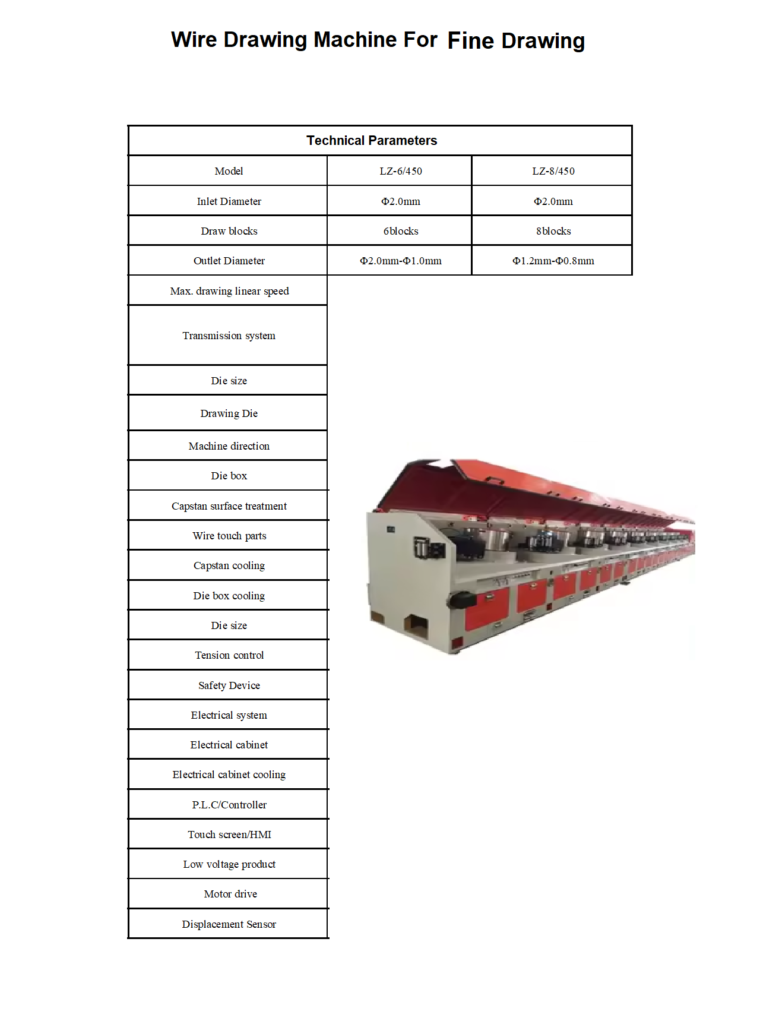
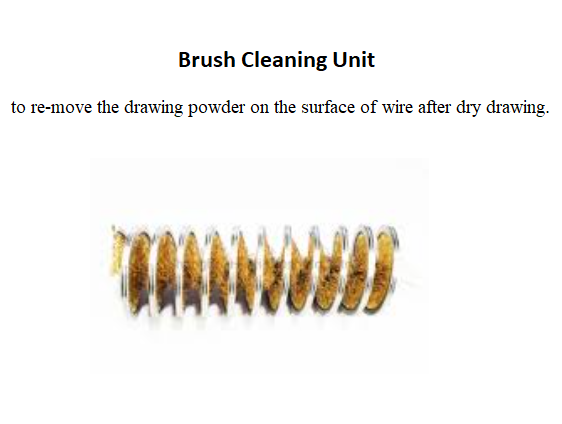
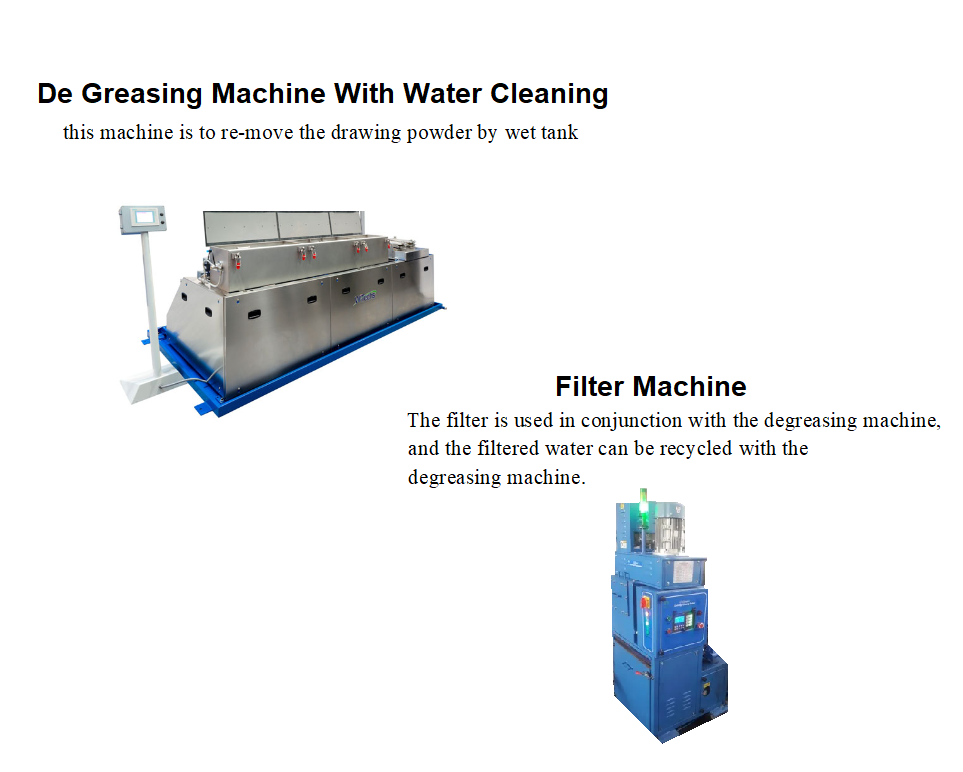
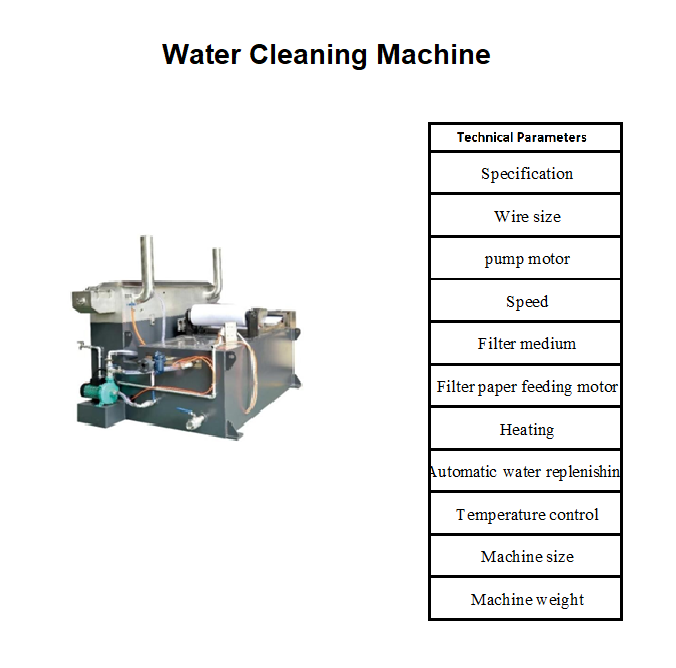
