The Effect of Raw Materials on the Quality of Welding Electrodes and Fluxes
The quality and performance of welding consumables largely depend on the raw materials used in their production. Specifically, Detailed Study of Welding Consumables Raw Materials in powder form play a crucial role in understanding the properties and effectiveness of welding electrodes and sub-arc welding fluxes.
As technology advances, the continued research and optimization of these raw materials will further enhance welding efficiency and effectiveness.
In this article, a list of these raw powder materials is mentioned and the characteristics and effects of some of important ones are described.
Also you can read This Article About Classification of these raw materials and their Specification and This Article about the Meaning of Know-How in Welding Consumables Production.
Introduction
A Sample List of Raw Materials
Cellulose Powders Specifications and Their Effect for Welding Consumables
Rutile Powders Specifications and Their Effect for Welding Consumables
Iron Powders Specifications and Their Effect for Welding Consumables
Ferro Manganese Powders Specifications and Their Effect for Welding Consumables
Ferro Silicon Powders Specifications and Their Effect for Welding Consumables
Calcium Fluoride Powders Specifications and Their Effect on Welding Consumables
Calcium Carbonate Powders Specifications and Their Effect for Welding Consumables
Mica Powders Specifications and Their Effect for Welding Consumables
Kaolin Powders Specifications and Their Effect for Welding Consumables
Potassium Feldspar Powders Specifications and Their Effect for Welding Consumables
Sodium Carboxy Methyl Cellulose Powders Specifications and Their Effect for Welding Consumables
Sample of Raw Materials
The following materials, which are in powder form, are used in the production of various welding consumables, each of these materials has a unique chemical analysis and grain size for the best output quality. Before reading this list, see the material specification for potassium feldspar powder as below:
Potassium Feldspar Powder as an Example of Specification sheet of the Raw Materials for Welding Consumables Production
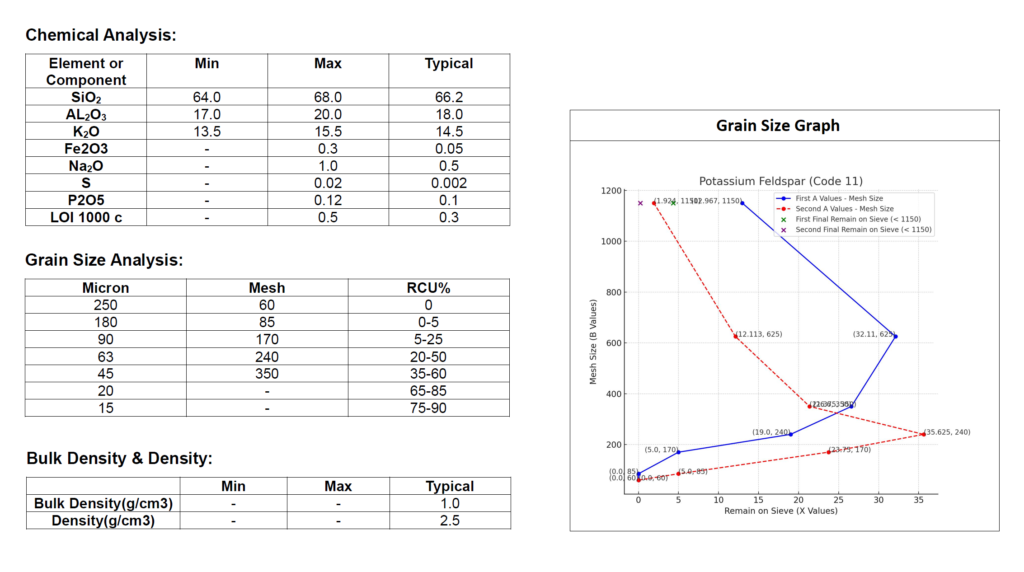
Sample of Raw Materials in Welding Consumables Production
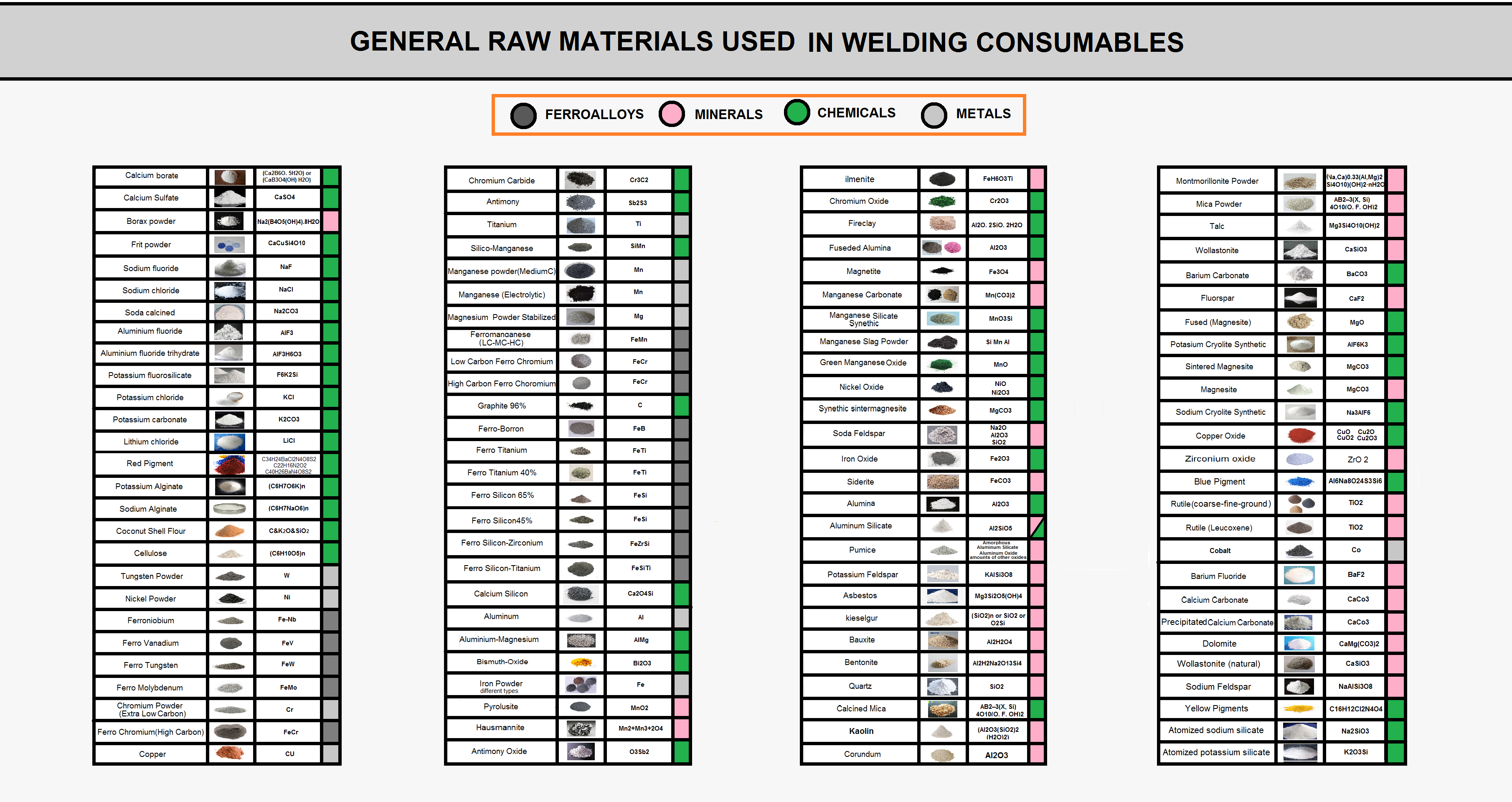
Calcium borate
Calcium Sulfate
Borax powder
Frit powder
Sodium fluoride
Sodium chloride
Soda calcined
Aluminum fluoride
Aluminum fluoride trihydrate
Potassium fluorosilicate
Potassium chloride
Potassium carbonate
Lithium chloride
Red Pigment
Potassium Alginate
Sodium Alginate
Coconut Shell Flour
Cellulose
