Shielding Gas Formers
Slag Formers
Slag Modifiers
Slag Detachability Modifier
Arc Stabilizers
Deposition Rate Augmenters
Deoxidizers
Fluxing Agents
Binding and Slipping Agents
Hydrogen Controlling Agents
Alloying Agents
Introduction
Material Used in Flux of Welding Consumables
The raw materials used in the welding consumables manufacturing process are divided into four major categories:
- Chemical powders
- Mineral powders
- Metal powders
- Feroalloy powders
An example of the powders classified in this group is shown in the (figure N10 and O10).
The raw materials used in the production of welding consumables are divided into different categories according to their nature, production, and processing methods. In general, the input of raw materials in welding consumables is in powder form, but many of these materials have come a long way before reaching the factory.
Tests to confirm the quality of these materials include chemical analysis, granulation analysis, densitometry, hygrometry, etc. The spec sheet of each material specifies the tests required for each of them.
FIG O10
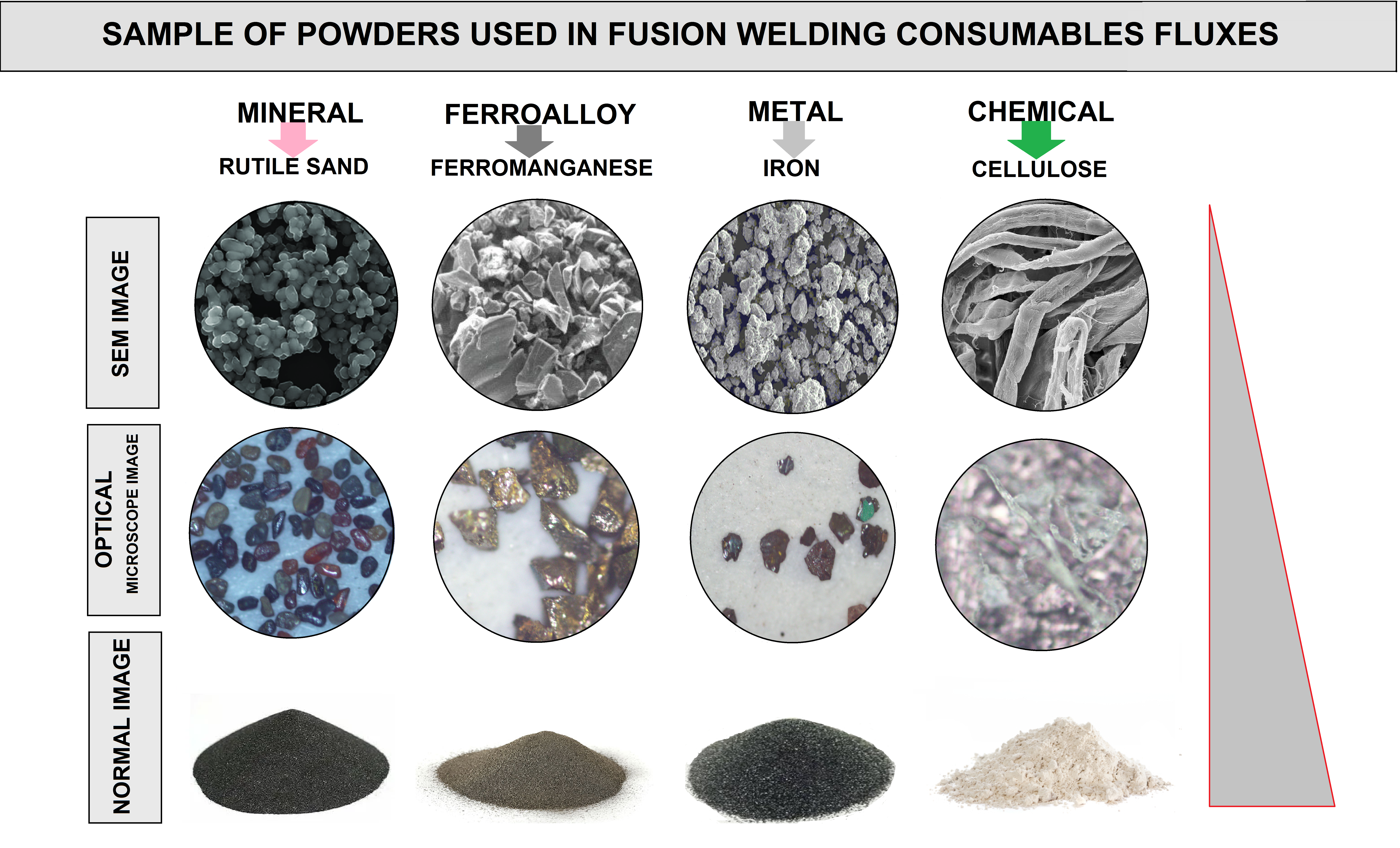
Function of Ingredients in Flux
In (figure A10) you can see the sample of classification for raw materials used in fusion welding consumables.