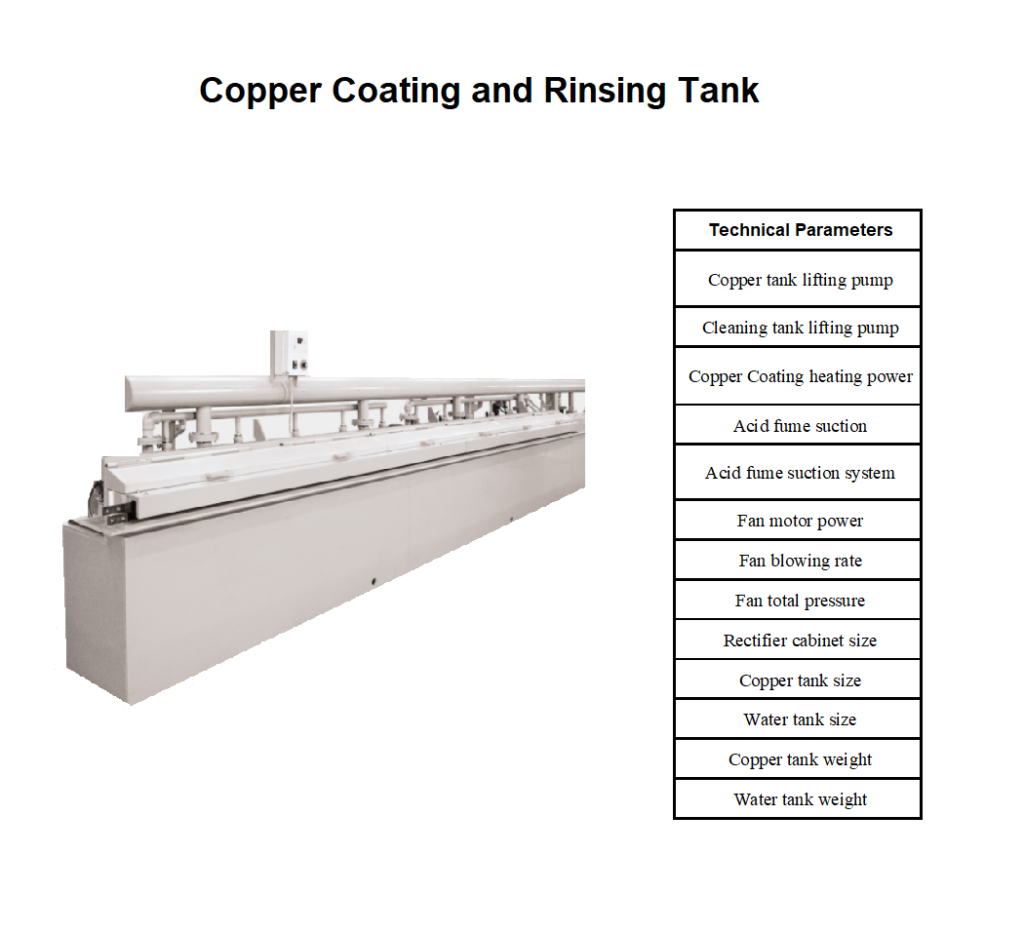
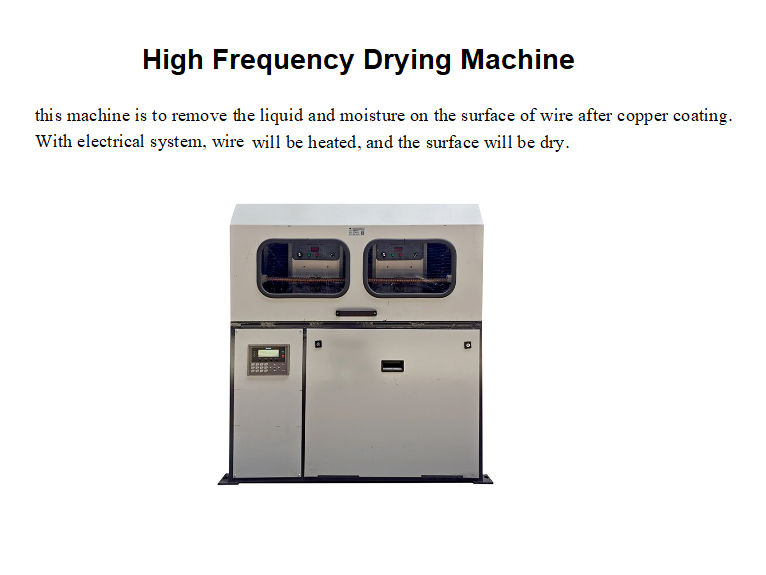
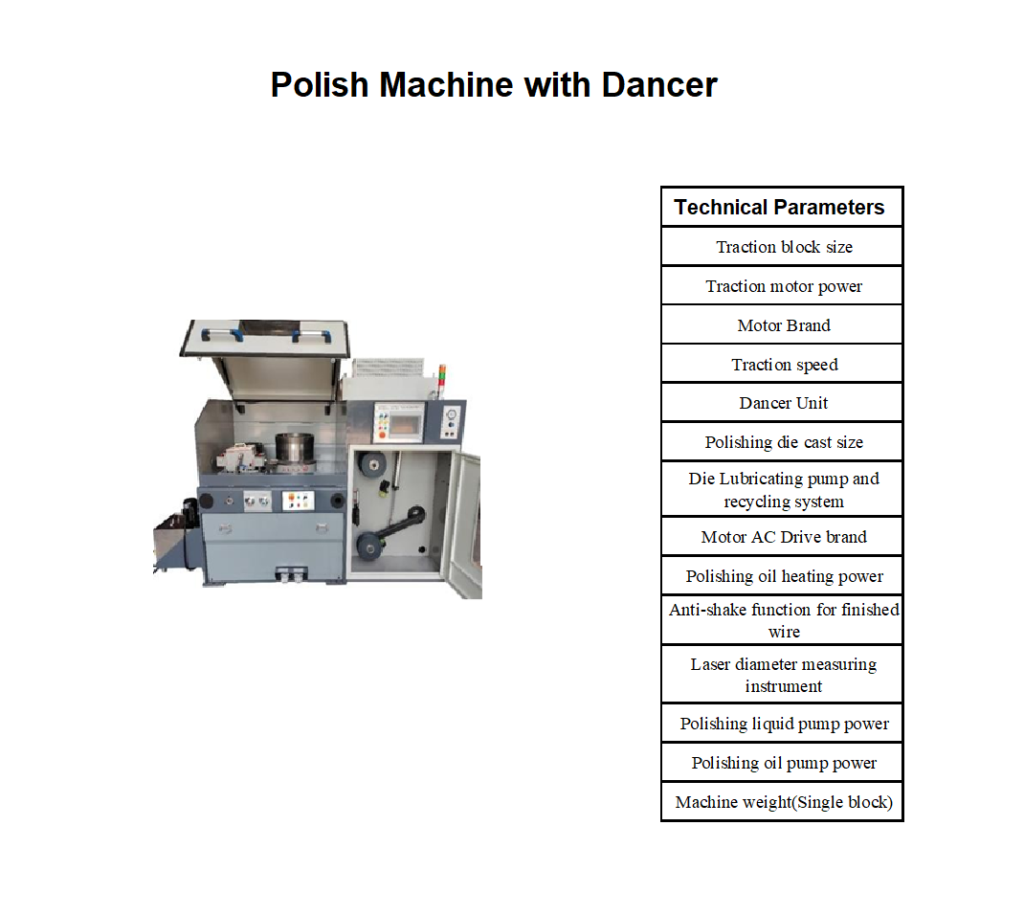
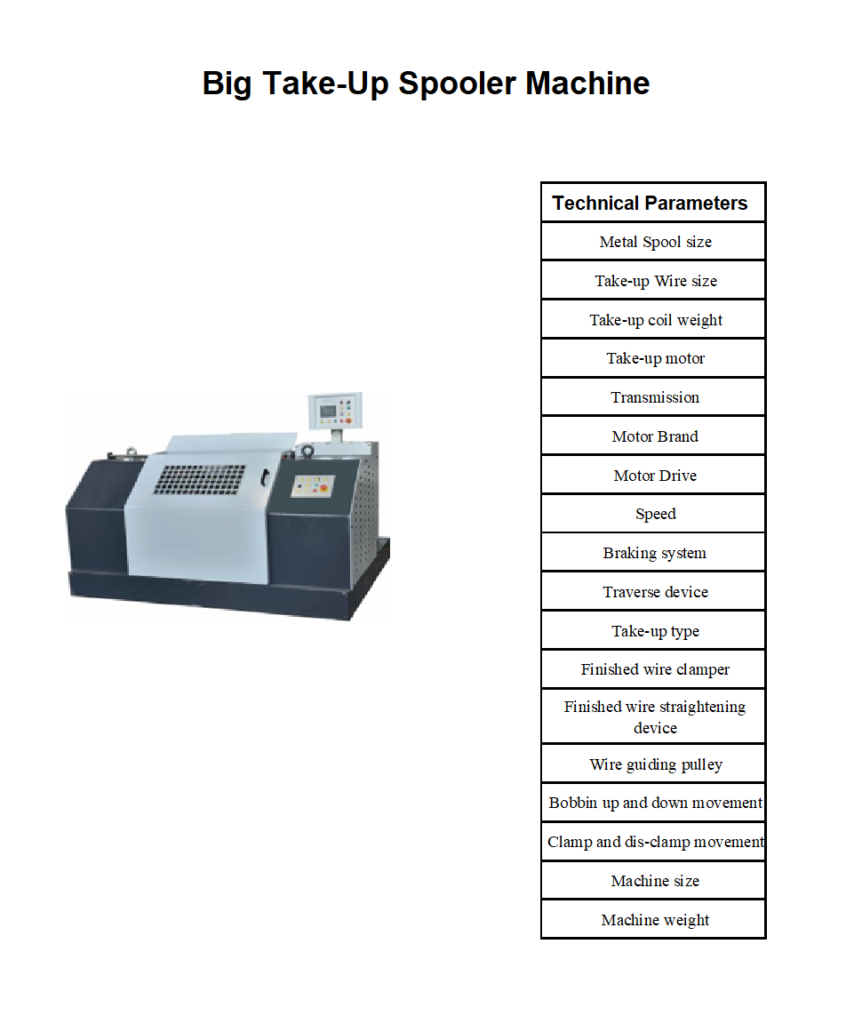