Tungsten Powder
Nickel Powder
Ferroniobium
Ferro Vanadium
Ferro Tungsten
Ferro Molybdenum
Chromium Powder (Extra Low Carbon)
Ferro Chromium (High Carbon)
Copper
Chromium Carbide
Antimony
Titanium
Silico-Manganese
Manganese powder (Medium C)
Manganese (Electrolytic)
Magnesium Powder Stabilized
Ferromanganese (LC-MC-HC)
Low Carbon Ferro Chromium
High Carbon Ferro Chromium
Graphite 96%
Ferro-Boron
Ferro Titanium
Ferro Titanium 40%
Ferro Silicon 65%
Ferro Silicon 45%
Ferro Silicon-Zirconium
Ferro Silicon-Titanium
Calcium Silicon
Aluminum
Aluminum-Magnesium
Bismuth-Oxide
Iron Powder (different types)
Pyrolusite
Hausmannite
Antimony Oxide
Ilmenite
Chromium Oxide
Fireclay
Fused Alumina
Magnetite
Manganese Carbonate
Manganese Silicate
Manganese Slag Powder
Green Manganese Oxide
Nickel Oxide
Synthetic intermagnesite
Soda Feldspar
Iron Oxide
Siderite
Alumina
Aluminum Silicate
Pumice
Potassium Feldspar
Asbestos
Kieselgur
Bauxite
Bentonite
Quartz
Calcined Mica
Kaolin
Corundum
Montmorillonite Powder
Mica Powder
Talc
Wollastonite
Barium Carbonate
Fluorspar
Fused (Magnesite)
Potassium Cryolite Synthetic
Sintered Magnesite
Magnesite
Sodium Cryolite Synthetic
Copper Oxide
Zirconium Oxide
Blue Pigment
Rutile (coarse-fine-ground)
Rutile (Leucoxene)
Cobalt
Barium Fluoride
Calcium Carbonate
Precipitated Calcium Carbonate
Dolomite
Wollastonite (natural)
Sodium Feldspar
Yellow Pigments
Atomized sodium silicate
Atomized potassium silicate
Cellulose Powders Specifications and Their Effect for Welding Consumables
An image of cellulose powder with a photographic camera
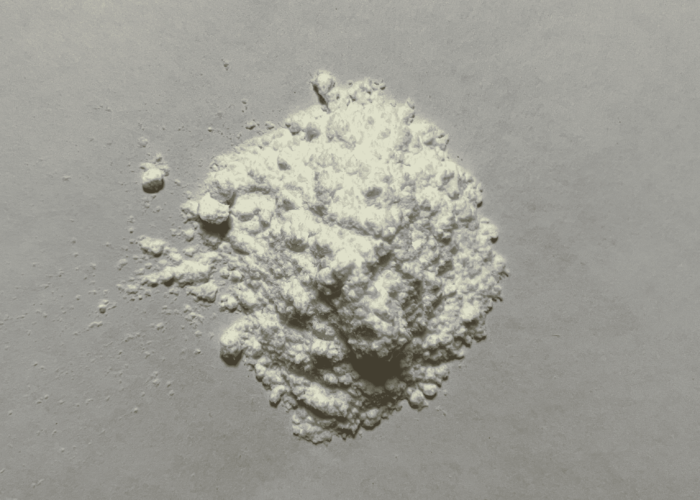
Cellulose powder is commonly used as a key component in the coating of welding electrodes, particularly in shielded metal arc welding (SMAW) electrodes. It has several significant effects on the quality of the final welded product.
Enhanced Arc Stability:
- Effect: Cellulose in the electrode coating decomposes during welding, producing gases such as carbon dioxide and hydrogen. This helps stabilize the arc and maintain a consistent welding process.
- Quality Impact: A stable arc results in smoother and more uniform welds, reducing defects such as porosity or incomplete fusion.
Improved Penetration:
- Effect: The gases generated from the cellulose provide a forceful arc that improves the penetration of the weld into the base material.
- Quality Impact: Deeper penetration ensures stronger welds, particularly beneficial for thick materials.
Slag Formation and Removal:
- Effect: The cellulose contributes to the formation of a slag layer on the weld pool. This slag solidifies on top of the weld and can be easily removed after cooling.