FIG A10
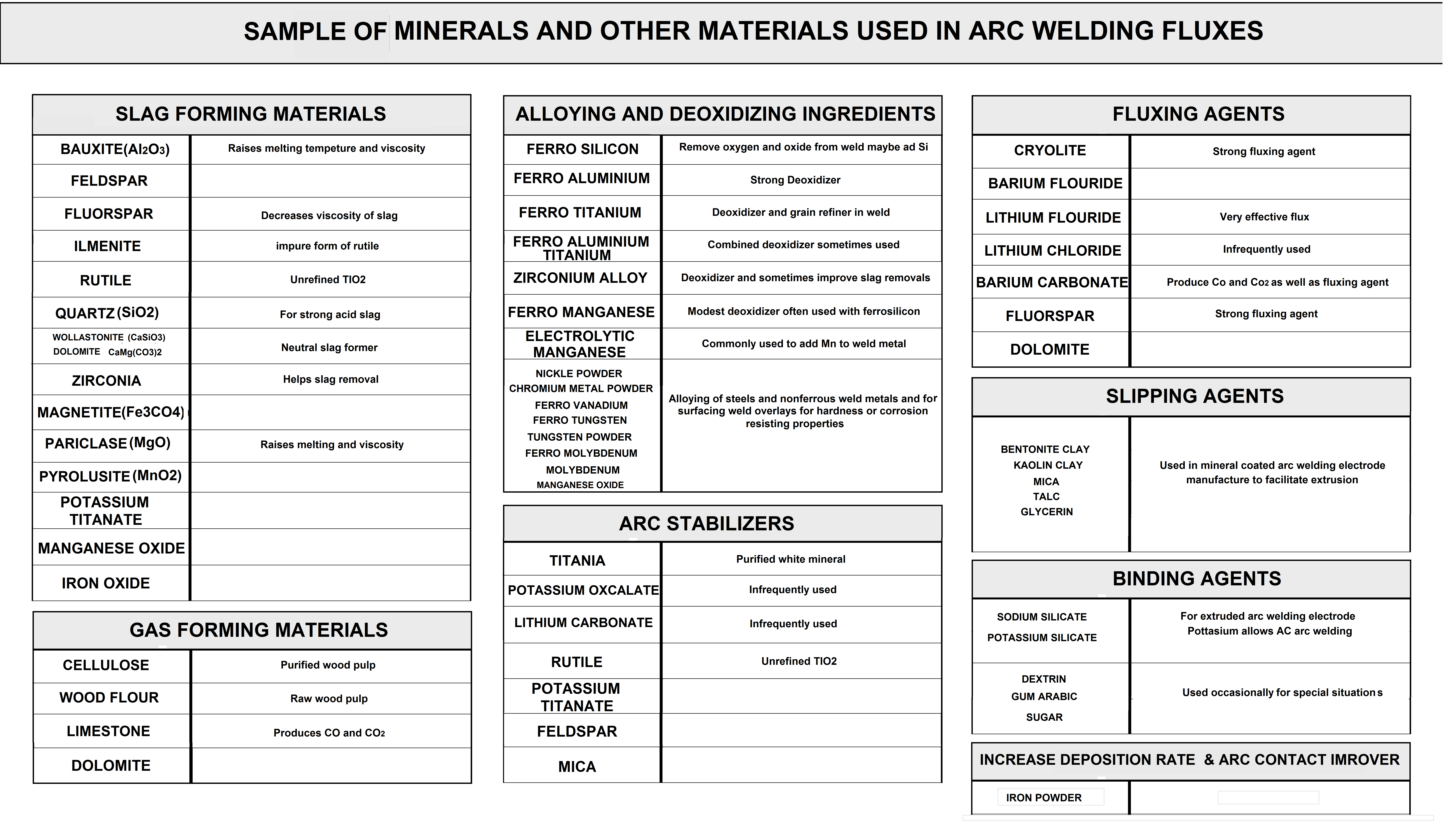
Shielding Gas Formers:
The task of this group of raw materials is to create protective gases of melt pool.During welding, the flux material decomposes and produces fumes. These fumes shield the molten weld pool from the atmosphere. In the absence of those fumes, molten weld pool will directly come in the contact of atmosphere and may react with the oxygen present in the environment and thus oxidation will take place, which is very dangerous and may lead to failure.
The most commonly used minerals providing gases protection include calcite, supplied with limestone, having a chemical formula of CaCO₃. The thermal decomposition of CaCO₃ takes place at 950°C, leading to the formation of CaO and CO₂, which, in turn decomposes (in arc plasma) into carbon monoxide and atomic oxygen in accordance with the reactions (figure D10).
The reaction of carbonate decarburization is endothermic in nature. In this reaction, released CO₂ makes up 44% of the total calcite mass. The transport of CO₂ takes place as a result of Knudsen diffusion through voids and cracks between phases and through spaces formed due to the separation of CaO crystals from CaCO₃ not yet decomposed.
latest research examined the effect of calcium carbonate content in the phase composition of a low-hydrogen coating mixture on the content of hydrogen diffusing in a weld metal, with calcite content in the mixture varying between 10% and 24%.
Tests revealed a decreasing amount of hydrogen in a weld for mixtures containing up to 18% of CaCO₃. Greater CaCO₃ amounts produced the opposite effect.
While preparing coating mixtures it is also possible to use a number of other carbonates (figure D10), yet they are used to a less degree. As can be seen in figure, the mineral releasing the greatest amount of CO₂ is magnesite , whilst iron carbonate (siderite) decomposes releasing the smallest amount of the above mentioned gaseous compound. It should be emphasized that among all basic oxides it is calcium oxide that has the greatest ability to absorb and fix water in the structure, hence its excellent capability of reducing hydrogen and oxygen contents in a molten metal area. The ability of magnesium oxide to react with water is significantly inferior if compared with that of CaO, which is additionally responsible for the predominant popularity of calcium carbonate .
The thermal decomposition of magnesite and that of siderite are similar, in accordance with the reaction. In turn, dolomite decomposes in a two-stage reaction. During the first stage, at a temperature of 700-750°C, reaction products are CaCO₃, MgO and CO₂. The second stage takes place at a temperature of 900-1000°C and leads to the decomposition of CaCO₃ into CaO and CO₂ .It should be mentioned that the greater the carbonate fraction, the higher the basicity of slag and the lower the hydrogen content in a weld .This is due to a greater tendency to fix water in a structure through the absorption of hydrogen from arc plasma, which prevents the hydrogen from entering a liquid metal.
FIG D10
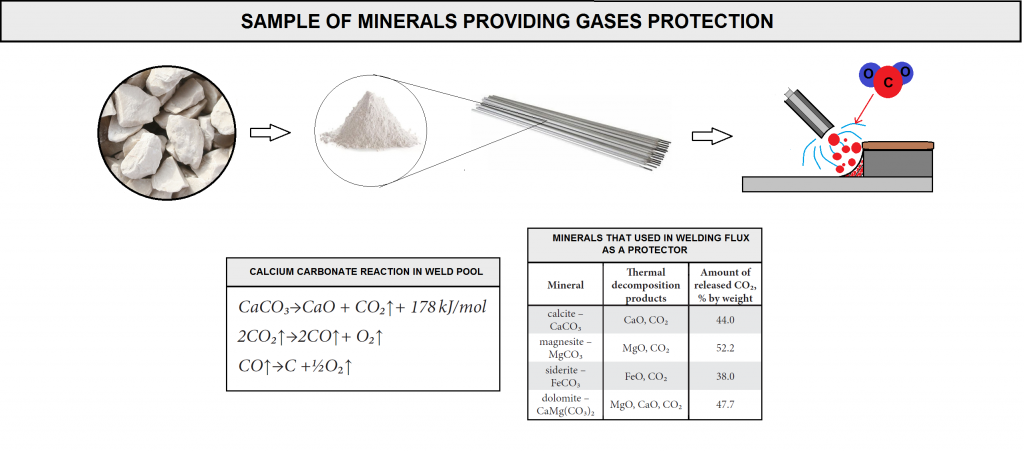
Slag Formers:
the slag is a combination of glass and crystalline phases that should remain molten throughout the time that the weld pool is in a liquid state. Practical guidelines recommend a melting temperature that is around 200c below the melting temperature of the weld metal to protect the molten pool from atmospheric contamination. the density of the slag must be much lower than that of the molten weld metal in order to float above the molten weld pool and reduce slag entrapment in the weld metal.
based on the chemical reactions between molten and slag, the raw materials used in the flux will decompose due to the heat generated by the electric arc, and part of it is transferred to the slag and leads to the formation of slag (FIG G10).