ReWinder Module Overview
The final Re-Spooler machine are responsible for transferring the wires wrapped in large reels to the final 15-17 kilo plastic or metal spools. This unit is available in two models, automatic and normal. This unit consists of three parts: Payoff-Dancer-Take up.
It is also possible to deliver welding wire in drums over 50 kilos by another type of packing machine, which requires a different unit for this.
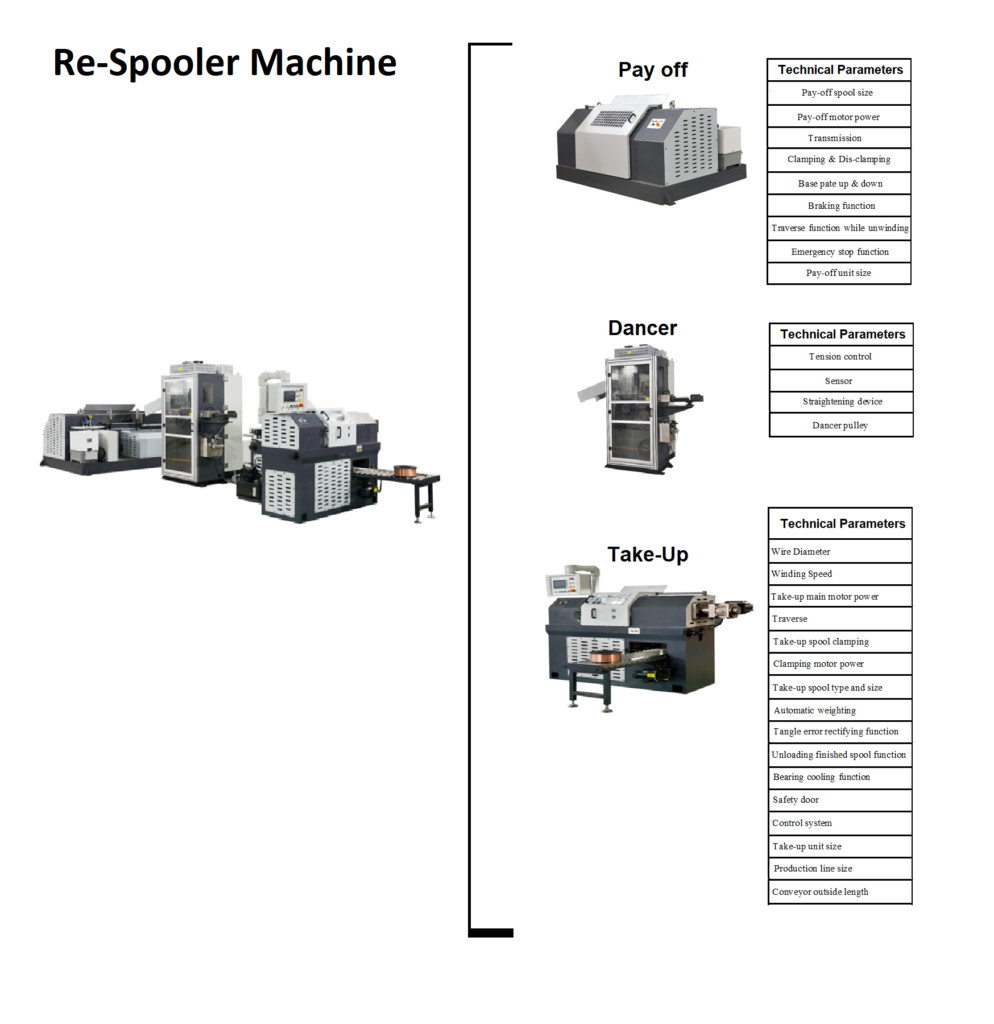
The Picture of the Processing Steps
Wire Processing to the Final Product
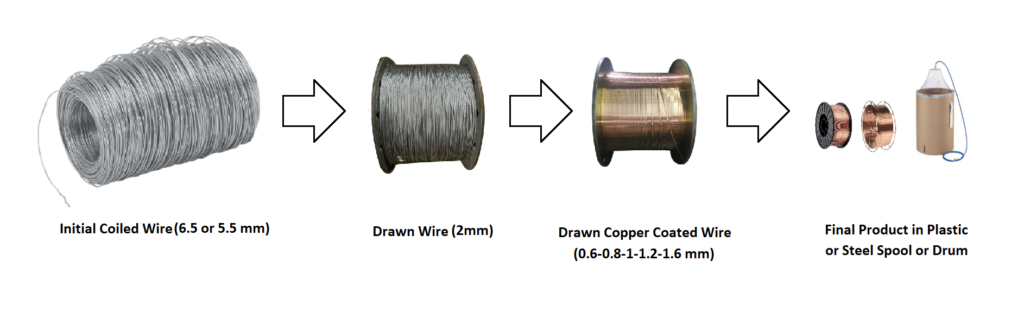