- Quality Impact: Proper slag formation and easy removal protect the weld from atmospheric contamination during cooling.
Reduced Hydrogen Embrittlement:
- Effect: Cellulose decomposition releases hydrogen, which can be a double-edged sword. While hydrogen can cause porosity if not managed properly, the controlled release in the right quantity can help reduce hydrogen embrittlement.
- Quality Impact: By managing hydrogen levels, the risk of weld cracking due to hydrogen embrittlement is minimized, which is crucial for maintaining the toughness and strength of the weld, especially in high-strength steels.
Control of Cooling Rate:
- Effect: The slag produced by cellulose decomposition can influence the cooling rate of the weld.
- Quality Impact: Controlled cooling rates help in reducing the risk of forming undesirable microstructures that can compromise the mechanical properties of the weld, such as brittleness or hardness issues.
Enhanced Mechanical Properties:
- Effect: The cellulose in the coating affects the weld metal composition and cooling characteristics, influencing the final microstructure.
- Quality Impact: The resulting weld typically exhibits better mechanical properties, such as increased tensile strength, ductility, and impact resistance.
An image of different types of cellulose by SEM
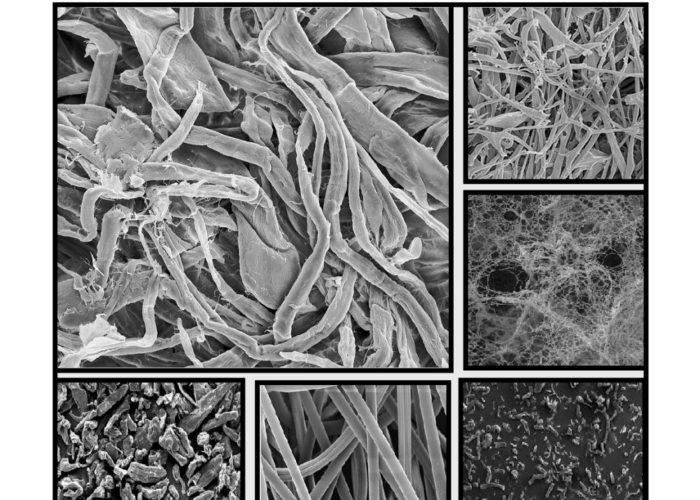
In the production of welding consumables, particularly in the formulation of electrode coatings, several types of cellulose powders are used. These can be broadly categorized based on their source, processing method, and specific properties.
Here are some common types and their specifications and differences:
- Wood Cellulose Powder:
- Source: Derived from wood pulp.
- Specifications: Typically has a high purity level with low ash content. It may have a particle size range from 20 to 200 microns.
- Differences: Offers consistent quality and is widely available. It tends to have higher carbon content, which can affect the gas generation during welding.
- Cotton Cellulose Powder:
- Source: Derived from cotton linters.
- Specifications: Generally has higher cellulose content and lower lignin compared to wood cellulose. Particle size can vary but is often fine, around 20 to 150 microns.
- Differences: Produces less slag and has better thermal stability. It is often used in high-quality electrodes for critical welding applications.
- Alpha Cellulose Powder:
- Source: Derived from highly purified wood or cotton.
- Specifications: Contains at least 90-95% alpha cellulose. It is highly purified and usually has a very fine particle size, around 20 to 100 microns.
- Differences: Provides excellent thermal stability and gas generation characteristics. It is more expensive due to its high purity but results in very stable and clean welds.
- Microcrystalline Cellulose (MCC):
- Source: Derived from refined wood pulp or cotton.
- Specifications: Consists of fine, crystalline particles, usually in the range of 10 to 50 microns. It has high purity and low moisture content.
- Differences: Offers superior control over gas generation and arc stability. It is used in specialized electrodes where precision and consistency are critical.
- Recycled Cellulose Powder:
- Source: Derived from recycled paper or other cellulose-containing materials.
- Specifications: Varies widely in purity and particle size, typically 50 to 200 microns.
- Differences: More cost-effective but may have inconsistent quality and higher impurity levels, which can affect weld quality. It is often used in lower-cost or less critical applications.
Key Differences and Impact on Welding Consumables
- Purity:
- Higher purity cellulose powders (like alpha cellulose and MCC) result in cleaner welds with fewer impurities and defects.
- Lower purity powders (like recycled cellulose) may introduce contaminants into the weld, affecting its quality.
- Particle Size:
- Finer particles (like those in MCC and alpha cellulose) provide better control over the welding process and more consistent gas generation.
- Coarser particles may result in less stable arcs and more spatter.
- Source:
- The source material affects the cellulose’s inherent properties, such as carbon content, lignin content, and thermal stability.
- Cotton-derived cellulose generally offers better performance than wood-derived cellulose in terms of slag formation and gas generation.
- Cost:
- Higher purity and more refined cellulose powders are more expensive but offer better performance and are used in critical applications.
- Lower-cost powders are used in general-purpose or non-critical welding applications where high performance is not as crucial.
By selecting the appropriate type of cellulose powder, manufacturers can set the properties of welding consumables to meet specific requirements, balancing cost, performance, and application needs.
Rutile Powders Specifications and Their Effect for Welding Consumables
An image of Rutile Sand powder with a photographic camera

Rutile is a naturally occurring mineral form of titanium dioxide (TiO₂). It is typically found in igneous and metamorphic rocks and is a significant ore of titanium. Rutile has several properties that make it particularly valuable in industrial applications, including its high refractive index, strong optical dispersion, and chemical stability. In the context of welding electrodes, rutile sand is processed into a fine powder that can be incorporated into the coating of the electrodes.
Rutile powder is used in the coating of welding electrodes, particularly in those designed for shielded metal arc welding (SMAW). The presence of rutile in the electrode coating has several important effects on the welding process and the quality of the welds produced.
Nature of Rutile Sand
Rutile sand is a naturally occurring mineral found in heavy mineral sand deposits, typically in coastal and riverine environments. These deposits often include a mix of minerals like ilmenite, zircon, and rutile. Rutile sand is prized for its high titanium dioxide content, which can range from 90% to 96%, making it an important raw material for various industrial applications, including welding electrode production.
Key Characteristics of Rutile Sand:
- High Titanium Content: High purity of titanium dioxide is a significant factor in its desirability.