The density of flux material is less than the weld material hence the flux comes upwards and floats on the weld pool and hence protects the weld pool. During solidification, flux material also solidifies and forms a thin layer on the surface of weld called as slag. This thin layer of slag helps in slow cooling of weld material. In the absence of thin layer of slag, rapid cooling of molten weld pool will happen and it is very harmful because rapid cooling results in microstructural changes of weld metal (martensite formation) so the existence of slag formers in flux covering is very important (figure E10).
There are three main types of slag forming raw materials in welding electrode :
Basic oxide,acidic oxide and amphoteric oxides . these oxides determine slag properties such as melting temperature ,thermal expansion,density, electrical conductivity,thermal conductivity,and viscosity.
basic oxides such as CaO ,MgO ,Na2O and K2O tend to decrease the viscosity of the slag since they break silica networks. Silicates are acidic oxides that function primarily as slag formers ,i.e.
As mentioned ,Fluxes and flux formulations are generally referred to as acid, basic, or neutral. acid fluxes (e.g., silica) generally form acids in water; basic fluxes (calcium carbonate and lime) form bases in water; and fluorspar, or calcium fluoride, is a neutral substance because it is the reaction product of a base and an acid.
Alumina (Al2O3) and titania (TiO2) are other network formers that produce the chain structure of the slag. they are classified as amphoteric oxides for they can act either as an acid or base depending on the surrounding medium ,i.e. the make of the flux composition. FeO and MnO are also considered as amphoteric oxides.
FIG G10
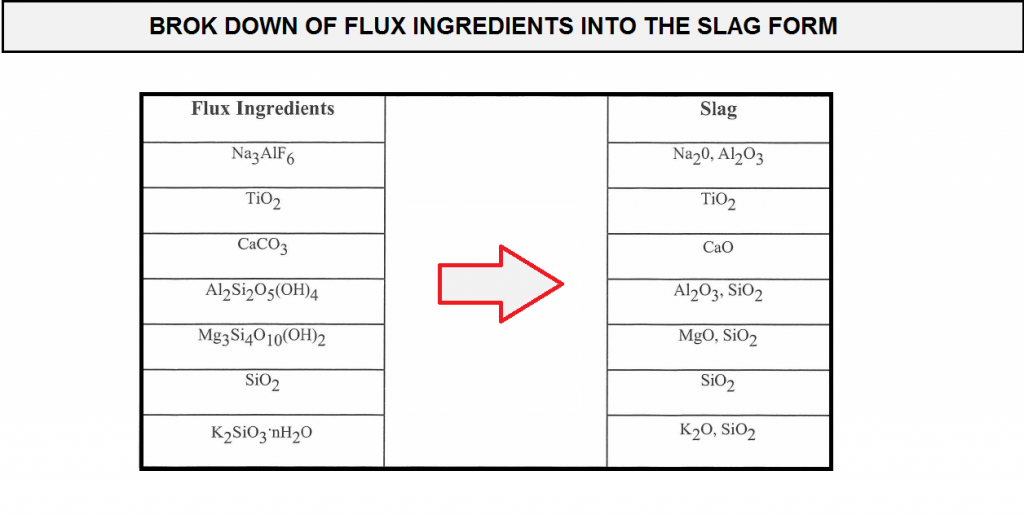
FIG E10
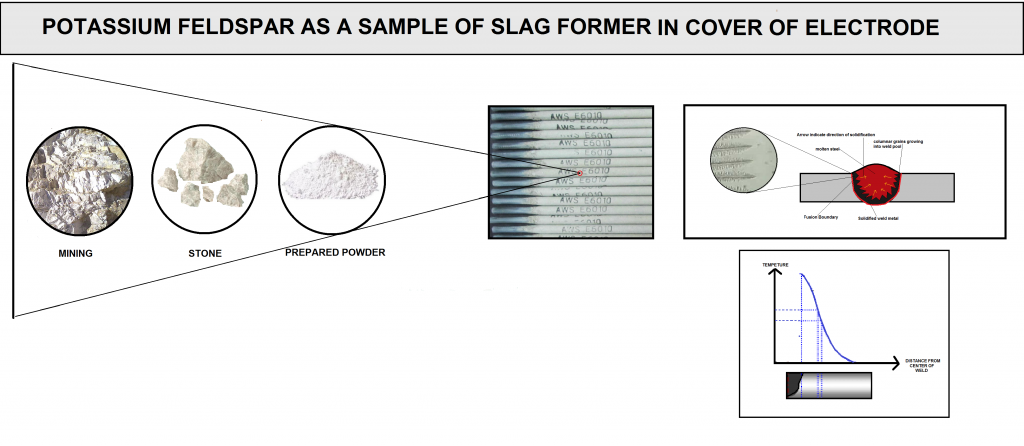
Most Important Slag Former Components
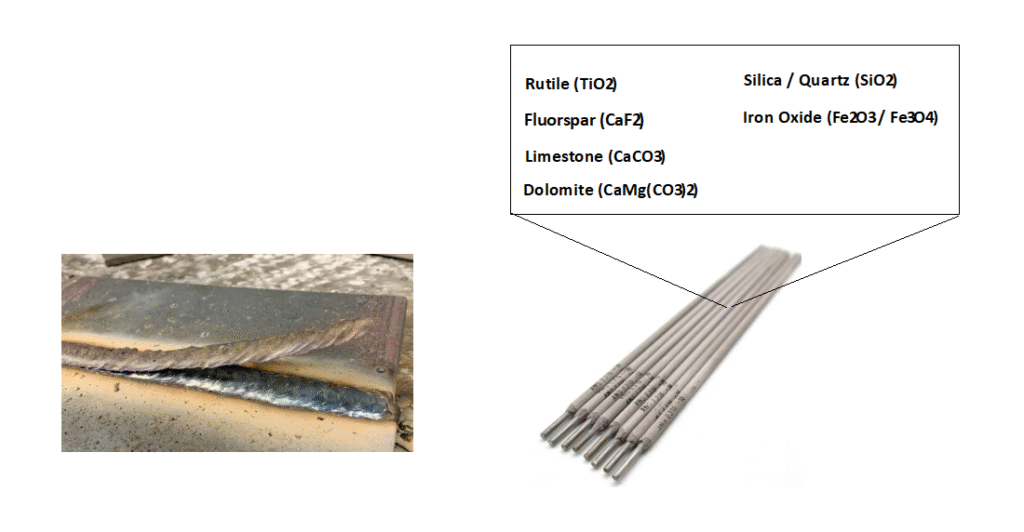
Slag Modifiers:
They are the raw materials in minerals type that control the physical properties of the slag (melting point, freezing range, conductivity, wettability, fluidity).The slag viscosity must be adequate in the weld metal melting temperature range to fully protect and cover weld pool during welding . slag viscosity is important item .because sufficient slag viscosity will not allow atmospheric gases to enter the molten weld pool and inhibit the slag from flowing away from the molten weld metal . networks of silicates ,aluminates , and titantes all posses high –valence cations that construct the bonding network to enhance glass formation in the slag. Silicates can create very good glass bonding networks but produce high oxygen weld metal content since every silicon atom found in the center of the SiO4 tetrahedrons is surrounded by four oxygen atoms. When the slag is too fluid , the network of silicate tetrahedrons possess broken bonds between the silicon. Aluminate and titanates are more grid and stable slags with higher viscosity and decreased weld metal oxygen content.Fluoride are known to decrease the viscosity of the slag by ionizing and breaking down the silica networks.
