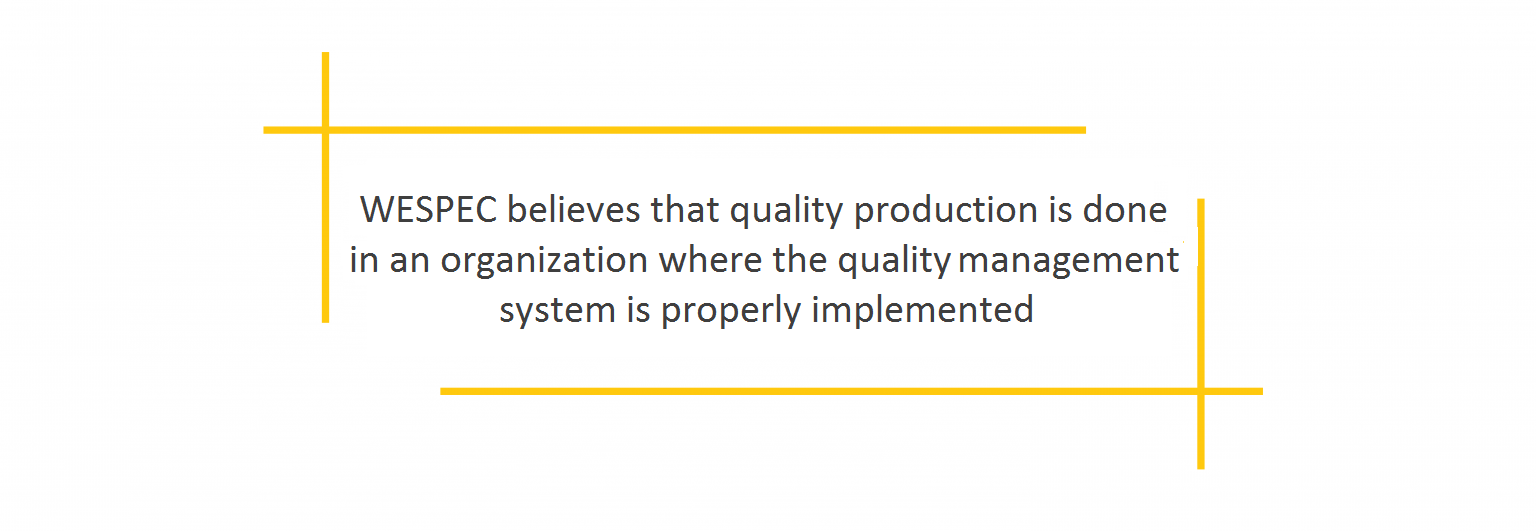
What is Quality Management System
A Quality Management System, often called a QMS, is a set of internal rules that are defined by a collection of policies, processes, documented procedures and records. This system defines how a company will achieve the creation and delivery of the product or service they provide to their customers. When implemented in your company, the QMS needs to be specific to the product or service you provide, so it is important to tailor it to your needs. However, in order to help ensure that you do not miss elements of a good system, some general guidelines exist in the form of ISO 9001 (Quality Management System – Requirements), which is intended to help standardize how a QMS is designed.
Quality Management System Common Elements
Quality Management System processes start with the initial management planning stages of a company, which define the goals of the company including what products or services the company will be offering. The system then deals with all processes needed, from sales of the product or service through creation and finally delivery of the product or service to the customer.
Additionally, the support processes for this to happen are controlled as part of the system. This will include managing resources like people and equipment, procedures to control documents and records, and documents defining how to control products or services that do not meet requirements.
Finally, there are processes as part of the QMS that are designed to monitor the processes of the system and lead to improvement. These processes will include a method of auditing the system processes, means of applying corrective and preventive actions for problems and a way for management to review the system to ensure requirements are met and plans are made for improvements.
One of the best ways to ensure that your system has included all applicable processes is to refer to a standard set of requirements for Quality management Systems. The ISO 9001 standard is one such set of requirements that defines and outlines all the typical policies, processes, documented procedures and records that are needed for a successful QMS, and can be used and tailored for the needs of any organization.
Some challenges of developing a QMS
Quality Management System development can have some challenging aspects. One of the first is to overcome the misconception of thinking a QMS only refers to the processes necessary to deal with inspection and disposition of non-conforming products, often designated to members of a quality control department. Such a system only manages the inspection of product, while not managing the inputs that help a product or service to be compliant in the first place, effectively trying to inspect quality into the product or service.
Once this is overcome, the biggest challenges are in demonstrating the commitment of management by having the overlying policies defined and communicated to all levels of the organization. Then the QMS can be made to work as a method of ensuring that all necessary requirements are defined and met, and improvements are made.
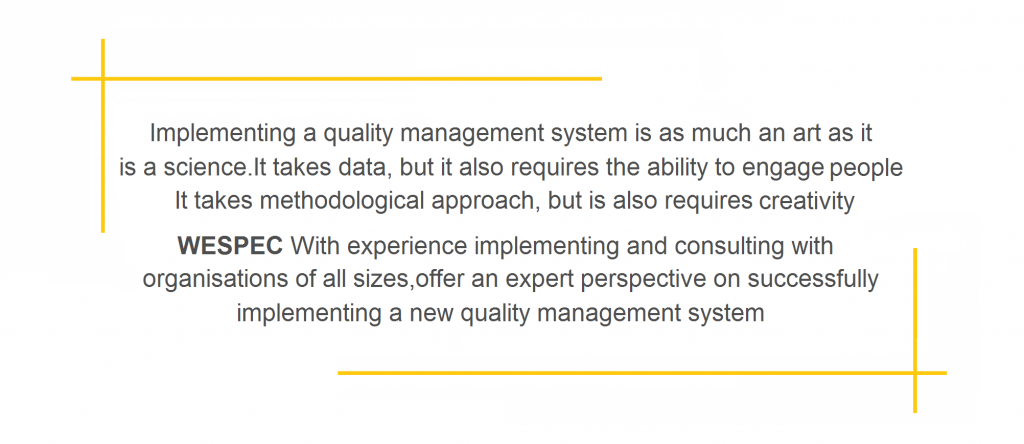