- Natural Grain Size: The sand consists of naturally occurring grains, typically in the range of 0.1 to 0.5 mm in diameter.
- Chemical Stability: Rutile is chemically stable, resistant to corrosion, and non-reactive with most substances.
Production and Processing of Rutile Sand
The processing of rutile sand involves several stages, ensuring that the material meets the specifications required for its end-use, including in welding electrodes:
- Mining: Rutile sand is mined from mineral sand deposits, which are usually located near coastal regions. The mining process involves dredging or dry mining, depending on the location and nature of the deposit.
- Separation: After mining, the raw sand is processed to separate the rutile from other heavy minerals like ilmenite, zircon, and monazite. This is typically done using gravity separation, magnetic separation, and electrostatic separation techniques.
- Purification: The separated rutile is further purified to increase the concentration of titanium dioxide, often through processes like leaching to remove any remaining impurities.
- Size Classification: The rutile sand is classified based on grain size. For welding electrode production, it might be further processed into a more consistent particle size or ground into a finer powder.
- Quality Control: The final product undergoes quality control checks to ensure it meets the required standards for titanium dioxide content, grain size, and absence of impurities .
Microscopic Image of Rutile Sand
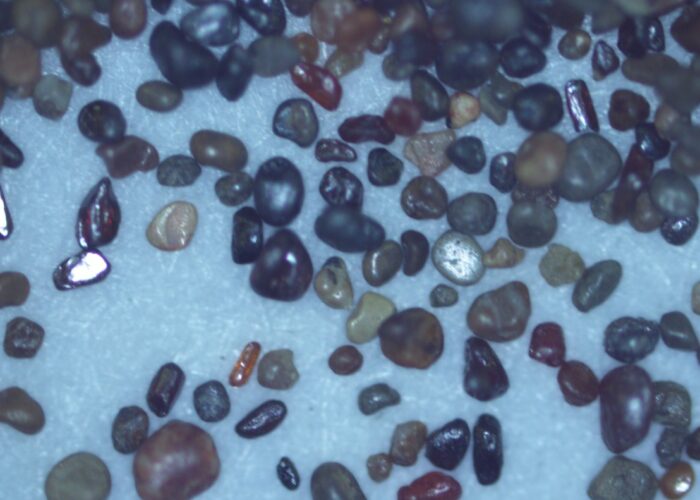
Effect of Rutile Sand on Welding Electrodes
1. Weld Quality and Mechanical Properties
- Arc Stability: Rutile in the electrode coating stabilizes the welding arc. A stable arc is critical for consistent heat input, which directly influences the quality of the weld bead. Stable arcs produce welds with fewer defects like porosity, slag inclusions, or incomplete fusion.
- Mechanical Properties: Rutile-based electrodes typically produce welds with good mechanical properties, including high tensile strength and ductility. The titanium dioxide in rutile contributes to the formation of a stable, strong weld metal that can withstand stress and strain, making it ideal for structural applications.
2. Slag Formation and Removal
- Protective Slag Layer: Rutile contributes to the formation of a slag layer on top of the weld pool. This slag is essential for protecting the molten metal from atmospheric gases like oxygen and nitrogen, which could otherwise lead to oxidation and nitriding, causing defects in the weld.
- Easy Slag Removal: The slag formed by rutile-based electrodes is generally easy to remove once the weld cools. This leads to cleaner weld surfaces, reducing post-weld cleaning time and effort, and minimizing the risk of weld defects related to slag inclusions.
3.Surface Finish
- Smooth Weld Appearance: Welds made with rutile-based electrodes tend to have a smooth and aesthetically pleasing surface finish. This is important in applications where weld appearance is crucial, such as in exposed structures or piping.
4. Ease of Use
- User-Friendly Characteristics: Rutile-based electrodes are known for their ease of use, even in challenging welding positions (e.g., vertical or overhead). This makes them popular for a wide range of applications, from industrial manufacturing to repair work. The ease of use also means that less skilled welders can produce acceptable welds, increasing productivity and reducing training costs.
5. Impact on Welding Efficiency
- High Deposition Rate: Rutile electrodes typically offer a high deposition rate, meaning more metal is deposited per unit of time, which improves welding efficiency. This is particularly beneficial in high-volume welding operations where time and productivity are critical factors.
- Versatility Across Positions: The ability to use rutile electrodes in all positions (flat, horizontal, vertical, and overhead) without significant changes in technique or settings enhances operational flexibility and efficiency.
6. Cost-Effectiveness
- Material Costs: The use of rutile sand in electrode coatings can be cost-effective, depending on the availability and processing costs of rutile. This cost-effectiveness, combined with the high-quality welds produced, can lower overall welding costs.
- Reduced Post-Weld Processing: The easy removal of slag and the good surface finish of welds made with rutile electrodes can reduce the need for extensive post-weld processing, such as grinding or polishing, further contributing to cost savings.
Another type of rutile used in the production of welding electrodes is Rutile Flour witch is the crushed version of Rutile Sand.Rutile flour and rutile sand are both derived from the mineral rutile (TiO₂), but they differ in their physical form, particle size, and applications in welding electrode manufacturing.
While both rutile flour and rutile sand are valuable in welding electrode manufacturing, rutile flour tends to provide superior performance in terms of arc stability, surface finish, and overall weld quality. Rutile sand, while still effective, may be more suitable for applications where cost is a primary concern and slightly less emphasis is placed on weld appearance or the highest level of mechanical performance.