Slag Detachability Modifier:
slag detachability is of great concern because it influences the integrity of multi-pass weldments and affects process economics because of the potential of rework. Rutile (TiO2) containing fluxes generally produce slags that exhibit good detachability . basic flux system typically exhibit less than describe wetting and more abrupt angles. Consequently , complete slag removal may be more difficult in these regions .slag removal has also been documented as more difficult when the flux coating contains fluorides. Slags that include the spinel (AO.B2O3) and cordierite (Mg2Al4Si5O18) glass structure have also been deemed very difficult to detach from the weld metal . an increase in alumina content in the flux composition has shown improved slag detachability .
another important factor to consider for slag detachability is the difference in coefficient in thermal expansion between the slag and the weld metal deposit.
It is desirable to have a temperature coefficient of thermal expansion slightly different from the weld metal . an adequate amount of difference in the coefficient of thermal expansion is necessary for good slag detachability but slag detachability that is too rapid may present undesired heavy temper colors.
The presence of calcium fluoride is responsible for the difficult separation of slag, similarly as in the case of cordierite – Mg₂Al₃[AlSi₅O₁₈] and the solid solution of spinel (Mg, Mn, Cr) O∙(Al, Cr, Mn)₂O₃. Slag behaves otherwise in cases of increased amounts of SiO₂, Al₂O₃ and Cr₂TiO₂, the presence of which facilitates the separation of slag.
Arc Stabilizers:
The addition of these raw materials in the flux coating help stabilize the arc by continuously producing ions and emitting electrons to form an electrically conductive passage. For example Potassium silicates acts predominately as the binder in the flux coating , it plays a critical role in the stabilization of the arc in AC applications because potassium ionizes at lower energy ,4.3 eV. Sodium ionizes at 5.1 eV and is therefore more readily used as the binder for arc stabilizer of DC applications where the ability to re-establish the welding arc is not as vital. The addition of fluorides typically produces a more erratic arc, despite its ability to remove surface oxides from the join region.
Deposition Rate Augmenters:
metallic additions that increase the rate of deposition of the weld metal. for example The addition of fine iron (Fe) enables faster melting of the electrode, thus increasing welding process efficiency. Welding without this kind of additives requires greater power consumption, is responsible for a droplet-type liquid metal transport mode (more difficult to control) and leads to a greater number of spatters .
The chemical composition and the physico-chemical properties of a coating mixture, dependent on the raw material used, have a significant influence on the penetration depth . presence of pure CaCO₃, K₂CO₃ and CaF₂ causes shallow penetration, whereas Na₃CO₃, MnO₂, Al₂O₃, SiO2 and MgO lead to the obtainment of a medium depth of penetration. It has also been found that the presence of MgCO₃ in a coating mixture ensures the obtainment of deep penetration.
Deoxidizers:
etallic additions, including iron powder and ferroalloys, that are added to remove free or combined oxygen from the molten metal in the weld pool. ferroalloys supplied to a mixture in order to deoxidize a liquid metal in a weld. Ferromanganese (FeMn), ferrotitanium (FeTi) and ferrosilicon (FeSi) belong to the group of deoxidizing raw materials most commonly used for the preparation of coating mixtures and fluxes.
Fluxing Agents:
minerals those are active in the removal of impurities from the weld. For reactive metals, aggressive chemical compounds are often added to the flux to remove tenacious oxides from the weld joint .fluorides and chlorides are example of these compounds. Fluorides also decrease the viscosity of the slag .
Binding and Slipping Agents:
flux formulations contain raw materials that serve as binders and extrusion aids in the manufacture of coated welding rods or promote agglomeration and extrusion processes in the manufacture of granular SAW flux.in covered electrode , a binding agent is added to produce a wet mix , which is loaded into the extruder chamber ready for electrode extrusion. Binding agents are used to bind the flux ingredients together on the core rods. As many binders are water-base solutions , they are also a potential hydrogen source . some common low-hydrogen binders used are typically organic in nature such as sugar , dextrin , and gum Arabic .
The solutions of sodium and potassium silicates Ma(SiO₂)bO, where M=Na+ or K+) are used mainly as filler metals. This group of chemical compounds affects the centricity of a covered electrode, being a precondition for stable arc burning and proper weld formation, particularly while making root runs .
slipping agents are also added into the dry mix of the flux composition to ease extrude ability of electrodes . some common slipping agents used are glycerin, china clay , kaolin , talc ,bentonite , and mica.
For better strength of coating surface to prevent cracking The addition of carboxy methyl cellulose or cellulose (in low-hydrogen and rutile electrodes respectively) as a plasticizer prevents the excessively fast drying of a mixture, which could trigger the formation of cracks on a coating surface.