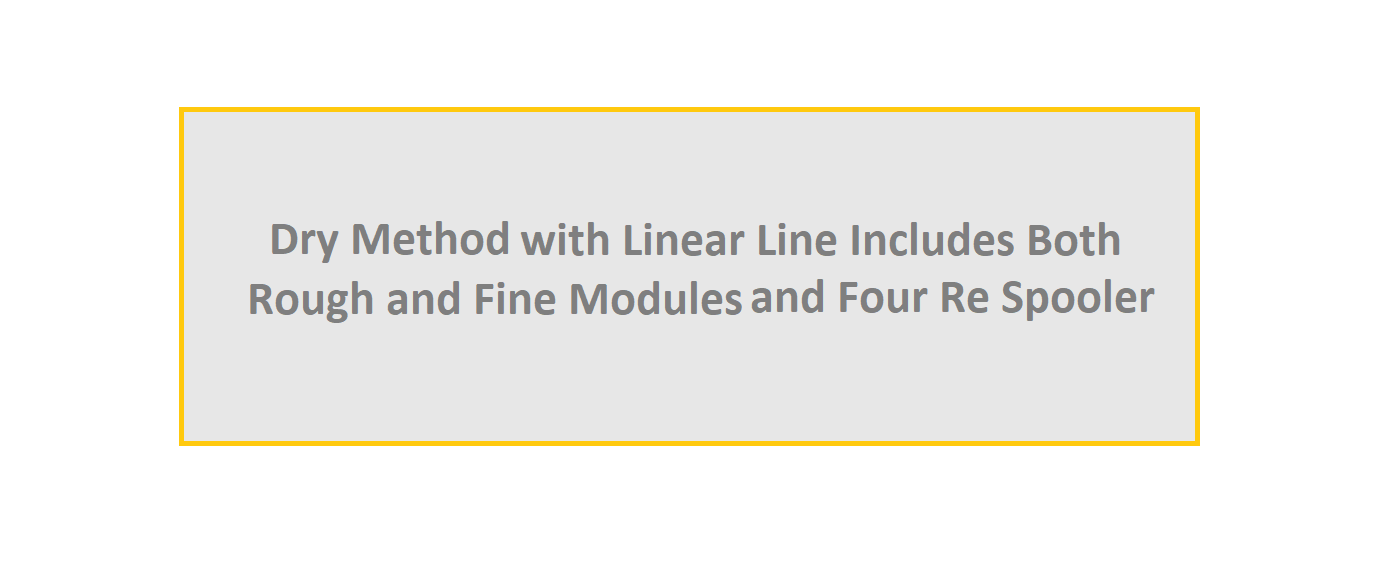
Designed Production Line
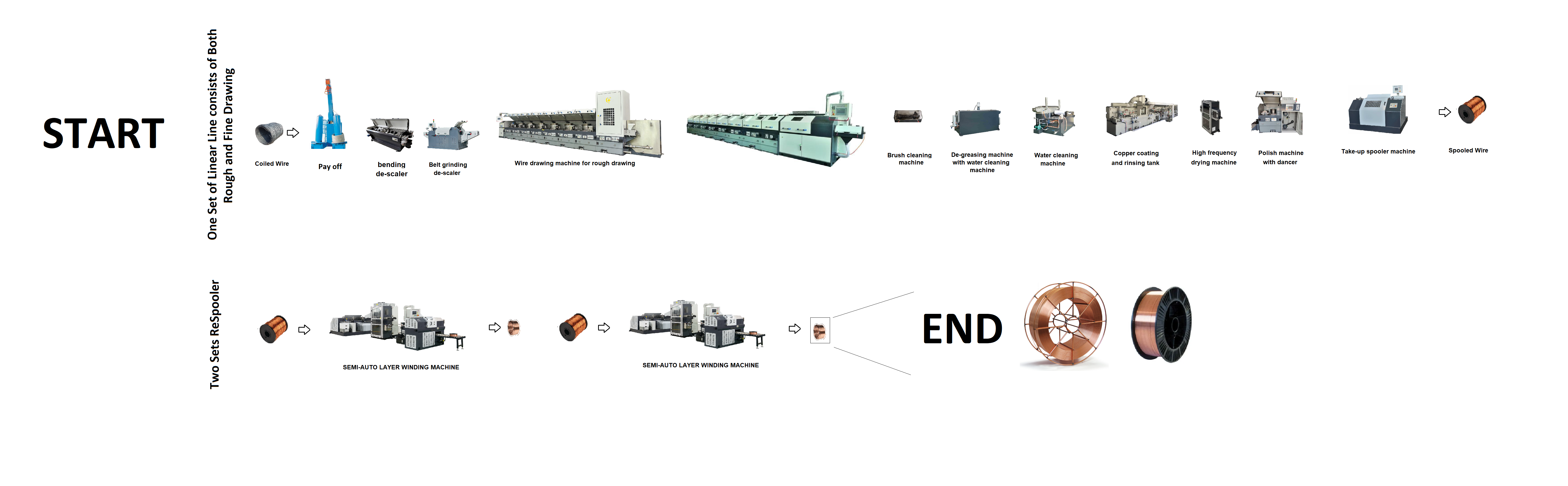
Production Funnel
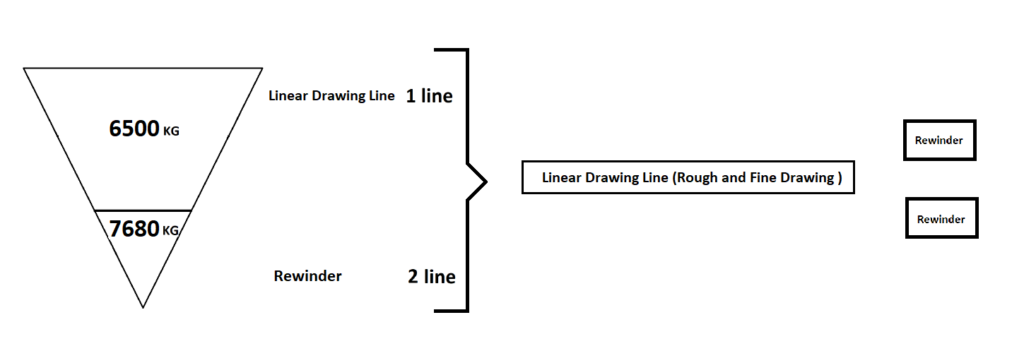