An image of Rutile Flour powder with a photographic camera
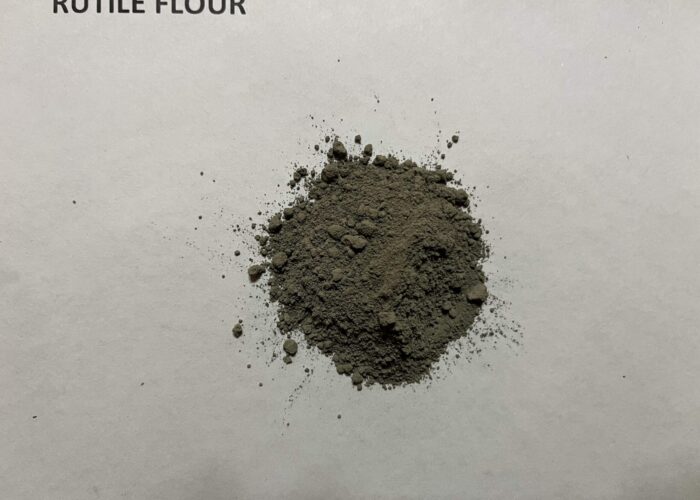
Iron Powders Specifications and Their Effect for Welding Consumables
Iron powders are an essential component in the formulation of welding electrodes, particularly in the production of flux-cored arc welding (FCAW) and shielded metal arc welding (SMAW) electrodes. The type and characteristics of iron powder used can significantly influence the properties of the welding electrode, affecting the welding process and the quality of the welds. Here’s an overview of the different types of iron powders and their effects in welding electrode manufacturing:
Reduced Water Atomized Iron Powder
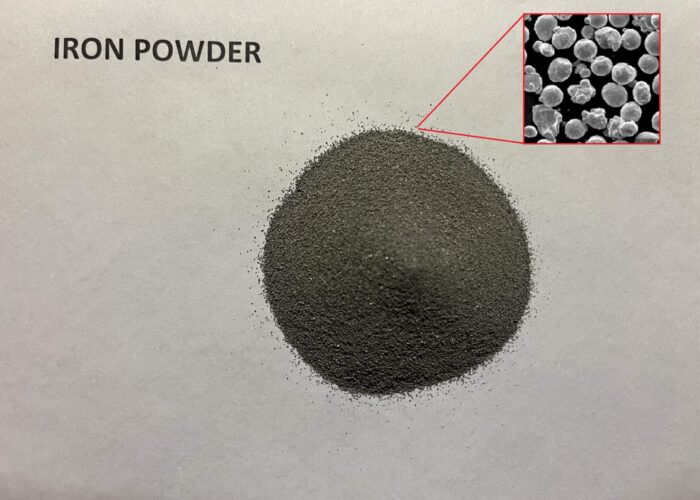
Ferro Manganese Powders Specifications and Their Effect on Welding Consumables
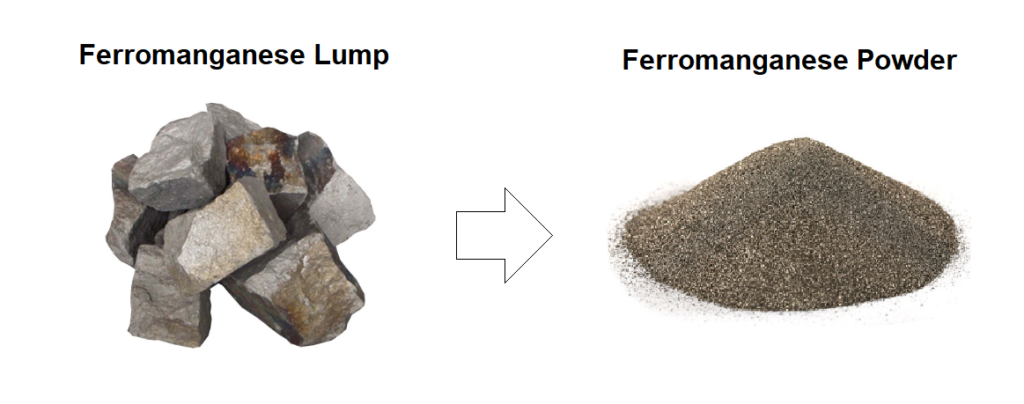
Ferro Silicon Powders Specifications and Their Effect on Welding Consumables
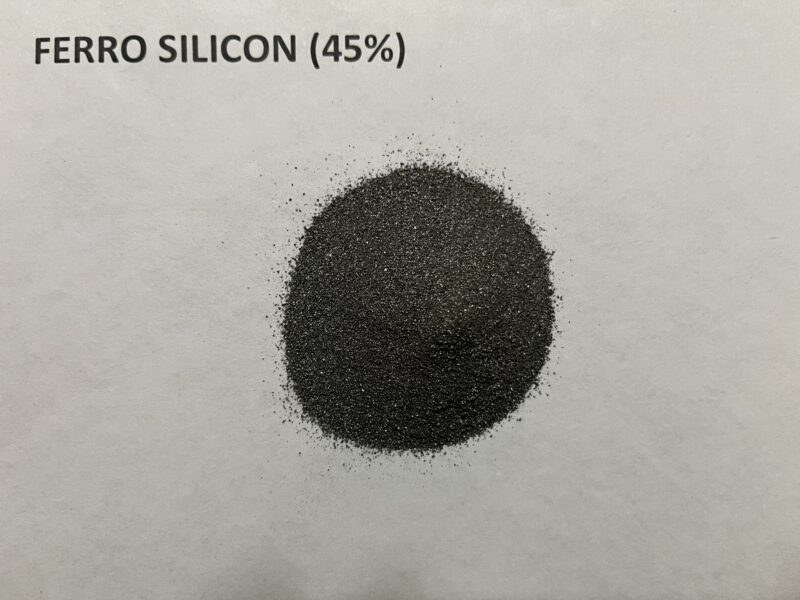
Calcium Fluoride Powders Specifications and Their Effect on Welding Consumables
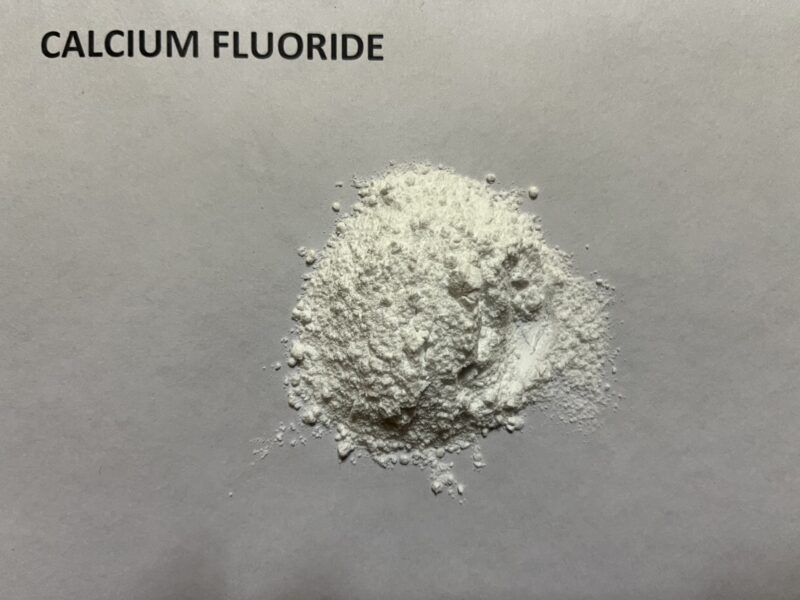
Calcium Carbonate Powders Specifications and Their Effect on Welding Consumables
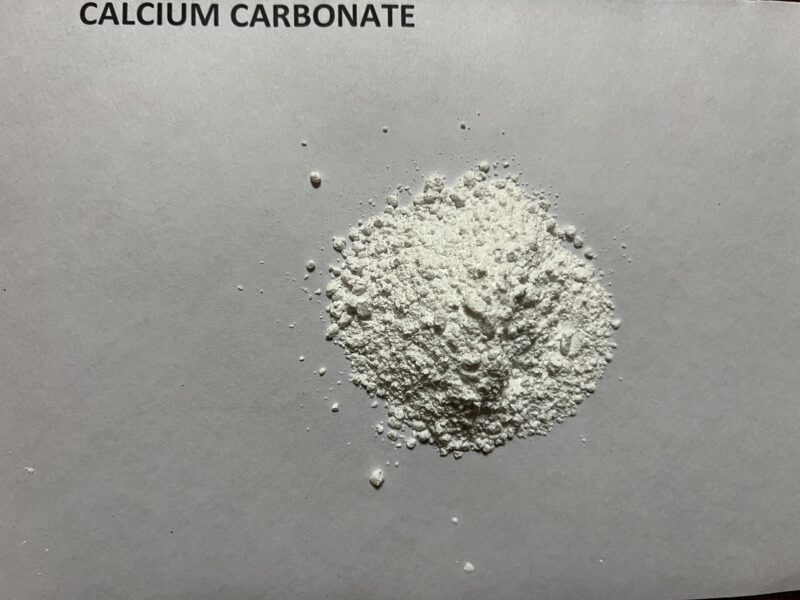
Mica Powders Specifications and Their Effect on Welding Consumables
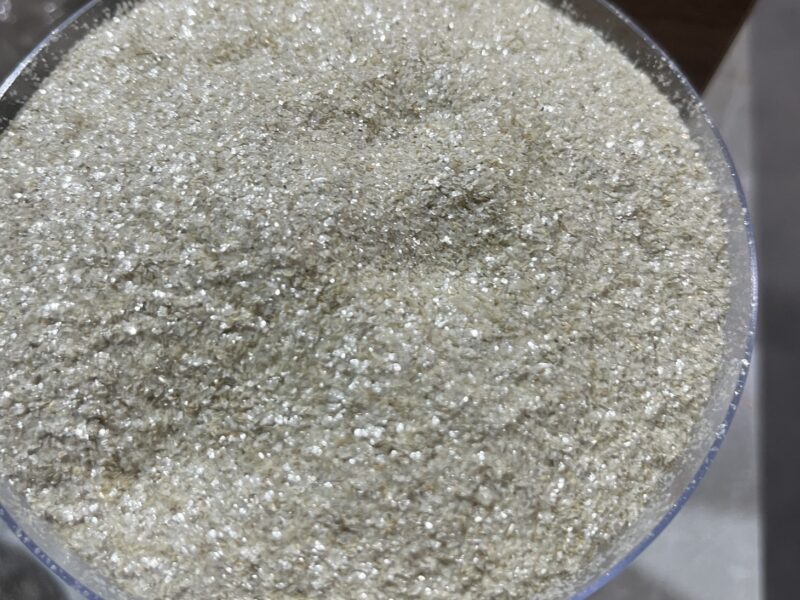
Mica is a naturally occurring silicate mineral with a layered structure, known for its thermal stability, electrical insulating properties, and flake-like appearance. It is used as a raw material in welding electrodes and occasionally in submerged arc welding (SAW) fluxes due to its unique physical and chemical characteristics.
Mica plays a crucial role in welding electrodes and, to a lesser extent, in submerged arc welding fluxes. Its contributions to coating durability, arc stability, and slag behavior enhance the overall quality and performance of welding consumables. Proper selection of mica type, particle size, and usage proportion ensures optimal results in welding applications.