Hydrogen Controlling Agents:
The appropriate fluidity of molten slag and the reduction of diffusive hydrogen content are obtained by adding components containing fluoride ions . Calcium fluoride, CaF₂, is most commonly used in the production of coating mixtures and is provided in the form of fluorite (melting point 1418°C). As the low-hydrogen (basic) components of mixtures are characterized by a greater ability to fix water, CaF₂ is commonly used in the production of low-hydrogen (basic) electrodes. Tests conducted by scientists revealed that fluorine, F₂, reacts with hydrogen molecules forming hydrogen fluoride, HF, in accordance with the reaction:
Hydrogen fluoride does not dissolve in liquid iron and evaporates from an arc area .Sadly, calcium fluoride is not sufficiently active and its part enters slag. Therefore, it seems advisable to investigate the behavior of other fluorides. It has been found that calcium fluoride in the presence of silicon dioxide, SiO₂, reduces its oxidizing ability forming silicon fluoride, SiF₄, as can be seen in the reaction :
During submerged arc welding it is possible to observe the formation of a small amount of silicon fluoride which decreases the partial pressure of hydrogen. In addition, it has been found that the formation of SiF₄ does not reduce the content of silicon in a weld. Researchers noticed the reaction between calcium fluoride and aluminium oxide in slag, in accordance with the equation:

Fluorite is entirely included in the slag ratio, expressed by a basic component – acidic component ratio in accordance with the equation below ,describing the metallurgical behavior of a coating mixture and having a significant effect on the toughness of a weld .The higher the basicity, the lower the hydrogen content in a weld and the greater the toughness of a weld.

Scientists have observed a decrease in the content of hydrogen diffusing in a weld from 12 to 2ml per 100g of molten metal with a slag ratio increasing from 0 to 3 respectively. It has been established that the type of oxide present in a coating mixture affects the ease of slag separation from the surface of a weld.
Alloying Agents:
Before researching on alloying elements of weld, first of all it is necessary to investigate affinity of alloying elements to oxygen. According to the increasing affinity to oxygen elements most frequently of them can be arranged in the following line.

The elements located to the left of iron, during welding are practically assimilated completely by a welding pool. The tungsten and molybdenum located near to iron on the right are also almost fully assimilated by a welding pool. All other elements are oxidized and the more actively, than to the left from iron.
Alloying additions can be contained both in the core wire and in a covering of an electrode. The weld metal will dilute with base metal, Therefore the percentage of alloying elements in the base metal is effective in the final analysis of the weld metal.
Delta quantity is described as the amount of a specific element that is gained or lost during the welding process. The delta quantity is represented by the following mathematical equation:

The analytical content of element x is determined by chemical analysis of the weld metal whereas the estimated content is determined by adding the contribution from the core rod and base metal . a negative delta quantity , gives a loss of the specific element either to the slag or in a gaseous form . a positive delta quantity means that the flux contribution of the specific element was transferred to the weld metal to achieve a certaintarget weld composition. Delta quantity concept plays an important part in understanding the role of the flux ingredients in their contribution to the final weld composition.
Concentration of alloying elements in the weld metal depends on factors include:
- their content in a metal rod
- content of components in covering composition
- concentration of alloying element in that component
- coefficient of covering weight, and coefficients of alloying element transition from a covering and wire to metal
- Coefficients of alloying elements transition of a covering and wire differ
- The coefficient of transition shows physical and chemical properties of element intensity of element evaporation
- sputtering and other technological phenomena.
In practice orientation experimental average values of element transition coefficients are used. These values can be used only when conditions of a weld metal alloying and experiments are identical.
welding consumables designers will add useful elements to the weld metal structure through various combinations and through complex calculations and experiments .elements in form of many components added to flux formulations to enhance the properties of the weld metal. For example, Manganese is one of the most important elements in the weld metal structure in E7018 covered electrodes. it adds to weld metal by 4 different components like ferromanganese (LC & HC) , Manganese electrolytic ,etc. also the core wire manganese content will add to weld metal by defined rate. While in the GMAW wire (ER70S-6) the only source of adding manganese is just wire , So the designers will be adding manganese in the steelmaking process to reach the optimum content of manganese in final weld metal (Figure J10).
FIG J10
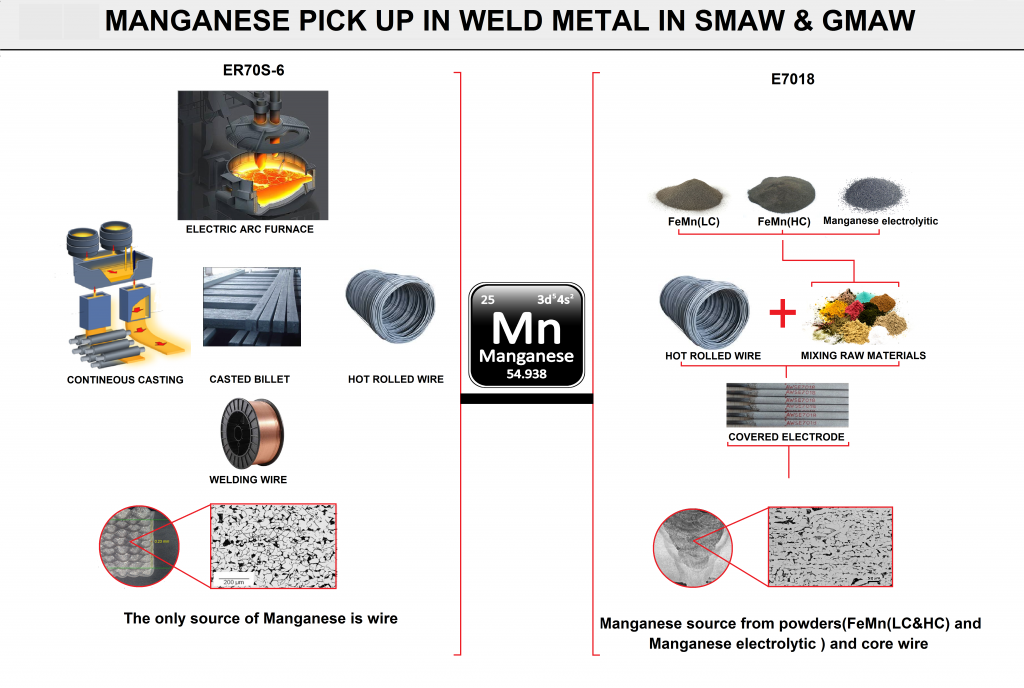
- Effect of Carbon:The most important constituent of steel weld metal. It raises tensile strength, hardness, and resistance to wear and abrasion. It lowers ductility, toughness and machinability.