The Picture of the Processing Steps
Wire Processing to the Final Product
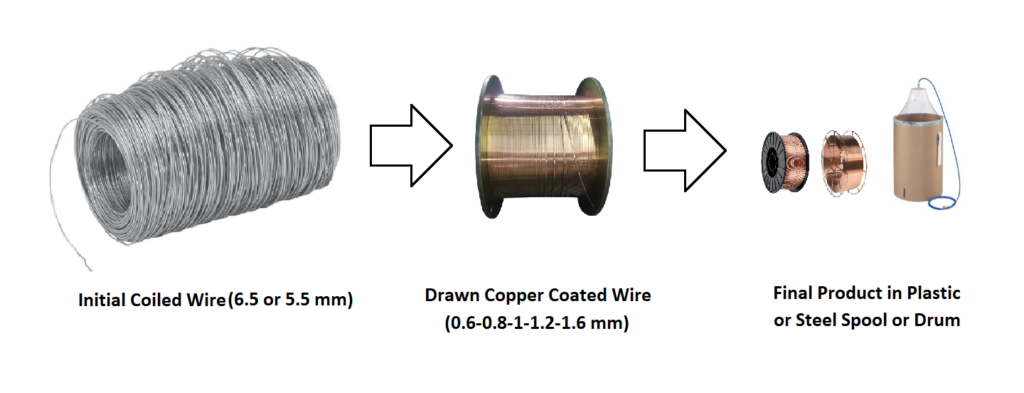
Know-More
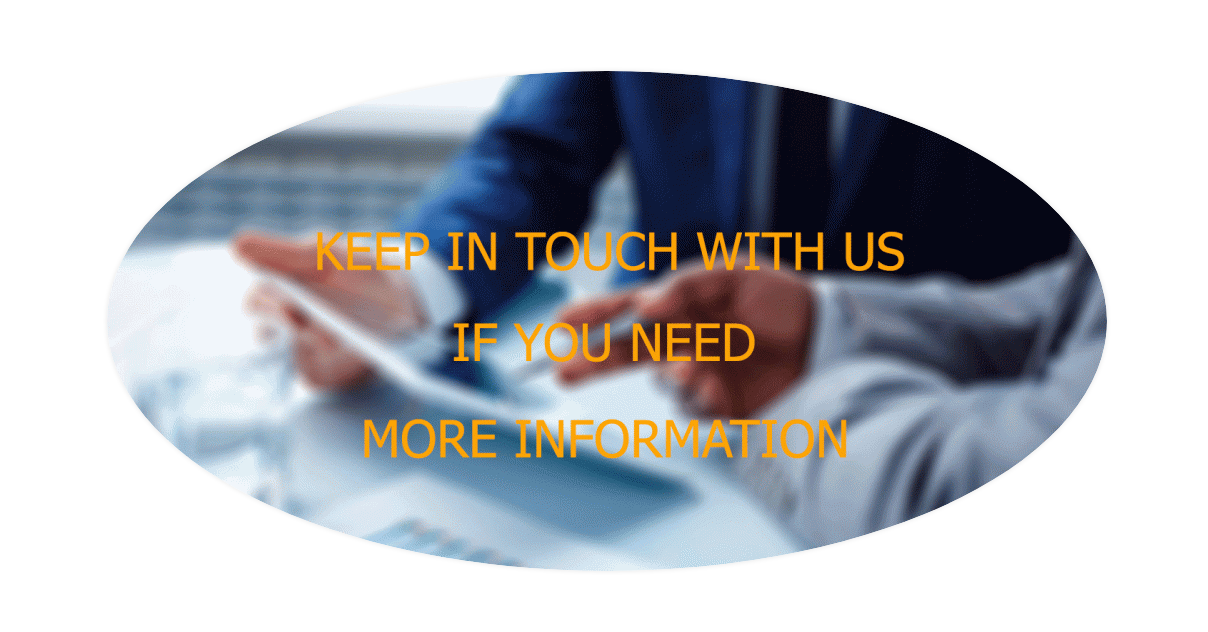