Production of Mica
Mica is mined from natural deposits, followed by processing to suit industrial applications:
- Mining:
- Extracted from mines as mica schist, pegmatite, or metamorphic rocks.
- Key sources include India, China, and Brazil.
- Processing:
- Crushing and Screening: Large mica rocks are crushed into smaller pieces.
- Grading and Purification:
- Graded by particle size and purity.
- Purification processes remove impurities like quartz, feldspar, and other associated minerals.
- Splitting or Pulverizing:
- Depending on the application, mica is split into thin sheets or ground into fine powder.
- Types Based on Form:
- Sheet Mica: Used in specialized applications, typically not for welding.
- Powdered Mica: Widely used in welding consumables.
Types of Mica
- Natural Mica:
- Unmodified mica obtained directly from natural sources.
- Used in welding applications where standard properties are sufficient.
- Synthetic Mica:
- Manufactured for high-purity applications.
- Offers consistent performance with minimal impurities.
- Coated Mica:
- Coated with additional materials (e.g., resins) to enhance specific properties.
- Calcined Mica:
- Heat-treated to remove volatile components, improving thermal stability and electrical insulation.
Role of Mica in Welding Consumables
1. Covered Welding Electrodes
- Binder and Coating Stability:
- Mica helps maintain the integrity of the electrode coating, reducing cracking during drying and storage.
- Thermal Stability:
- Provides high thermal resistance, ensuring stable performance under welding heat.
- Slag Formation:
- Enhances the quality of slag, contributing to better protection of the weld pool and easier slag removal.
- Arc Stability:
- Helps maintain a stable arc during welding, reducing fluctuations and spatter.