- Effect of Manganese:A deoxidizer and de gasifier and reacts with sulfur to improve forgeability. It increases tensile strength, hardness, hardenability and resistance to wear. It decreases tendency toward scaling and distortion. It increases the rate of carbon-penetration in carburizing.
- Effect of Silicon: A deoxidizer and degasifier. It increases tensile and yield strength, hardness, forgeability and magnetic permeability.
- Effect of Molybdenum: Increases strength, hardness, hardenability, and toughness, as well as creep resistance and strength at elevated temperatures. It improves machinability and resistance to corrosion and it intensifies the effects of other alloying elements. In hot-work steels and high-speed steels, it increases red-hardness properties.
- Effect of Vanadium: Increases strength, hardness, wear-resistance, and resistance to shock impact. It retards grain growth, permitting higher quenching temperatures. It also enhances the red-hardness properties of high-speed metal cutting tools.
- Effect of Chromium: Increases tensile strength, hardness, hardenability, toughness, resistance to wear and abrasion, resistance to corrosion, and scaling at elevated temperatures.
- Effect of Titanium: Used as stabilizing elements in stainless steel. Each has a high affinity for carbon and forms carbides, which are uniformly dispersed throughout the steel. Thus, localized precipitation of carbides at grain boundaries is prevented.
- Effect of Cobalt: Increases strength and hardness and permits higher quenching temperatures and increases the red hardness of high-speed steel. It also intensifies the individual effects of other major elements in more complex steels.
- Effect of Nickel: Increases strength and hardness without sacrificing ductility and toughness. It also increases resistance to corrosion and scaling at elevated temperatures when introduced in suitable quantities in high-chromium (stainless) steels.
- Effect of Tungsten: Increases strength, wear resistance, hardness, and toughness. Tungsten steels have superior hot-working and greater cutting efficiency at elevated temperatures.
- Effect of Phosphorus: Increases strength and hardness and improves machinability. However, it adds marked brittleness or cold-shortness to steel.
- Effect of Sulfur: Improves machinability in free-cutting steels, but without sufficient manganese, it produces brittleness at red heat. It decreases weldability, impacts toughness, and ductility.
Ternary Diagram in Fusion Welding
One of the most important topics in identifying the raw materials reactions in fluxes to estimate the constituents in the slag and melt and its reactions is ternary system.
For example a ternary system of CaO-TiO2-SiO2,an approximate estimation as to the glass phases produced in the slag was determined using mass balance calculations. the CaO-TiO2-SiO2 phase diagram is shown in (figure F10).
in order to perform the mass balance calculations, the flux ingredients need to be broken down into their respective slag form (expressed in the form of of the slag . are performed, similar oxides are then grouped together such that the ternary system diagram of Cao-TiO2-SiO2 can be used .so Na2O-MgO,k2O are grouped together with CaO, and Al2O3 is grouped with TiO2.Recall that these groupings represent only an approximation and not exact stipulation of the slag type , but the methodology allows for the estimation of which are the possible predominant glass phase in the slag and the effect of the difference in the Coefficient thermal expansion values between the slag and the weld metal. with the compositions of these flux coating, calculations were made to determine the respective glass phases that could probably form in the resulting slags.
FIG F10
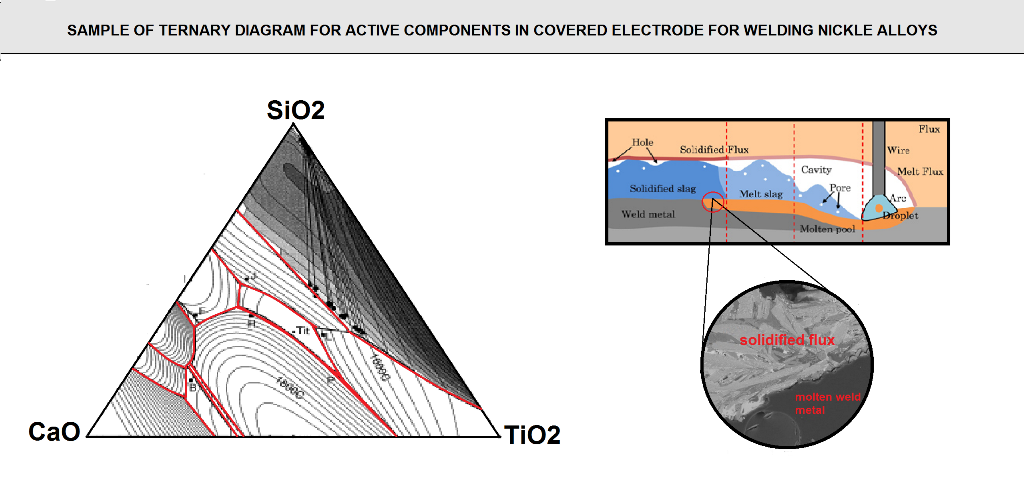
Raw Materials Production Process
Generally, the raw materials used in welding consumables production, classified in two main groups:
- Natural powders
- Synthetic powders
Following we describe about production process of some of powders in these two main group.
Natural Powders:
This raw materials are totally natural .This type of materials are usually extracted from mines of the appropriate purity. Identification of appropriate mineral vein is very important to prevent harmful substances from entering the extracted ores. The general process of producing these powders is crushing them in different ways.For example, in the process of producing calcium carbonate powder, mining engineers first discover the best high purity vein. Mining machines then exploited limestone mines to extract the large scale stones.
After mining process ,big blocks of CaCo3 are hammered into lumps at smaller size(20-30cm) then CaCo3 lumps are transported by trucks to the factory. before the production ,materials are carefully selected, washed and cleaned to ensure the quality of end product. Then materials are put into the jaw crusher for initial crushing. Smaller sizes of materials are made. After that, these materials are transferred by roller to hammer crusher for better crushing. At the end of the stage, materials are ready for grinding. They are stored in the feed silo. From the feed silo, materials are transported into the ball mill for fine grinding . ball mill contains of about 25 tons of steel ball.the materials from the ball mill will be blown passing through the classifier. the qualified particles passed through classifier shall be stored in product silo. Other shall be returned to the ball mill for further processing(figure K10).