- Moisture Resistance:
- Improves moisture resistance in the coating, preventing hydrogen-induced defects like porosity and cracking.
2. Submerged Arc Welding Fluxes
- Slag Behavior:
- Although less commonly used in SAW fluxes, mica can influence slag viscosity and behavior, ensuring better protection of the molten weld pool.
- Thermal Properties:
- Enhances the flux’s thermal resistance, aiding in high-temperature welding processes.
Effect on the Quality of Welding Electrodes and Fluxes
- Coating Durability:
- Mica’s flake-like structure provides flexibility and reduces the risk of coating cracks during handling and storage.
- Weld Purity:
- Acts as a barrier to contaminants like atmospheric moisture, reducing hydrogen-induced porosity in welds.
- Arc Stability:
- Contributes to smooth and consistent arc characteristics, minimizing spatter and improving weld bead appearance.
- Slag Characteristics:
- Produces a protective, easy-to-remove slag that enhances weld quality and reduces post-weld cleaning effort.
- Thermal Performance:
- Its high heat resistance improves electrode performance in demanding conditions and reduces coating breakdown during welding.
- Electrode Shelf Life:
- Reduces moisture absorption in electrode coatings, extending shelf life and maintaining consistent performance.
Key Considerations
- Purity:
- High-purity mica is preferred to avoid contamination that could affect weld quality.
- Particle Size:
- Finer particles are used for uniform coating distribution, while coarser particles may be employed for specific slag behavior.
- Usage Proportion:
- Excessive mica in the formulation can make slag too viscous, complicating removal.
Kaolin Powders Specifications and Their Effect on Welding Consumables
Potassium Feldspar Powders Specifications and Their Effect on Welding Consumables
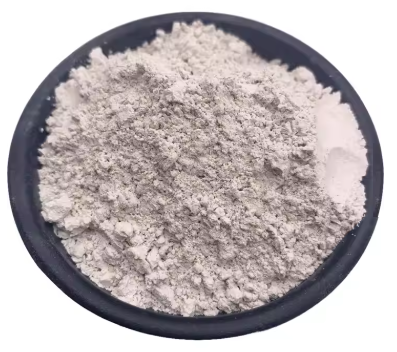
Potassium feldspar (KAlSi₃O₈) is a naturally occurring mineral used in welding consumables like covered electrodes and submerged arc welding (SAW) fluxes. It contributes to slag formation, arc stability, and weld metal properties due to its high potassium and aluminosilicate content.
Potassium feldspar is a versatile and critical raw material in welding consumables. It plays a significant role in slag formation, arc stability, and coating durability in welding electrodes, as well as slag behavior and weld metal properties in SAW fluxes. By selecting the appropriate grade and optimizing its proportion in formulations, manufacturers can achieve superior weld quality and performance in a variety of welding applications.
Production of Potassium Feldspar
- Mining:
- Potassium feldspar is extracted from natural deposits, typically found in igneous, metamorphic, and sedimentary rocks.
- Major sources include countries like India, Turkey, China, and the USA.
- Processing:
- Crushing and Grinding:
- The mined ore is crushed and milled to the desired particle size.
- Purification:
- Impurities such as quartz, mica, and iron oxides are removed through magnetic separation, flotation, or chemical treatment.
- Grading:
- The feldspar is graded into different particle sizes and purity levels for specific applications.
- Crushing and Grinding:
- Optional Modifications:
- In some cases, feldspar is calcined (heat-treated) to enhance its thermal stability.
Types of Potassium Feldspar
- Natural Potassium Feldspar:
- Used directly after mining and purification.
- Contains minor impurities that may be acceptable for general applications.
- High-Purity Potassium Feldspar:
- Processed to remove most impurities, ensuring consistent chemical properties.
- Preferred for critical welding applications.
- Powdered Potassium Feldspar:
- Ground to a fine powder for uniform distribution in welding consumable formulations.
- Blended Feldspar:
- Mixed with other feldspar types (e.g., soda feldspar) to balance potassium and sodium content for specific welding requirements.
Role of Potassium Feldspar in Welding Consumables
1. Covered Welding Electrodes
- Slag Formation:
- Potassium feldspar acts as a fluxing agent, helping to form a stable slag that protects the molten weld pool from atmospheric contamination.
- Arc Stabilization:
- Its potassium content improves electrical conductivity, resulting in a stable arc and smooth welding operation.
- Coating Strength:
- Enhances the mechanical strength of the electrode coating, reducing cracking and improving durability.
- Deoxidation:
- Removes oxygen from the weld pool, reducing porosity and inclusions in the weld.
2. Submerged Arc Welding Fluxes
- Slag Viscosity:
- Contributes to regulating slag viscosity, ensuring uniform coverage and easy removal after welding.
- Thermal Resistance:
- Its aluminosilicate content provides high thermal stability to the flux.
- Weld Metal Chemistry:
- Supplies trace amounts of potassium, which can influence the mechanical and chemical properties of the weld metal.
- Improved Arc Characteristics:
- Enhances the flux’s electrical properties, ensuring consistent current flow and better arc stability.
Effect on the Quality of Welding Electrodes and Fluxes
- Slag Formation:
- Produces a stable, protective slag that shields the weld pool and improves weld bead shape and appearance.
- Easy-to-remove slag reduces post-weld cleaning effort.
- Arc Stability:
- Potassium feldspar enhances arc stability, ensuring smooth welding with minimal spatter and better control.
- Weld Metal Purity:
- Its fluxing properties help in deoxidation, reducing oxygen inclusions and porosity.
- Mechanical Properties:
- Ensures a consistent weld bead with improved toughness, strength, and ductility.
- Coating Integrity:
- In welding electrodes, feldspar contributes to a stronger coating that resists cracking during handling and storage.
- Thermal Stability:
- In SAW fluxes, feldspar enhances the flux’s performance at high temperatures, maintaining its protective properties.
Key Considerations
- Purity:
- High-purity feldspar is essential to avoid impurities like iron or sulfur, which could negatively affect weld quality.
- Particle Size:
- Fine feldspar particles ensure uniform mixing and better performance in coatings and fluxes.
- Proportion in Formulation:
- Excessive feldspar can lead to excessive slag formation or overly fluid slag, complicating removal and affecting weld appearance.
- Blending with Other Materials:
- Potassium feldspar is often used in combination with other minerals, such as silica and alumina, to achieve the desired flux or coating properties.
Sodium Carboxymethyl Cellulose Powders Specifications and Their Effect on Welding Consumables
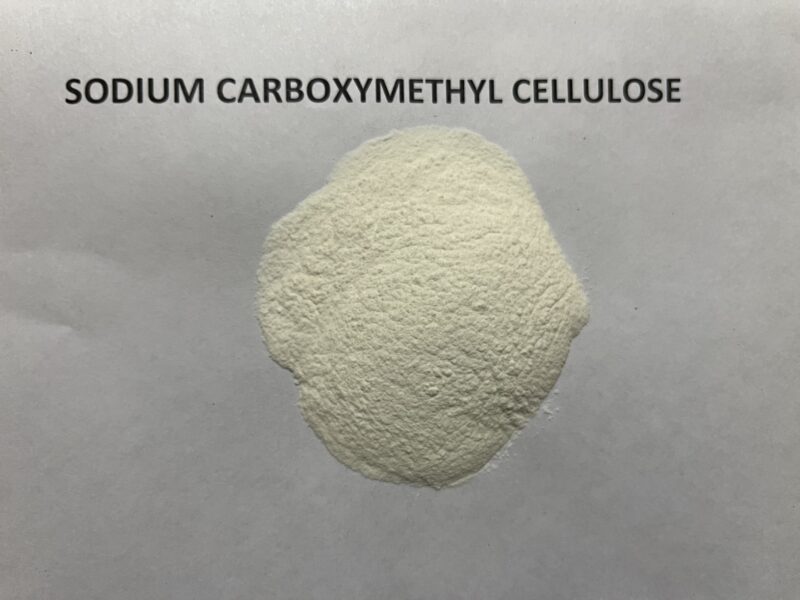
Sodium Carboxymethyl Cellulose (CMC) is a water-soluble cellulose derivative used in welding electrode coatings and sometimes in submerged arc welding (SAW) fluxes. It acts as a binder, thickener, and stabilizer, improving the consistency, adhesion, and workability of coatings and fluxes.
Sodium Carboxymethyl Cellulose (CMC) is a versatile additive in welding electrodes and SAW fluxes, serving as a binder, thickener, and stabilizer. It improves coating integrity, workability, and granule strength while contributing to consistent welding performance. By selecting the appropriate grade and controlling its usage, manufacturers can enhance the quality and reliability of their welding consumables.
Production of Sodium Carboxymethyl Cellulose
- Raw Materials:
- Derived from cellulose (cotton, wood pulp) and sodium hydroxide (NaOH).
- Chloroacetic acid (ClCH₂COOH) is used to introduce carboxymethyl groups.
- Manufacturing Process:
- Alkalization: Cellulose is treated with sodium hydroxide to produce alkali cellulose.
- Etherification: Alkali cellulose reacts with chloroacetic acid, substituting hydroxyl groups (-OH) in cellulose with carboxymethyl groups (-CH₂COONa).
- Purification:
- The product is washed to remove byproducts like sodium chloride (NaCl) and sodium glycolate.
- Drying and Milling:
- The purified CMC is dried and ground to the desired particle size.
- Grades Based on Purity and Viscosity:
- Technical Grade: Used in industrial applications like welding consumables.
- High-Purity Grade: Suitable for applications requiring minimal impurities.
- Viscosity Levels: Available in low, medium, and high viscosity grades for different applications.
Types of Sodium Carboxymethyl Cellulose
- Low-Viscosity CMC:
- Provides minimal thickening and is used where a thin coating or low viscosity is required.
- Medium-Viscosity CMC:
- Offers balanced properties for general welding applications.
- High-Viscosity CMC:
- Used for thickening and improving adhesion in coatings.
- Technical Grades:
- Contains moderate levels of impurities suitable for welding consumable applications.
Role of Sodium Carboxymethyl Cellulose in Welding Consumables
1. Covered Welding Electrodes
- Binder:
- Acts as a binder for coating materials, holding them together during electrode production and application.
- Moisture Retention:
- Prevents cracking and flaking of the coating during drying and storage.
- Thickener:
- Enhances the consistency of the coating slurry, improving uniformity and application control.
- Adhesion:
- Improves the adhesion of the coating to the electrode core wire.
- Burn-Off Behavior:
- Combusts cleanly during welding, minimizing residue in the weld pool.
2. Submerged Arc Welding Fluxes
- Binding Agent:
- In flux granulation, CMC acts as a temporary binder, ensuring that flux particles adhere during manufacturing.
- Granule Strength:
- Improves the mechanical strength of flux granules, reducing breakage during handling and application.
- Water Solubility:
- Provides controlled solubility in water, aiding in the granulation process.
Effect on the Quality of Welding Electrodes and Fluxes
- Coating Integrity:
- Enhances the strength and durability of the coating, preventing cracking or flaking during handling and storage.
- Workability:
- Improves the flow and application of the coating slurry, ensuring uniform coverage and consistent electrode quality.
- Moisture Resistance:
- Reduces susceptibility to moisture absorption, preventing hydrogen-induced defects like porosity and cracking in welds.
- Arc Stability:
- CMC burns off cleanly, contributing to stable arc characteristics and smooth welding.
- Slag Formation:
- Minimal impact on slag chemistry but ensures uniform coating, which indirectly contributes to consistent slag behavior.
- Granule Durability in SAW Fluxes:
- Prevents flux granules from breaking apart, ensuring consistent flux performance and weld quality.
Key Considerations
- Purity:
- Lower-purity grades may introduce impurities (e.g., sulfur or chlorine), potentially affecting weld quality.
- High-purity CMC is preferred for critical applications.
- Viscosity:
- The viscosity grade must match the specific application to achieve the desired consistency and binding strength.
- Proportion in Formulation:
- Excessive use can make coatings too sticky or difficult to handle, while insufficient amounts may lead to weak or brittle coatings.
- Moisture Control:
- Proper storage is necessary as CMC can absorb moisture, impacting its effectiveness and shelf life.