Calcium fluoride (fluorspar) is the other mineral that is used in welding consumables. This mineral has many uses in different industries like electronics, optic and laser, ceramic, plastics, jewelry, decorative. this powder has the same production process like calcium carbonate (figure L10).
FIG K10
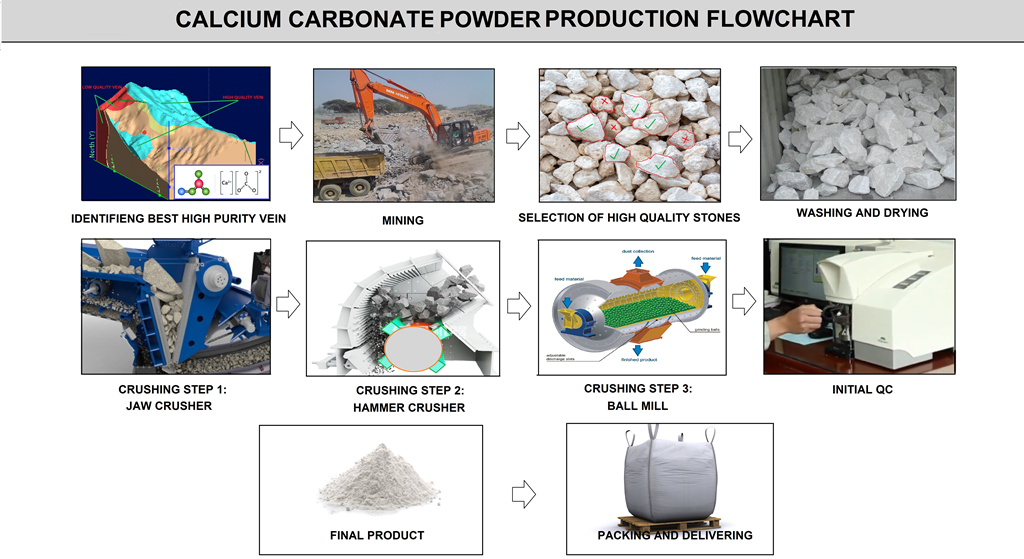
FIG L10
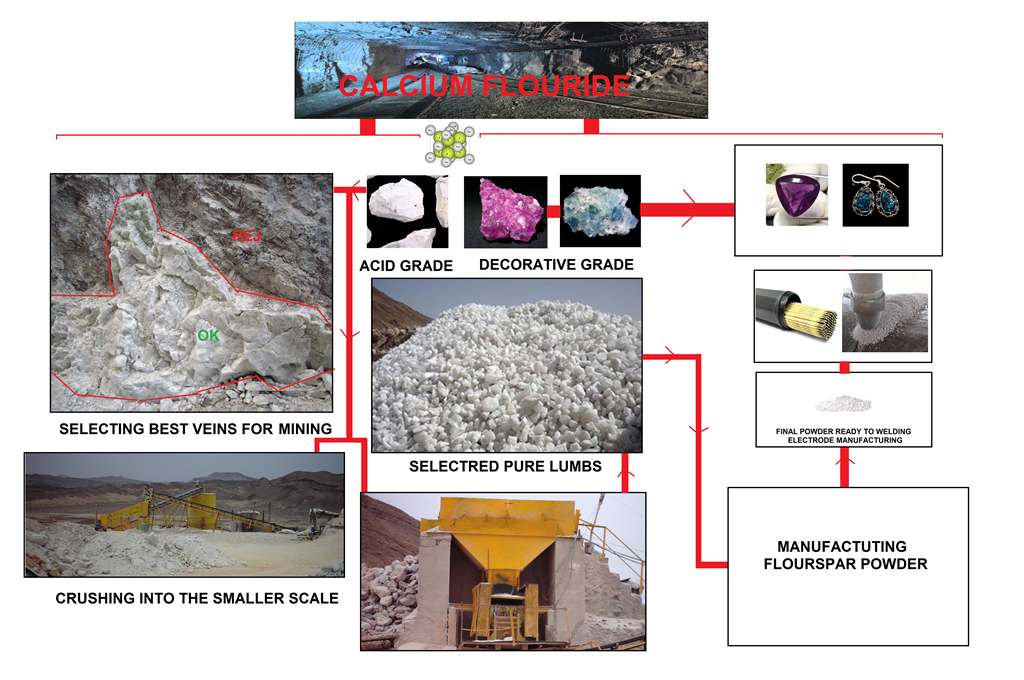
Synthetic Powders:
Naming raw materials in this category means that this group of materials has at least one intermediate process step for the processing of the raw material. For example in (figure M10) the production process of barium carbonate from barrite ore is shown .
Calcium carbonate is known as a natural powder that by a specific process, precipitated calcium carbonate is made. This powder is known as a synthetic powder. Precipitated calcium carbonate (PCC) is an innovative product derived from lime stone.
FIG M10
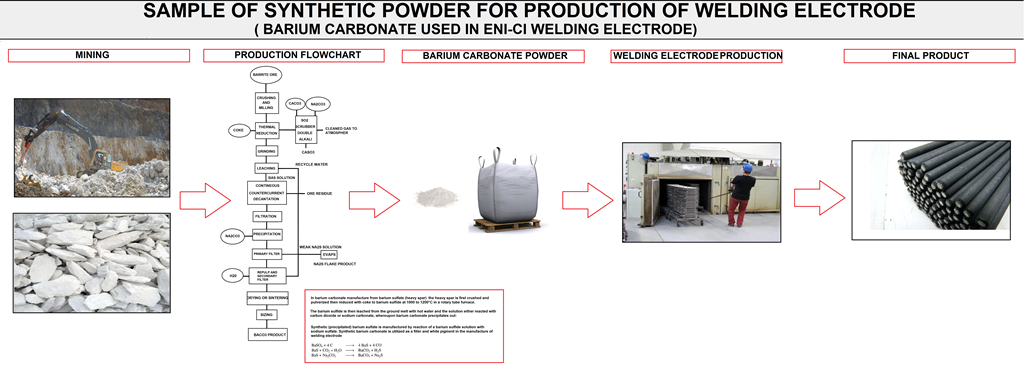
Calcination:
Calcinations is the process of subjecting a substance to the action of heat, but without fusion, for the purpose of causing some change in its physical or chemical constitution. also The purpose of this process is to remove physical and chemical water from the powders.
Calcination is also used to mean a thermal treatment process in the absence or limited supply of air or oxygen applied to ores and other solid materials to bring about a thermal decomposition. A calciner is a steel cylinder that rotates inside a heated furnace and performs indirect high-temperature processing (550–1150 °C, or 1000–2100 °F) within a controlled atmosphere.
Examples of calcination processes include the following:
- decomposition of carbonate ores, as in the calcination of limestone to drive off carbon dioxide.
- decomposition of hydrated minerals, as in the calcination of bauxite and gypsum, to remove water of crystallization as water vapor.
- decomposition of volatile matter contained in raw petroleum coke.
- heat treatment to effect phase transformations, as in conversion of anatise to rutile or devitrification of glass materials
- removal of ammoniumions in the synthesis of zeolites.
Bauxite calcined is one of the most important powders that are used in production of submerged arc welding fluxes. The importance of the calcination process is because if it is not done, the moisture content makes lot of problems in the finished product like porosity in weld metal and slag.
Atomization:
Atomized powder is a powder produced by the dispersion of a molten material into particles by a rapidly moving gas or liquid stream or by mechanical dispersion (figure Q10).
Ferrosilicon is often used in the coatings of manual metal arc electrodes, where it must not react with the binders used to make the extruded coating.It is found that crushed Ferrosilicon is too reactive and able to evolves gas that is producing defective coatings. It can be passivated by heating to a high temperature in air, but a water atomised product has a passive film already (~0.1% oxygen) and also has spherical shape, giving good paste rheology.
considerable amounts of Ferromanganese are used in welding consumables. High carbon Ferromanganese is easily crushed and milled, but lower carbon grades are increasingly difficult. Carbon levels in welding consumables are often low, but vary. Atomization of FeMn with water results in considerable oxidation (~1-3% oxygen) which may be undesirable.
FIG Q10
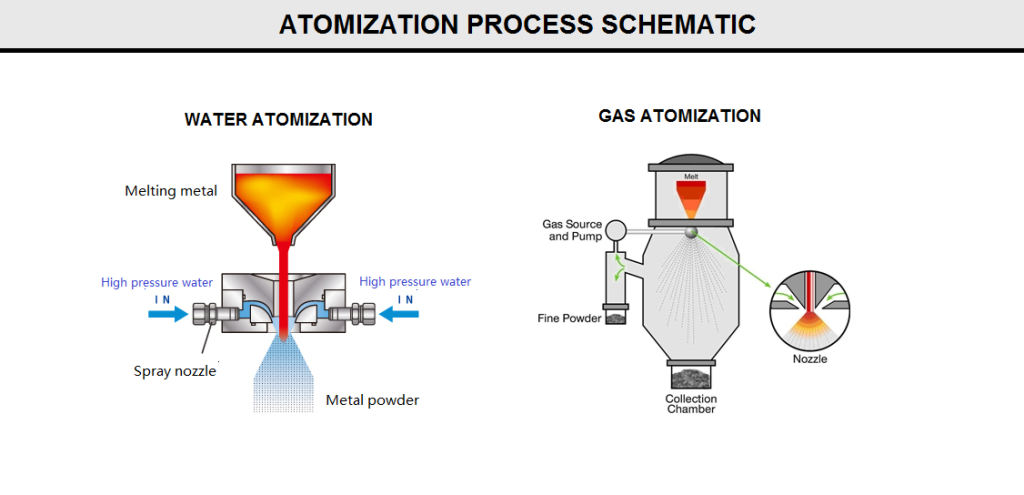
Precipitation:
Chemical precipitation is the most common technology used in removing dissolved (ionic) metals from solutions, such as process wastewaters containing metals. The ionic metals are converted to an insoluble form (particle) by the chemical reaction between the soluble metal compounds and the precipitating reagent. The particles formed by this reaction are removed from solution by settling and/or filtration.
Calcium carbonate is prepared from calcium oxide. Water is added to give calcium hydroxide then carbon dioxide is passed through this solution to precipitate the desired calcium carbonate, referred to in the industry as precipitated calcium carbonate (PCC).

Stabilization:
This process is intended to stabilize the material’s reactivity to prevent undesirable and harmful reactions to this material. For each material, the process is performed differently.
For example low-carbon ferromanganese requires stabilization process due to its high reactivity with ambient oxygen. Stabilization of this powder is done by coating the surface of the powder by oxidizing agent like Potassium dichromate. Magnesium is the other active powder. Surface of magnesium particles is highly reactive and may be oxidized easily during storage at ambient conditions. Coating the surface of metal particles with a layer of polymer could be a simple and efficient way to prevent oxidation.
Making Metal Powder
There are four main processes used in metal raw materials production: solid-state reduction, atomization, electrolysis, and chemical.
1) Solid-State Reduction
In solid-state reduction, selected ore is crushed, typically mixed with carbon, and passed through a continuous furnace. In the furnace, a reaction takes place, reducing the carbon and oxygen from the powder, that leaves a cake of sponge metal which is then crushed, separated from all non-metallic material, and sieved to produce powder. Since no refining operation is involved, the purity of the powder is dependent on the purity of the raw materials. The irregular sponge-like particles are soft, readily compressible, and give compacts of good pre-sinter (“green”) strength.
2) Atomization
In this process, molten metal is separated into small droplets and frozen rapidly before the drops come into contact with each other or with a solid surface. Typically, a thin stream of molten metal is disintegrated by subjecting it to the impact of high-energy jets of gas or liquid. In principle, the technique is applicable to all metals that can be melted and is used commercially for the production of iron; copper; alloy steels; brass; bronze; low-melting-point metals such as aluminum, tin, lead, zinc, and cadmium; and, in selected instances, tungsten, titanium, rhenium, and other high-melting-point materials.
3) Electrolysis
By choosing suitable conditions, such as electrolyte composition and concentration, temperature, and current density, many metals can be deposited in a spongy or powdery state. Further processing—washing, drying, reducing, annealing, and crushing—is often required, ultimately yielding high-purity and high-density powders. Copper is the primary metal produced by electrolysis but iron, chromium,manganese, and magnesium powders are also produced this way. Due to its associated high energy costs, electrolysis is generally limited to high-value powders such as high-conductivity copper powders.
4) Chemical
The most common chemical powder treatments involve oxide reduction, precipitation from solutions, and thermal decomposition. The powders produced can have a great variation in properties and yet have closely controlled particle size and shape. Oxide-reduced powders are often characterized as “spongy,” due to pores present within individual particles. Solution-precipitated powders can provide narrow particle size distributions and high purity. Thermal decomposition is most often used to process carbonyls. These powders, once milled and annealed, exceed 99.5% purity.